Custom Carbide Inserts Manufacturing Service
Our Custom Carbide Inserts Manufacturing Service delivers precision-engineered carbide inserts and lathe form tools tailored to your needs. Designed for durability and efficiency, our solutions enhance performance in aerospace, automotive, and industrial applications. Trust us for high-quality, custom-crafted tools that optimize your machining processes.
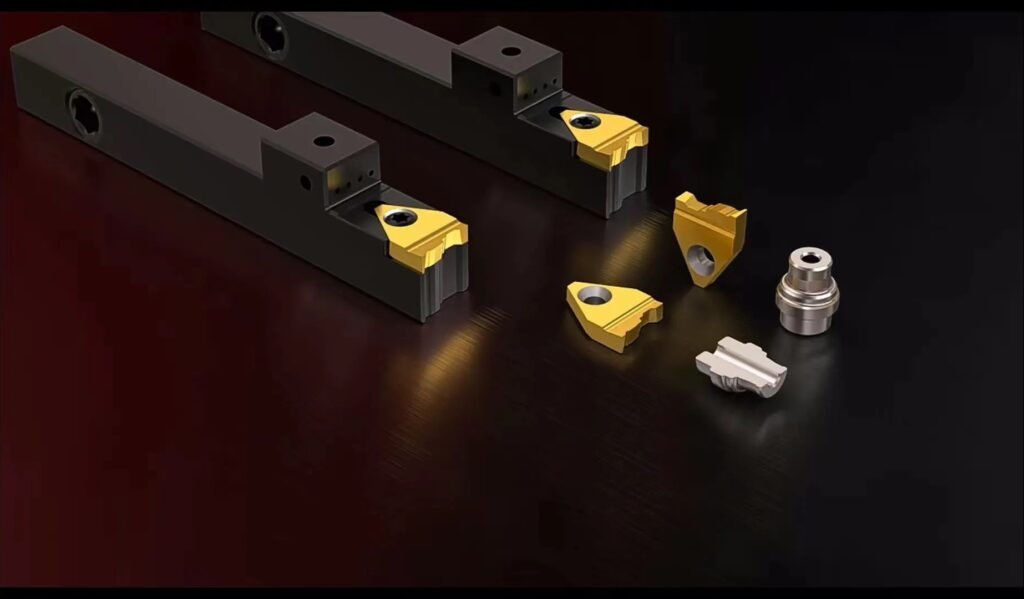
The Power of Precision
Are you ready to take your machining operations to the next level? Discover how custom carbide inserts can transform your productivity, precision, and profitability.
A. The Challenge of Modern Machining
In today's competitive manufacturing landscape, precision, efficiency, and cost-effectiveness are not just goals—they're necessities. As materials become more advanced and tolerances tighter, standard cutting tools often fall short of meeting these demanding requirements.
B. Introducing Custom Carbide Inserts: Your Competitive Edge
Enter the world of custom carbide inserts—a game-changing solution that's revolutionizing the machining industry. These tailored cutting tools are designed to meet your specific needs, offering unparalleled performance and opening new possibilities in manufacturing.
C. Why Standard Tools Fall Short
Off-the-shelf cutting tools are designed for general use, often leading to compromises in performance, tool life, and machining efficiency. In contrast, custom carbide inserts are engineered to excel in your unique applications, providing benefits that standard tools simply can't match.
Unleashing the Potential of Custom Carbide Inserts
A. What Are Custom Carbide Inserts?
Custom carbide inserts are specialized cutting tools tailored to meet specific machining requirements. Unlike standard inserts, these tools are designed with your unique needs in mind, optimizing geometry, material composition, and coating to deliver superior performance in your particular application.
B. The Science Behind Custom Cutting Tools
The power of custom carbide inserts lies in their precisely engineered design:
- Geometry: Cutting edges, chip breakers, and clearance angles are optimized for your specific machining operation.
- Material: Advanced carbide formulations provide the ideal balance of hardness and toughness for your application.
- Coatings: Specialized coatings enhance wear resistance, reduce friction, and improve heat dissipation.
C. Applications Across Industries
Custom carbide inserts are transforming machining operations across various sectors:
- Efficiently machine heat-resistant superalloys
- Achieve tight tolerances on critical components
- Increase productivity in large structural part production

D. Case Study: Productivity Transformed
A leading aerospace manufacturer struggled with tool life and surface finish when machining turbine blades from a nickel-based superalloy. By implementing custom carbide inserts, they achieved:
- 40% increase in tool life
- 25% reduction in cycle time
- Improved surface finish, meeting stringent quality requirements
These results highlight the transformative power of custom cutting tools in addressing specific machining challenges.
- Optimize high-volume production of engine components
- Improve surface finish on precision parts
- Enhance tool life in cast iron machining
- Achieve mirror finishes on implant components
- Efficiently machine difficult materials like titanium and cobalt-chrome
- Maintain strict tolerances for life-critical parts
- Improve tool life in tough downhole component machining
- Enhance performance in corrosion-resistant alloy cutting
- Optimize large-diameter turning operations
- Achieve superior surface finishes in hardened steel
- Improve efficiency in complex 3D milling operations
- Enhance tool life in abrasive material machining
The Advantages That Set You Apart
A. Precision Redefined
Custom carbide inserts take precision to new heights:
- Tighter Tolerances
- Achieve tolerances as tight as ±0.0001 inches consistently
- Maintain dimensional accuracy over longer production runs
- Reduce scrap rates and rework
- Superior Surface Finish
- Attain mirror-like finishes with Ra values as low as 0.1 μm
- Eliminate the need for secondary finishing operations
- Improve part functionality and aesthetics
- Complex Geometries Made Simple
- Machine intricate features with ease
- Reduce the number of operations required
- Achieve consistent results on challenging part designs
B. Efficiency Unleashed
Custom carbide inserts dramatically improve machining efficiency:
- Faster Machining Times
- Increase cutting speeds by up to 50%
- Optimize chip formation for smoother cutting action
- Reduce cycle times and increase throughput
- Reduced Setup and Changeover
- Minimize the number of tool changes required
- Streamline your tooling inventory
- Decrease machine downtime for tool adjustments
- Longer Tool Life
- Extend insert life by 2-3 times compared to standard tools
- Reduce frequency of tool changes
- Lower overall tooling costs

C. Cost-Effectiveness: The Bottom Line
Investing in custom carbide inserts pays dividends:
- Reduced Material Waste
- Optimize material removal rates
- Decrease instances of scrapped parts
- Improve yield from raw material stock
- Energy Savings
- Lower power consumption through optimized cutting action
- Reduce machine run time for each part
- Decrease overall energy costs in your operation
- Decreased Downtime
- Minimize unplanned stoppages due to tool failure
- Reduce time spent on tool changes and adjustments
- Increase overall equipment effectiveness (OEE)
D. Customization: Your Unique Edge
Tailor your cutting tools to your exact needs:
- Tailored Geometries
- Design cutting edges optimized for your specific operations
- Create custom chip breakers for ideal chip control
- Develop special profiles for unique part features
- Specialized Coatings
- Select coatings that excel in your particular application
- Combine multiple coating layers for optimum performance
- Enhance wear resistance, heat dissipation, and lubricity
- Material Innovations
- Choose from a wide range of carbide grades
- Explore advanced substrates for extreme applications
- Benefit from ongoing research in cutting tool materials

Partner with Us for Cutting-Edge Solutions
A. Our Expertise in Custom Carbide Inserts
Leverage our decades of experience and cutting-edge capabilities:
- State-of-the-Art Design Process
- Advanced CAD/CAM systems for precise insert modeling
- Finite Element Analysis (FEA) for optimized performance
- Virtual machining simulations to predict real-world results
- Cutting-Edge Manufacturing Capabilities
- Latest CNC grinding technology for complex geometries
- Advanced sintering processes for superior material properties
- State-of-the-art coating equipment for enhanced performance
- Rigorous Quality Control
- 100% inspection of critical dimensions
- Automated optical measurement systems
- Extensive testing under simulated machining conditions
B. Collaborative Approach: Your Success is Our Priority
We work hand-in-hand with you to develop the perfect solution:
- Consultation and Needs Assessment
- In-depth analysis of your machining challenges
- Comprehensive review of your current processes
- Identification of key areas for improvement
- Prototype Development and Testing
- Rapid prototyping of custom insert designs
- In-house testing to validate performance
- On-site trials in your actual production environment
- Continuous Optimization
- Ongoing support to fine-tune insert performance
- Regular check-ins to ensure continued satisfaction
- Proactive suggestions for further improvements
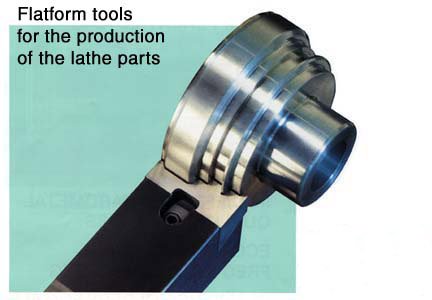
C. Success Stories: Real Results from Real Clients
Don’t just take our word for it. Here’s what our clients have achieved:
- Automotive supplier increased tool life by 300% and reduced cycle time by 20%
- Aerospace manufacturer improved surface finish quality by 50% while reducing tooling costs
- Medical device company achieved consistent 0.0005″ tolerances on complex titanium parts
Carbide Insert Design
Key Aspects of Carbide Insert Design
- Geometry:
- Shape: Inserts come in various shapes (e.g., triangular, square, round, diamond, or rhombic), each suited for specific applications. For example:
- Round inserts: Ideal for high-feed milling or contouring.
- Square inserts: Used for general-purpose milling or turning with strong cutting edges.
- Triangular inserts: Common for turning, offering versatility with multiple cutting edges.
- Rake Angle: The angle of the cutting face affects chip formation and cutting forces. Positive rake angles reduce cutting forces and are used for softer materials, while negative rake angles provide stronger edges for harder materials or heavy cuts.
- Clearance Angle: The angle between the insert’s flank and the workpiece prevents rubbing and ensures smooth cutting. Typically 5°–15°, depending on the application.
- Nose Radius: The rounded tip of the insert impacts surface finish and strength. Smaller radii are used for precision and light cuts, while larger radii handle heavier cuts but may increase vibration.
- Shape: Inserts come in various shapes (e.g., triangular, square, round, diamond, or rhombic), each suited for specific applications. For example:
- Chip Breaker Design:
- Chip breakers are grooves or features on the insert’s top surface that control chip formation, directing chips away from the workpiece to prevent damage and improve safety. Designs vary based on material and cutting conditions:
- Light-duty chip breakers: For low-feed rates and soft materials.
- Heavy-duty chip breakers: For high-feed rates and tougher materials like stainless steel.
- Chip breaker geometry is tailored to specific feeds, depths of cut, and material types (e.g., steel, aluminum, or titanium).
- Chip breakers are grooves or features on the insert’s top surface that control chip formation, directing chips away from the workpiece to prevent damage and improve safety. Designs vary based on material and cutting conditions:
- Material and Coating:
- Base Material: Tungsten carbide provides the core hardness, with cobalt (typically 6–12%) enhancing toughness. The carbide grain size (submicron to coarse) influences hardness and toughness trade-offs.
- Coatings: Applied via techniques like Chemical Vapor Deposition (CVD) or Physical Vapor Deposition (PVD), coatings enhance wear resistance and reduce friction. Common coatings include:
- Titanium Nitride (TiN): General-purpose, wear-resistant.
- Titanium Carbonitride (TiCN): For high-speed cutting.
- Aluminum Oxide (Al2O3): For high-temperature applications.
- Diamond-like coatings: For non-ferrous materials like aluminum.
- Multi-layer coatings combine properties for versatility across materials and conditions.
- Mounting and Clamping Features:
- Inserts are designed with holes, chamfers, or countersinks for secure mounting on tool holders. Common mounting styles include:
- Screw-on: A central hole for screw attachment.
- Clamp-on: Held by a clamp without a hole, often for negative rake inserts.
- The insert’s base geometry (flat or with locating features) ensures precise positioning and stability during cutting.
- Inserts are designed with holes, chamfers, or countersinks for secure mounting on tool holders. Common mounting styles include:
- Edge Preparation:
- Cutting edges may be honed (slightly rounded) or chamfered to increase edge strength and prevent chipping, especially for interrupted cuts or hard materials.
- Sharp edges are used for soft materials or finishing operations to minimize cutting forces and improve surface finish.
- Insert Size and Thickness:
- Inserts are sized based on the inscribed circle (IC) diameter or edge length, affecting cutting depth and stability. For example, a larger IC (e.g., 12 mm) is used for heavy machining.
- Thickness impacts rigidity, with thicker inserts suited for high-force applications.
Design Standards and Coding
- ISO/ANSI Standards: Inserts are standardized (e.g., ISO 1832) with a code system describing shape, size, tolerance, and features. For example, a code like CNMG 120408 indicates:
- C: Shape (rhombic, 80°).
- N: Clearance angle (0°, neutral).
- M: Tolerance class.
- G: Chip breaker and mounting style.
- 12: IC size (12 mm).
- 04: Thickness (4 mm).
- 08: Nose radius (0.8 mm).
- These codes help machinists select inserts for specific tools, materials, and operations.
Applications and Design Considerations
- Material-Specific Designs: Inserts are optimized for materials like steel, cast iron, aluminum, or superalloys. For example:
- Aluminum requires sharp edges and polished surfaces to prevent material buildup.
- Hardened steels need tough inserts with negative rake angles and robust coatings.
- Cutting Conditions: Designs account for speed, feed rate, and depth of cut. High-speed machining may use PVD-coated inserts, while heavy roughing uses thicker, CVD-coated inserts.
- Sustainability: Modern designs focus on multi-edge inserts (e.g., triangular inserts with six usable edges) to reduce waste and cost.
Take the Next Step: Request a Custom Quote
Our team of application engineers is ready to answer any additional questions you may have. Don’t hesitate to reach out for personalized advice on how custom carbide inserts can benefit your specific operation.
Ready to experience the power of custom carbide inserts? Here’s how to get started:
- What Information We Need
- Details about your machining operation (materials, tolerances, volumes)
- Current challenges or limitations you’re facing
- Specific goals you want to achieve
- Our Response Time Guarantee
- Initial response within 24 hours
- Detailed proposal within 5 business days
- Prototype development timeline provided upfront
- No-Obligation Consultation
- Free initial assessment of your needs
- Transparent pricing and ROI projections
- Flexible engagement options to suit your requirements