"Твердые пластины из КНБ для твердого точения с высокой износостойкостью, хорошей термостойкостью и отличным качеством поверхности. При обработке таких материалов, как закаленная сталь, чугун и высокотемпературные сплавы, использование пластин из твердого КНБ позволяет повысить эффективность и точность обработки, а также продлить срок службы инструмента. В этой статье мы расскажем о преимуществах, сценариях применения и методах выбора пластин из твердого КНБ, чтобы помочь читателю лучше понять применение пластин из твердого КНБ при токарной обработке твердых материалов."



Рекомендуемые параметры обработки материала для цельных пластин из КНБ | |||||
Материал заготовки | Твердость | Скорость резки (м/мин) | Скорость подачи (мм/об) | Cскорость утяжки (мм) | |
Серый чугун | HB170~230 | 500~1500 | 0.1~0.4 | 0.1~1.5 | |
Ковкий чугун | HB240~300 | 200~400 | 0.1~0.4 | 0.1~1.5 | |
Легированный чугун | HB240~300 | 150~300 | 0.05~0.4 | 0.1~1.5 | |
Сплавы на основе железа | HRC45~50 | 50~150 | 0.05~0.4 | 0.05~0.5 | |
Закаленная сталь | HRC45~65 | 80~200 | 0.05~0.2 | 0.05~0.2 | |
Жаропрочные сплавы | / | 50~200 | 0.05~0.2 | 0.05~0.2 |
Важность использования правильных режущих инструментов для работы с твердыми материалами
Использование правильных режущих инструментов для обработки твердых материалов имеет большое значение для качества и эффективности обработки. Твердые материалы, такие как закаленные стали, чугун и высокотемпературные сплавы, часто обладают высокой твердостью и износостойкостью, что затрудняет их обработку. Использование неподходящих режущих инструментов может привести к снижению качества обработки, увеличению сил резания и сокращению срока службы режущего инструмента. Напротив, использование режущих инструментов, специально разработанных для обработки твердых материалов, таких как цельные пластины из КНБ, может значительно повысить эффективность и точность обработки, одновременно продлевая срок службы режущего инструмента.
Ниже приведен краткий перечень преимуществ и недостатков различных типов инструментов, предназначенных для работы с различными твердыми материалами.
Тип режущего инструмента | Обрабатываемые материалы | Преимущества | Недостатки |
Твердые пластины из КНБ | Закаленная сталь, высокотемпературные сплавы, керамика и т.д. | Высокая твердость, износостойкость и отличная термостойкость; Подходит для высокоскоростной резки и сухой резки; Высокая точность и хорошее качество поверхности. | Дорогой; хрупкий, подвержен сколам и трещинам. |
Цементированные твердосплавные вставки | Чугун, алюминиевые сплавы, титановые сплавы, нержавеющая сталь и т.д. | Хорошая вязкость, износостойкость и коррозионная стойкость; Подходит для черновой и чистовой обработки, относительно недорогая. | Не подходит для высокоскоростной резки, подвержена термическому растрескиванию; Сложно обрабатывать сверхтвердые материалы. |
Керамические вставки | Высокотемпературные сплавы, керамика, стекло и т.д. | Высокая твердость, износостойкость, жаропрочность и химическая стабильность; подходит для высокотемпературной резки и сухой резки; высокая точность и хорошее качество поверхности. | Хрупкая, склонная к сколам и трещинам, не подходит для прерывистой резки. |
Пластины PCD | Цементированный карбид, армированные волокном пластики, композитные материалы и т.д. | Высокая твердость, износостойкость и отличная теплопроводность; Подходит для высокоскоростной резки и сухой резки; Относительно недорогой. | Склонны к сколам и трещинам; Не подходят для обработки неметаллических материалов. |
Алмазные вставки | Керамика, стекло, полупроводниковые материалы и т.д. | Высокая твердость, износостойкость и химическая стабильность; Подходит для сверхточной резки и полировки; Высокая эффективность обработки. | Дорогой; хрупкий, подвержен сколам и трещинам. |
Режущие инструменты из высокоскоростной стали | Чугун, нержавеющая сталь, алюминиевые сплавы и т.д. | Хорошая вязкость, износостойкость и теплопроводность; Подходит для общей резки. | Непригоден для высокоскоростной резки; подвержен износу и деформации. |
Примечание: Преимущества и недостатки, перечисленные в таблице, приведены только для справки. В реальных условиях применения необходимо всесторонне учитывать множество факторов, таких как условия обработки, параметры резания и форма заготовки.
Что такое цельная пластина из КНБ?
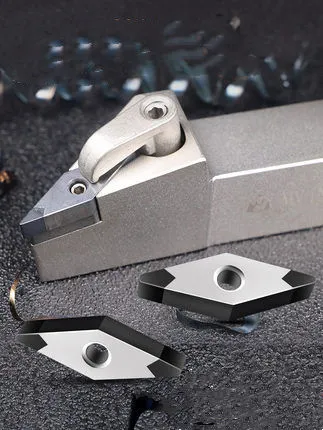
CBN - это аббревиатура от "кубический нитрид бора", который представляет собой сверхтвердый материал, уступающий по твердости только алмазу. КНБ обладает высокой твердостью, высокой термической стабильностью, высокой химической стабильностью, высокой теплопроводностью и другими превосходными свойствами и широко используется в областях резки и обработки, таких как автомобилестроение, авиация, аэрокосмическая промышленность, пресс-формы и так далее.
Преимущества цельных пластин из КНБ:
1. Высокая твердость КНБ 90% тверже алмаза и более чем в 5 раз тверже других инструментальных материалов.
2. Высокая термическая стабильность КНБ остается стабильным в высокотемпературных средах, не размягчается и не деформируется.
3. Высокая химическая стабильность КНБ обладает хорошей коррозионной и химической стойкостью.
4. Высокая теплопроводность КНБ более чем в 4 раза превышает теплопроводность стали и может эффективно отводить тепло, выделяемое при обработке.
Области применения твердых пластин из КНБ:
1. Автомобильная промышленность для обработки блоков цилиндров, головок цилиндров, коленчатых валов и т.д.
2. В аэрокосмической промышленности используется для обработки лопаток авиадвигателей, лопаток турбин и т.д.
3. Производство пресс-форм для обработки пластиковых форм, форм для литья под давлением и т.д.
4. Механическая обработка для эффективной обработки различных металлических материалов.
Виды резки КНБ:
Инструменты CBN выпускаются в двух основных видах: однокромочные и многокромочные.
1. Инструменты с одной кромкой CBN подходят для обработки твердых материалов, таких как легированная сталь, нержавеющая сталь, быстрорежущая сталь и т.д.
2. Многогранные инструменты CBN подходят для обработки большого количества заготовок, таких как чугун, медь, алюминий и т.д. Многогранные инструменты CBN высокоэффективны в обработке, но качество резания относительно низкое.
Каковы основные показатели высокой твердости Материалы, для обработки которых подходят пластины из твердого КНБ?
- Закаленная сталь: например, быстрорежущая сталь, штамповая сталь и инструментальная сталь.
- Чугун: например, серый чугун, ковкий чугун и белый чугун.
- Высокотемпературные сплавы: например, титановые сплавы, сплавы на основе никеля и хромомолибденовые сплавы.
- Твердые сплавы: такие как вольфрамо-кобальтовые сплавы и вольфрамо-молибдено-кобальтовые сплавы.
- Керамические материалы: глинозем, нитрид кремния и диоксид циркония.
Твердые пластины из КНБ хорошо подходят для обработки этих материалов благодаря своей чрезвычайно высокой твердости и износостойкости, а также способности сохранять стабильность и долговечность в условиях обработки при высоких температурах и давлении. Однако из-за высокой цены пластин из твердого КНБ они обычно используются только для сложных задач обработки.
Примеры отраслей, где обычно используются цельные пластины из КНБ:
Обрабатывающая промышленность: Твердые пластины CBN широко используются в обрабатывающей промышленности для прецизионной обработки и обработки пресс-форм, таких как обработка деталей автомобилей, обработка деталей двигателей, обработка деталей авиационных двигателей, прецизионная обработка пресс-форм и т.д.

Аэрокосмическая промышленность: Твердые пластины CBN также широко используются в аэрокосмической промышленности, в основном для обработки деталей из высокотемпературных сплавов, титановых сплавов и других материалов.

Электронная промышленность: Твердые пластины из КНБ также могут использоваться для обработки полупроводниковых материалов, оптического стекла и других прецизионных материалов, например, для обработки светодиодных чипов, оптических линз и т.д.
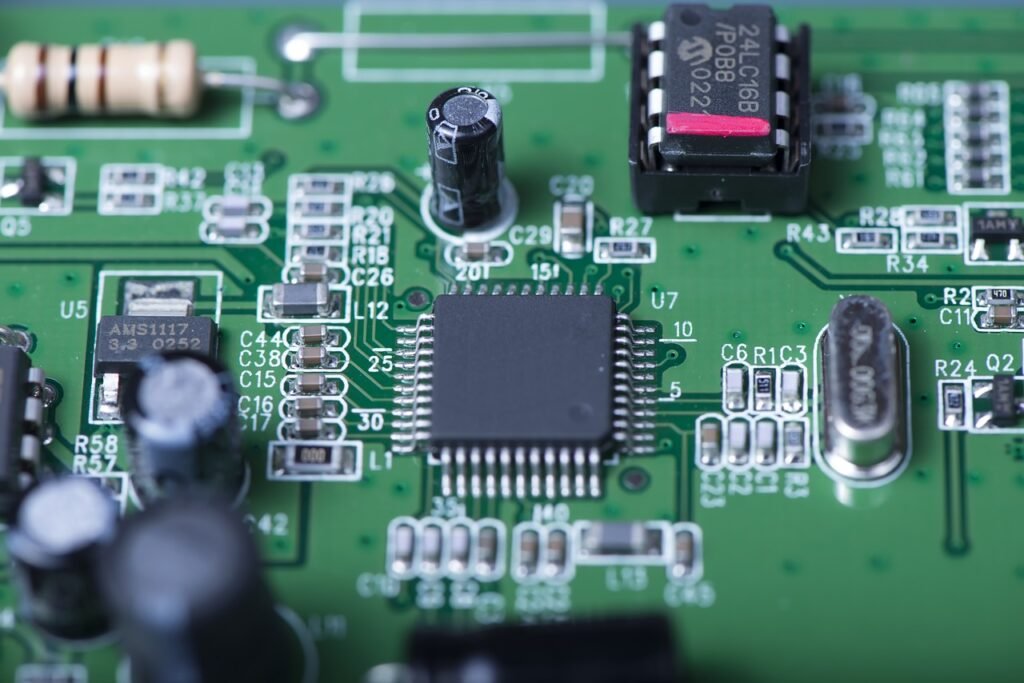
Энергетическая промышленность: Твердые пластины из КНБ также используются в энергетической промышленности, в основном для обработки таких компонентов, как оборудование для добычи нефти и буровые инструменты.
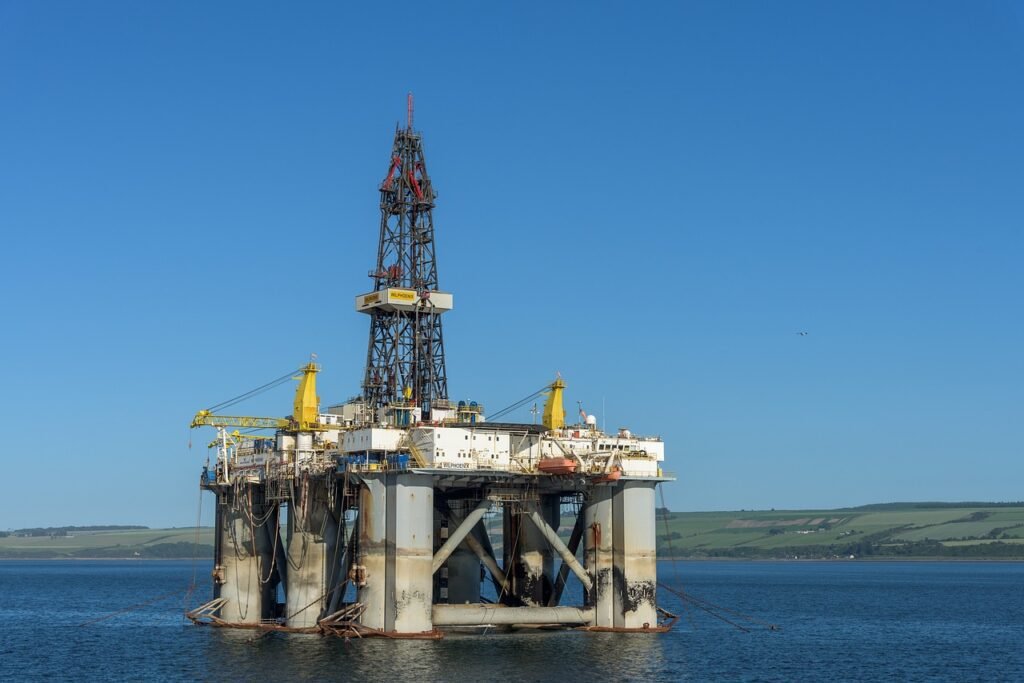
Несколько ключевых моментов для обслуживания твердых пластин из КНБ:
a. Настройка параметров резания: Параметры резания для цельных пластин CBN должны быть установлены в соответствии с твердостью, формой и размером обрабатываемого материала, чтобы обеспечить наилучшие результаты резания и срок службы. Как правило, скорость резания пластин CBN должна находиться в диапазоне 200-500 м/мин, а скорость подачи - в диапазоне 0,05-0,2 мм/об.
b. Выбор и использование СОЖ: Обработка пластин из твердого КНБ требует использования соответствующей охлаждающей жидкости для снижения температуры резания и трения, а также для уменьшения термического повреждения и износа инструмента. Как правило, можно использовать либо водорастворимую смазочно-охлаждающую жидкость, содержащую смазочные материалы и ингибиторы ржавчины, либо смазочно-охлаждающую жидкость на масляной основе.
c. Установка и настройка инструмента: Установка цельных пластин CBN требует внимания к ориентации и положению инструмента для обеспечения правильного угла резания и направления резания пластины. Также необходимо отрегулировать силу зажима инструмента и его высоту, чтобы обеспечить стабильность и точность резания.
d. Уход и обслуживание инструмента: В процессе использования цельных пластин CBN необходимо регулярно проверять и чистить инструмент, чтобы убедиться, что его поверхность чистая и без царапин. Кроме того, необходимо следить за тем, чтобы избежать столкновений и чрезмерного износа инструмента, чтобы продлить срок его службы.
e. Правильное хранение и защита: Твердые пластины CBN необходимо хранить в сухом, чистом и непыльном помещении, чтобы избежать коррозии и загрязнения поверхности инструмента. Также следует обращать внимание на защиту инструмента от влаги и ударов, чтобы избежать повреждения или деформации
Вот несколько популярных проблем, которые могут вам помочь.
Каков процесс производства твердых пластин CBN?
Твердые пластины CBN - это режущий инструмент с высокой твердостью и износостойкостью, изготовленный из частиц CBN (кубического нитрида бора) и металлического порошка, спеченного при высокой температуре и давлении.
Какова область применения твердых пластин CBN?
Твердые пластины из КНБ подходят для обработки материалов с высокой твердостью, высокой термостойкостью и высокой износостойкостью, таких как сталь, чугун, сплавы и т.д.
Каковы преимущества цельных пластин из КНБ по сравнению с пластинами из твердого сплава?
Пластины из твердого КНБ имеют более высокую твердость, лучшую термическую стабильность и более длительный срок службы, чем пластины из твердого сплава. Кроме того, пластины из твердого КНБ обеспечивают более высокую эффективность резания и качество поверхности.
Каков метод обслуживания твердых пластин CBN?
Обслуживание цельных пластин CBN требует внимания к чистоте и сухости поверхности инструмента, чтобы избежать столкновений и повреждений. Кроме того, инструмент необходимо регулярно осматривать и обслуживать, чтобы продлить срок его службы.
Сколько стоят цельные пластины из КНБ?
Твердые пластины из КНБ относительно дороги, как правило, в несколько раз дороже твердосплавных пластин или даже больше. Однако пластины из твердого КНБ имеют более длительный срок службы и позволяют сократить частоту и стоимость замены инструмента, одновременно повышая эффективность и качество обработки, снижая затраты и увеличивая производительность.
Какова структура цельной вставки CBN?
Твердые вставки из КНБ обычно состоят из частиц КНБ и металлической матрицы и выпускаются в конфигурациях с одной кромкой, несколькими кромками и вставками.
Как выбрать охлаждающую жидкость для твердых пластин CBN?
Смазочно-охлаждающая жидкость для пластин из твердого КНБ должна быть подобрана в соответствии с обрабатываемым материалом и условиями резания. Обычно это водорастворимая смазочно-охлаждающая жидкость или смазочно-охлаждающая жидкость на основе чистого масла.
Какова геометрия инструмента для цельных пластин CBN?
Твердые пластины из КНБ выпускаются прямоугольной, круглой, треугольной, алмазной и трапециевидной геометрии, которые можно выбрать в соответствии с конкретными требованиями к обработке.
Каковы силы резания и качество поверхности пластин из твердого КНБ?
Силы резания пластин из твердого КНБ обычно ниже, чем у пластин из твердого сплава, что снижает нагрузки и потери при обработке. Кроме того, качество поверхности пластин из твердого КНБ выше, что позволяет повысить эффективность обработки и качество продукции.