Carbide lathe form tool
A carbide lathe form tool is a type of form cutting tool used on a lathe machine that is specifically designed to shape or cut materials with a distinct profile or contour in a single operation. The “carbide” in its name refers to the material the tool is made from, usually tungsten carbide, which is a very hard and durable material capable of maintaining a sharp edge even at high temperatures and speeds, thereby increasing the tool’s lifespan and performance.
The cutting edge of a carbide lathe form tool is ground to match the specific shape or contour that needs to be produced on the workpiece. When the tool is applied against the rotating workpiece on a lathe, it carves out material, replicating its own profile onto the workpiece. This makes carbide lathe form tools ideal for precision machining tasks where complex shapes, grooves, or profiles need to be consistently reproduced, such as in the manufacturing of custom parts and components. Their carbide composition ensures they can handle a variety of materials, including hard metals that would wear down softer cutting tools quickly.
Common carbide lathe form tool machining methods
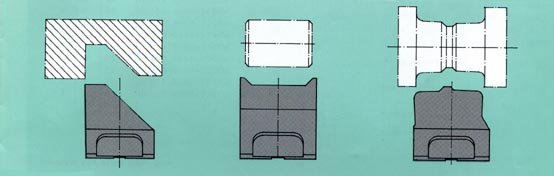
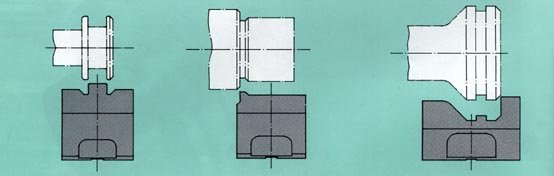
lathe form tool gallary
Часто задаваемые вопросы
How are form cutting tools different from standard cutting tools?
Form cutting tools and standard cutting tools differ primarily in their design and application purposes within machining processes. Here are the key distinctions:
- Design and Shape: Form cutting tools are crafted with a specific profile or shape on their cutting edges that is designed to be transferred directly onto the workpiece. This shape might be complex and is intended for creating precise contours or specific geometries in one operation. Standard cutting tools, on the other hand, typically have simpler designs, such as flat, pointed, or rounded cutting edges, and are used for more general purposes such as turning, milling, drilling, and cutting operations without imparting a specific shape to the material.
- Application and Versatility: Due to their specific design, form cutting tools are used for specialized tasks where a particular shape or profile needs to be machined into a workpiece. This makes them less versatile than standard cutting tools, which can be used across a wide variety of tasks and materials. Standard tools are the backbone of machining operations, used for basic cutting, shaping, and finishing tasks that do not require the replication of complex profiles.
- Material Removal Process: Form cutting tools often remove material in a manner that reflects their unique shape, creating specific forms in a single operation, which can increase efficiency for certain tasks. Standard cutting tools generally remove material in a more generic way, allowing for a broader range of operations but possibly requiring multiple passes or different tools to achieve a complex shape.
- Cost and Maintenance: The specialized nature of form cutting tools means they might be more expensive to design, manufacture, and maintain, particularly if a custom profile is required. Standard cutting tools, being more common and versatile, typically have lower initial costs and maintenance expenses, as well as a wider availability.
What are some common applications of form cutting tools in machining?
Form cutting tools are utilized across various machining applications where precise shapes, profiles, or details are essential. Here are some common applications:
- Gear Manufacturing: Gear teeth require very precise and uniform shapes to function correctly. Form cutting tools are used to cut the specific profiles of gear teeth, ensuring the proper engagement and functionality of the gear system.
- Thread Cutting: For both internal and external threading, form cutting tools with the thread profile ground into them are used to cut threads on screws, bolts, and in holes. These tools ensure that the threads are precise and conform to specific standards.
- Creating Custom Profiles: In industries where custom parts with unique profiles are necessary, such as aerospace, automotive, or tool and die making, form cutting tools are indispensable for machining these complex shapes accurately.
- Machining Keyways and Splines: Keyways and splines, which are used to match shafts and other components securely together, can be machined with form cutting tools designed for those specific shapes.
- Manufacturing Cutting Tools and Moulds: Form cutting tools are also used to manufacture other cutting tools, dies, and moulds with specific contours needed for various manufacturing processes.
- Decorative Grooving and Beveling: For adding aesthetic or functional grooves and bevels to parts, form cutting tools can be designed to create these features in a single operation.
- Dovetail Cutting: Cutting the precise angles and shapes of dovetails, which are used for strong, interlocking joints, is another application of form cutting tools.
Can form cutting tools be customized for specific geometric profiles in metalworking processes?
Yes, form cutting tools can absolutely be customized for specific geometric profiles in metalworking processes. This customization is one of their key advantages, allowing manufacturers to create complex and precise shapes in a single machining operation. Custom form cutting tools are designed and manufactured based on the specific requirements of the workpiece to be machined, ensuring that the tool’s cutting edge closely matches the desired contour or profile.
Customizing form cutting tools involves careful consideration of the material to be machined, the complexity of the profile, the volume of production, and the precision required. The process typically starts with a detailed drawing or CAD model of the desired profile. Tool manufacturers use this information to design the tool, selecting appropriate materials—such as high-speed steel or tungsten carbide—for the tool bit to ensure durability and performance.
Advanced techniques, such as computer-aided manufacturing (CAM) and CNC machining, play a crucial role in the manufacturing of these custom tools, allowing for high precision and adherence to the specified geometries. The custom tool is then ground and finished to match the provided specifications exactly.
Custom form cutting tools are widely used in specialized applications across various industries such as aerospace, automotive, mold making, and custom machinery manufacturing. The ability to create tools for specific profiles enables manufacturers to produce unique and complex parts efficiently, reducing the need for multiple machining operations and ensuring high levels of accuracy and consistency.
How are custom form cutting tools designed based on specific geometric profiles?
Designing custom form cutting tools based on specific geometric profiles involves a meticulous process that requires precision and expertise. The journey from conceptual design to the final tool involves several key steps:
- Understanding the Requirement: It starts with a comprehensive understanding of the specific geometric profile needed for the part to be machined. This usually involves detailed drawings, CAD models, or even physical examples of the desired outcome. Factors such as the material of the workpiece, the complexity of the profile, the required finish, and tolerances are crucial considerations.
- Material Selection for the Tool: Based on the requirements, an appropriate material for the cutting tool is selected. The material choice, such as high-speed steel (HSS), carbide, cobalt, or others, depends on the hardness of the workpiece material, the required lifespan of the tool, machining conditions, and cost constraints.
- Designing the Tool Profile: Using CAD (Computer-Aided Design) software, the specific geometric profile of the cutting edge is designed. This step involves translating the desired dimensions and shapes of the final product into the cutting surfaces of the tool. Advanced software allows for precise control over the tool geometry, ensuring that it can produce the required profile on the workpiece.
- Simulation and Optimization: Many modern CAD programs include simulation capabilities, allowing designers to visualize how the tool will interact with the workpiece material. Simulations can identify potential issues with the tool design, such as areas prone to wear or breakage, and help optimize cutting angles, speeds, and feeds for efficient material removal.
- Manufacturing the Tool: Once the design is finalized, CAM (Computer-Aided Manufacturing) software generates the necessary CNC (Computer Numerical Control) machining instructions to produce the tool. The manufacturing process may involve precision grinding, milling, and polishing to achieve the detailed geometries and sharp edges required for effective cutting.
- Coating (Optional): Some tools are then coated with materials like Titanium Nitride (TiN), Titanium Carbonitride (TiCN), or Diamond-like Carbon (DLC) to enhance their hardness, reduce wear, and increase lifespan. This step is especially common for tools that will be used on very hard materials.
- Testing and Quality Control: The final step involves testing the custom form cutting tool under actual or simulated working conditions to ensure it meets all specifications and requirements. Adjustments might be made based on this testing to further refine the tool’s performance.
The design process is iterative, involving close collaboration between tool designers, manufacturing engineers, and end-users to ensure that the custom form cutting tool precisely meets the specific geometric profile and performance requirements of the intended application.