Precision Customization - Your Special Carbide Tools Expert
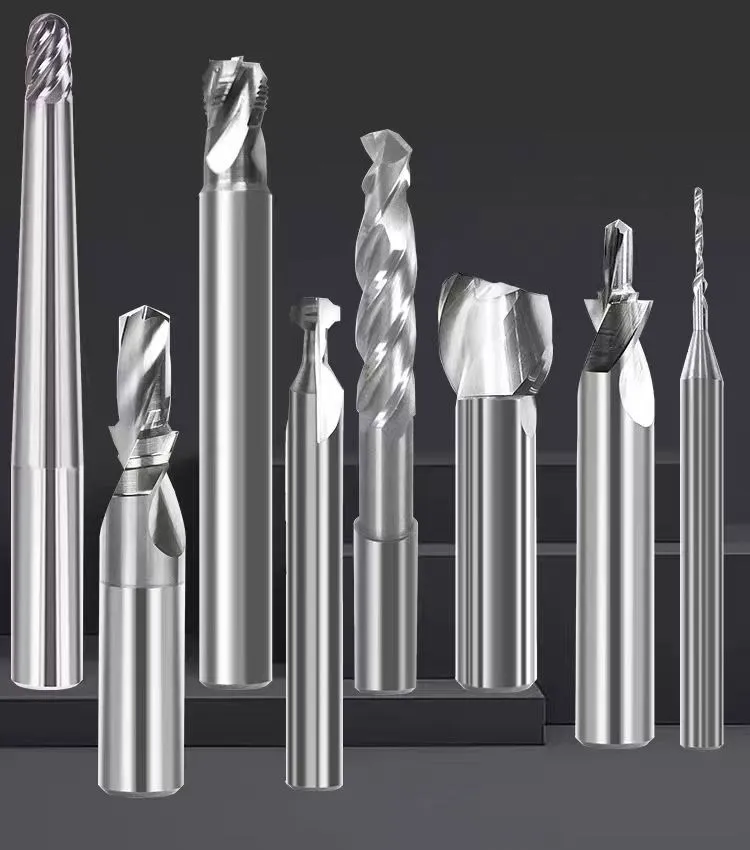
Our core special carbide tools include:
- Custom Carbide Inserts: Tailored to your specific applications with optimized geometry, coating technology, and cutting parameters
- Custom End Mills: Designed with specialized cutting edges, helix angles, and chip flutes to ensure optimal cutting performance
- Carbide Form Tools: Engineered for precision form machining, enabling single-pass complex profile generation. Ideal for various grooves, slots, splines, and other intricate surface machining, delivering superior accuracy and surface finish
Through advanced manufacturing technology and stringent quality control systems, our special carbide tools deliver:
- Significant improvement in machining efficiency
- Extended tool life
- Guaranteed machining precision
- Reduced production costs

The Advantages That Set You Apart
A. Precision Redefined
Custom carbide inserts take precision to new heights:
- Tighter Tolerances
- Achieve tolerances as tight as ±0.0001 inches consistently
- Maintain dimensional accuracy over longer production runs
- Reduce scrap rates and rework
- Superior Surface Finish
- Attain mirror-like finishes with Ra values as low as 0.1 μm
- Eliminate the need for secondary finishing operations
- Improve part functionality and aesthetics
- Complex Geometries Made Simple
- Machine intricate features with ease
- Reduce the number of operations required
- Achieve consistent results on challenging part designs
B. Efficiency Unleashed
Custom carbide inserts dramatically improve machining efficiency:
- Faster Machining Times
- Increase cutting speeds by up to 50%
- Optimize chip formation for smoother cutting action
- Reduce cycle times and increase throughput
- Reduced Setup and Changeover
- Minimize the number of tool changes required
- Streamline your tooling inventory
- Decrease machine downtime for tool adjustments
- Longer Tool Life
- Extend insert life by 2-3 times compared to standard tools
- Reduce frequency of tool changes
- Lower overall tooling costs

C. Cost-Effectiveness: The Bottom Line
Investing in custom carbide inserts pays dividends:
- Reduced Material Waste
- Optimize material removal rates
- Decrease instances of scrapped parts
- Improve yield from raw material stock
- Energy Savings
- Lower power consumption through optimized cutting action
- Reduce machine run time for each part
- Decrease overall energy costs in your operation
- Decreased Downtime
- Minimize unplanned stoppages due to tool failure
- Reduce time spent on tool changes and adjustments
- Increase overall equipment effectiveness (OEE)
D. Customization: Your Unique Edge
Tailor your cutting tools to your exact needs:
- Tailored Geometries
- Design cutting edges optimized for your specific operations
- Create custom chip breakers for ideal chip control
- Develop special profiles for unique part features
- Specialized Coatings
- Select coatings that excel in your particular application
- Combine multiple coating layers for optimum performance
- Enhance wear resistance, heat dissipation, and lubricity
- Material Innovations
- Choose from a wide range of carbide grades
- Explore advanced substrates for extreme applications
- Benefit from ongoing research in cutting tool materials

Partner with Us for Cutting-Edge Solutions
A. Our Expertise in special carbide tools
Leverage our decades of experience and cutting-edge capabilities:
- State-of-the-Art Design Process
- Advanced CAD/CAM systems for precise insert modeling
- Finite Element Analysis (FEA) for optimized performance
- Virtual machining simulations to predict real-world results
- Cutting-Edge Manufacturing Capabilities
- Latest CNC grinding technology for complex geometries
- Advanced sintering processes for superior material properties
- State-of-the-art coating equipment for enhanced performance
- Rigorous Quality Control
- 100% inspection of critical dimensions
- Automated optical measurement systems
- Extensive testing under simulated machining conditions
B. Collaborative Approach: Your Success is Our Priority
We work hand-in-hand with you to develop the perfect solution:
- Consultation and Needs Assessment
- In-depth analysis of your machining challenges
- Comprehensive review of your current processes
- Identification of key areas for improvement
- Prototype Development and Testing
- Rapid prototyping of custom insert designs
- In-house testing to validate performance
- On-site trials in your actual production environment
- Continuous Optimization
- Ongoing support to fine-tune insert performance
- Regular check-ins to ensure continued satisfaction
- Proactive suggestions for further improvements
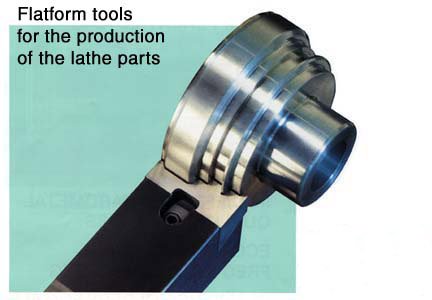
C. Success Stories: Real Results from Real Clients
Don’t just take our word for it. Here’s what our clients have achieved:
- Automotive supplier increased tool life by 300% and reduced cycle time by 20%
- Aerospace manufacturer improved surface finish quality by 50% while reducing tooling costs
- Medical device company achieved consistent 0.0005″ tolerances on complex titanium parts
Frequently Asked Questions
Common Questions About special carbide tools
Typically, 2-4 weeks from initial consultation to prototype delivery.
While the initial cost may be higher, custom inserts often provide significant ROI through improved productivity and longer tool life.
In many cases, yes. We can design inserts with re-sharpening in mind to extend their usable life even further.
We offer a performance guarantee. If the insert doesn’t meet agreed-upon specifications, we’ll refine the design at no additional cost.
If you’re facing challenges with tool life, surface finish, or machining efficiency, custom inserts could likely help. Contact us for a free assessment.
Take the Next Step: Request a Custom Quote
Our team of application engineers is ready to answer any additional questions you may have. Don’t hesitate to reach out for personalized advice on how custom carbide inserts can benefit your specific operation.
Ready to experience the power of custom carbide inserts? Here’s how to get started:
- What Information We Need
- Details about your machining operation (materials, tolerances, volumes)
- Current challenges or limitations you’re facing
- Specific goals you want to achieve
- Our Response Time Guarantee
- Initial response within 24 hours
- Detailed proposal within 5 business days
- Prototype development timeline provided upfront
- No-Obligation Consultation
- Free initial assessment of your needs
- Transparent pricing and ROI projections
- Flexible engagement options to suit your requirements