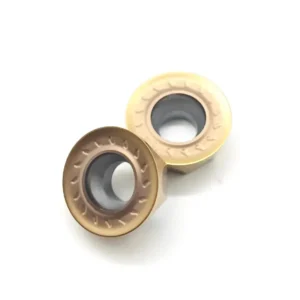
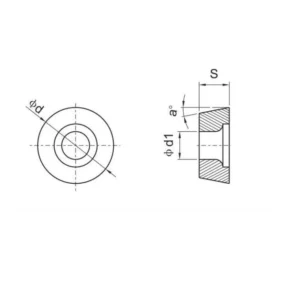
RPMT insert
Are you seeking cutting tools that deliver unmatched precision, durability, and versatility? RPMT inserts are engineered to meet the highest standards in machining, offering exceptional performance across various applications. Learn how RPMT inserts can transform your manufacturing processes and drive superior results.
- R: Indicates the shape of the insert, typically round in the case of RPMT inserts.
- P: Designates the insert’s tolerance class.
- M: Refers to the clamping method or chipbreaker style.
- T: Represents the thickness of the insert or specific features related to the design.
Why RPMT Are the Ideal Choice for Your Business
Exceptional Precision and Accuracy
RPMT inserts are designed with advanced geometries to ensure precise cutting and high accuracy in your machining operations. Their design guarantees that you achieve the exact specifications and tight tolerances required for high-quality outcomes.
Benefits:
- Achieve precise cuts and detailed results.
- Reduce the need for rework and corrections.
Superior Durability and Longevity
Constructed from high-quality carbide or cermet and equipped with advanced coatings, RPMT inserts are built to withstand demanding conditions. Their durability translates to a longer tool life and fewer insert changes.
Benefits:
- Endure high cutting forces and temperatures.
- Minimize tool replacements and associated downtime.
Versatile Applications
RPMT inserts are versatile and suited for a wide range of machining tasks, including:
- Turning Operations: Ideal for both roughing and finishing processes.
- Milling Operations: Effective for face milling, slotting, and profiling.
- Grooving and Parting: Suitable for internal and external grooving, as well as parting off operations.
Benefits:
- Adaptable to various materials and cutting conditions.
- Streamline your tool inventory by handling multiple applications.
Advanced Coatings and Materials
RPMT inserts come with high-grade coatings such as PVD (Physical Vapor Deposition) and CVD (Chemical Vapor Deposition), which enhance wear resistance and cutting performance. These coatings help reduce friction and improve tool efficiency.
Benefits:
- Improve tool longevity and performance.
- Ensure consistent results in diverse machining environments.
Choosing the Right RPMT Insert
To select the appropriate RPMT insert for your application, consider:
- Material: The type of material being machined (e.g., steel, stainless steel, cast iron).
- Operation Type: The specific machining operation (e.g., turning, milling, grooving).
- Cutting Conditions: Factors such as cutting speed, feed rate, and depth of cut.
- Insert Geometry and Coating: Choose based on required performance and application needs.
Our Production Capability

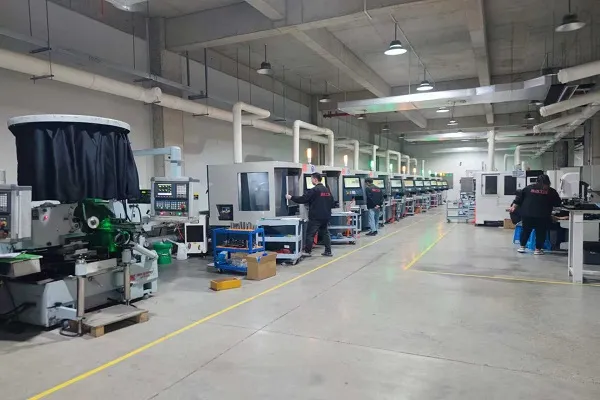



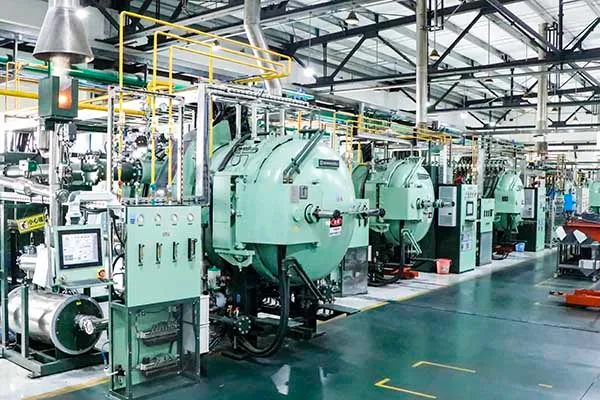

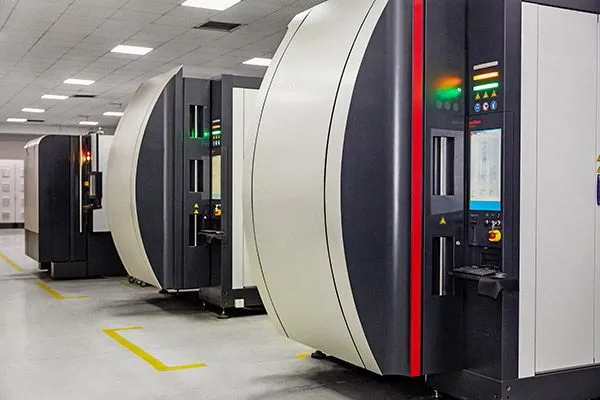

