Back spot face tool
- Reduce chip cutting time by at least 80% compared to traditional hand tools
- Eliminates costly secondary operations and saves time through clever process improvements
- Standard carbide indexable inserts accommodate a wide range of materials and reduce material costs
- Tool allows heavy interrupted cuts without excessive chattering
- Minimum pilot hole diameter Ø10.4mm
- Unlimited depth-to-diameter ratio with support guides
- Easy and quick tool change
- Maximum backbore diameter up to 1.6 times the boring diameter
- Backspot countersinks with chamfering are available.
- Use SKD61 material, more shock-resistant, more wear-resistant and more stable.
- Also easy check our automatic back spot facing tools
Applications
- Bolt head seating faces
- Differential cases – spherical and flat
- Valve seat pocketing
- Gate valves
- Planetary gear carriers
- Gearbox casings
- Landing gear
- Special inserts with chamfer and other forms on request
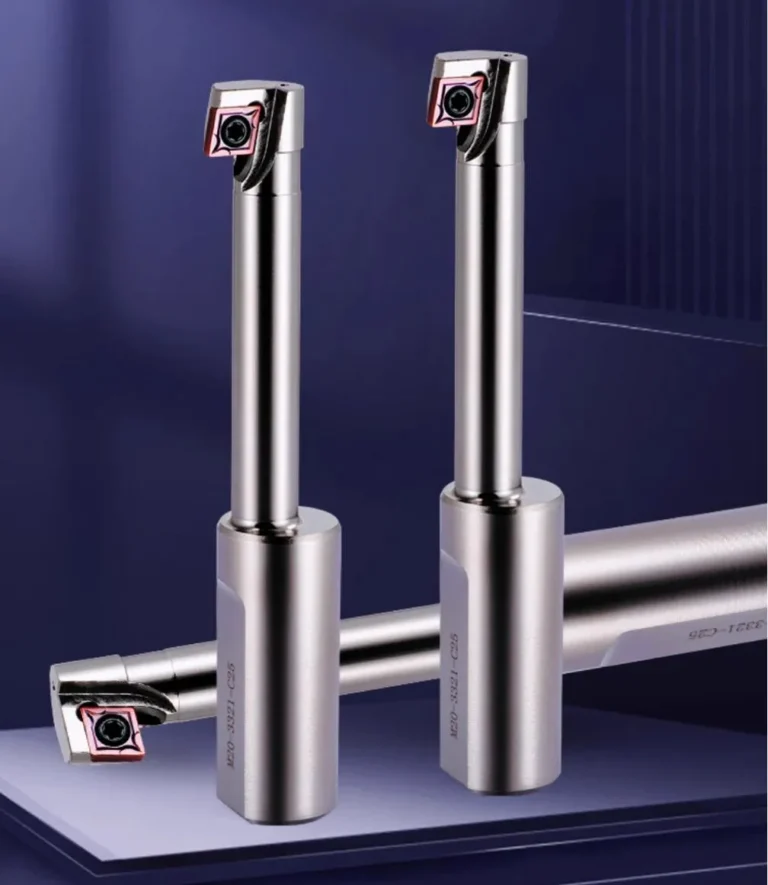
- Ø10.4mm minimum pilot hole
- Robust and versatile
- Back spotface, counterbore chamfer
- Back chamfer tool for vmc
- Works on interupted surfaces
Easy NC Programming
Easy programming by simply offsetting the centers between the machine spindle and hole.
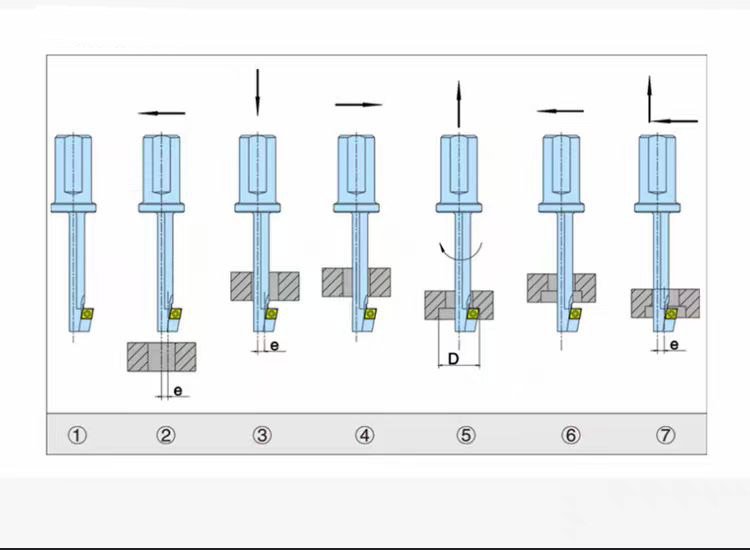
Eccentric grinding process
Under the premise of ensuring rigidity, the use of eccentric grinding process can effectively avoid the empty.
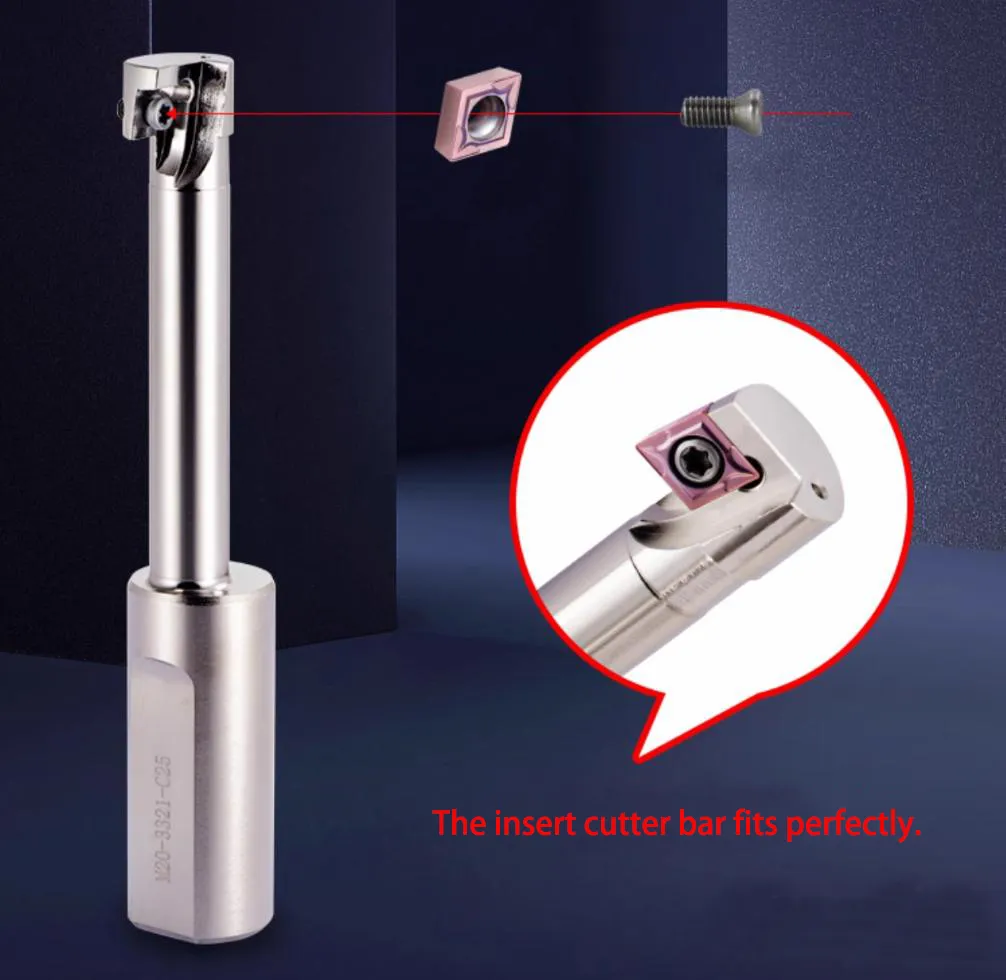
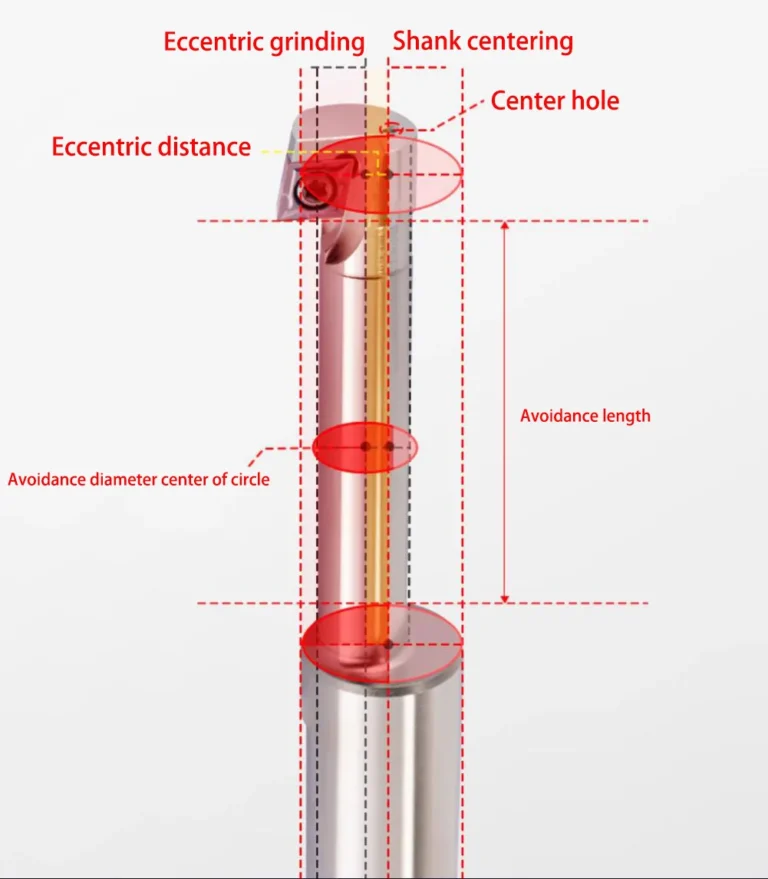
Well designed
Precision crafted, screw off-set design, blades are mounted without gaps for enhanced rigidity. Avoid blade loss caused by vibration, better machining effect.
Eccentric back spot face hole
Solve the processing pain points, processing the back countersunk holes do not need to turn the surface, greatly improving processing efficiency

Rust and corrosion prevention
Electroplating treatment, so that the product is corrosion-resistant, wear-resistant, oxidation-resistant, the blade and the cutter bar close fit, high tightness, comprehensive precision better

Side fastening clamping method
The surface of the toolholder is milled parallel and flat, which makes the clamping force stronger and less slippery during machining.
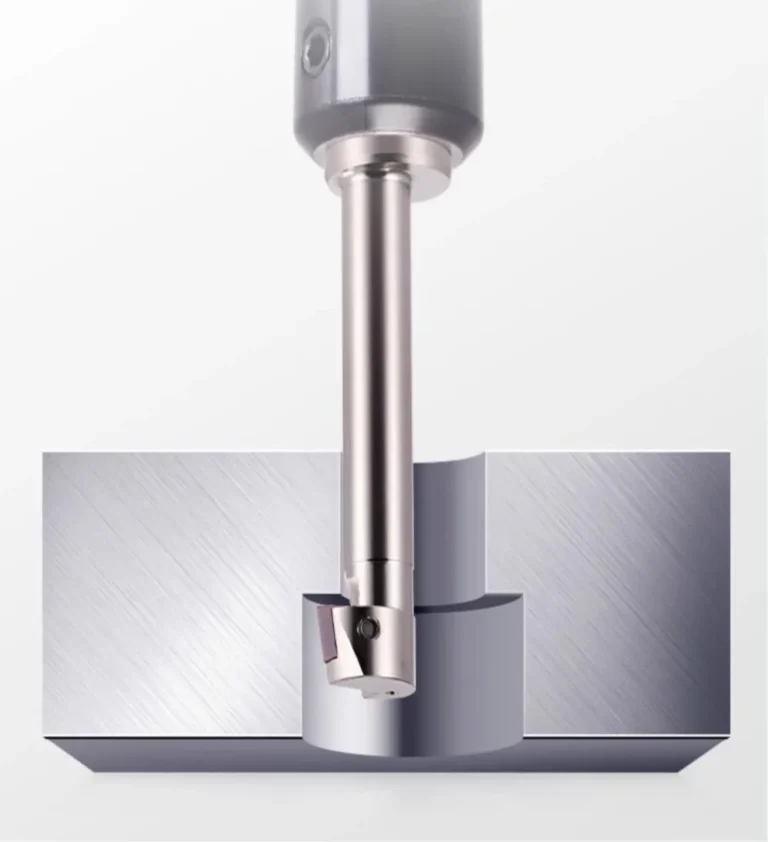
Replaceable standard inserts
Interchangeable CCMT inserts reduce processing costs

Clear specification branding
Laser engraving for clearer specification branding
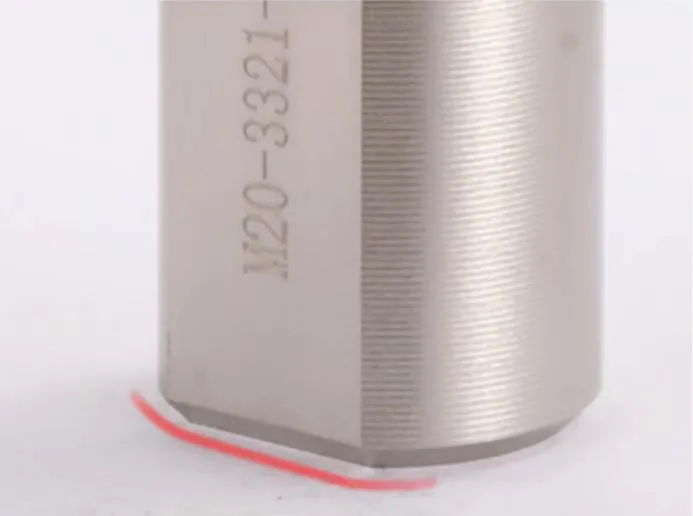
Back spot face tool Model Description

Cutter model | Rotating diameter( ΦDc) | Head diameterΦDc1 | L1 | L2 | Total Length(L) | Shank diameter(ΦDs) | Depth of cut(ap) | Carbide insert | Screw | Wrench |
---|---|---|---|---|---|---|---|---|---|---|
M10-1810-C16 | 18 | 10.4 | 53 | 40 | 95 | 16 | 4 | CCMT160204 | M2.5*6 | T8 |
M12-2013-C16 | 20 | 12.4 | 53 | 40 | 100 | 16 | 4 | |||
M14-2315-C16 | 23 | 14.2 | 63 | 50 | 110 | 16 | 4.5 | CCMT09T304 | M4*9 | T15 |
M16-2617-C20 | 26 | 16.4 | 86 | 68 | 150 | 20 | 5 | |||
M20-3321-C25 | 33 | 20.7 | 88 | 75 | 150 | 25 | 5.5 | |||
M24-4025-C25 | 40 | 24.6 | 90 | 78 | 150 | 25 | 8 |
Recommended cutting conditions
ISO | Workpiece | Hardness | Cutting speed(M/Min)Min-Suit-Max | Feed(mm/t)Min-Suit-Max |
---|---|---|---|---|
P | General steel | 180-280HB | 100/150/200 | 0.05/0.15/0.2 |
Mould Steel | 180-281HB | 100/150/200 | 0.05/0.1/0.15 | |
M | Martensitic stainless steel | 200-330HB | 100/150/200 | 0.05/0.15/0.2 |
Austenitic stainless steel | 200HB | 80/130/160 | 0.05/0.1/0.15 | |
K | Cast steel | 250HB | 100/150/200 | 0.05/0.15/0.25 |
N | High temperature alloys | / | 200/300/350 | 0.05/0.15/0.25 |
S | Titanium alloy | / | 30/40/60 | 0.03/0.05/0.08 |
Note: The above cutting conditions are approximate benchmarks and need to be adjusted according to mechanical rigidity and workpiece rigidity, depth of cut, and so on. |
Interested To Our back spot face tool?
ONMY Toolings is growing rapidly these years, and we are always welcome partners to work together to achieve manual benifits and grow together!