Lathe form tools are integral components in the metalworking industry, primarily due to their ability to shape materials accurately and efficiently. These tools are specially designed to create complex geometric profiles and precise cuts, enhancing the productivity and quality of machining processes.
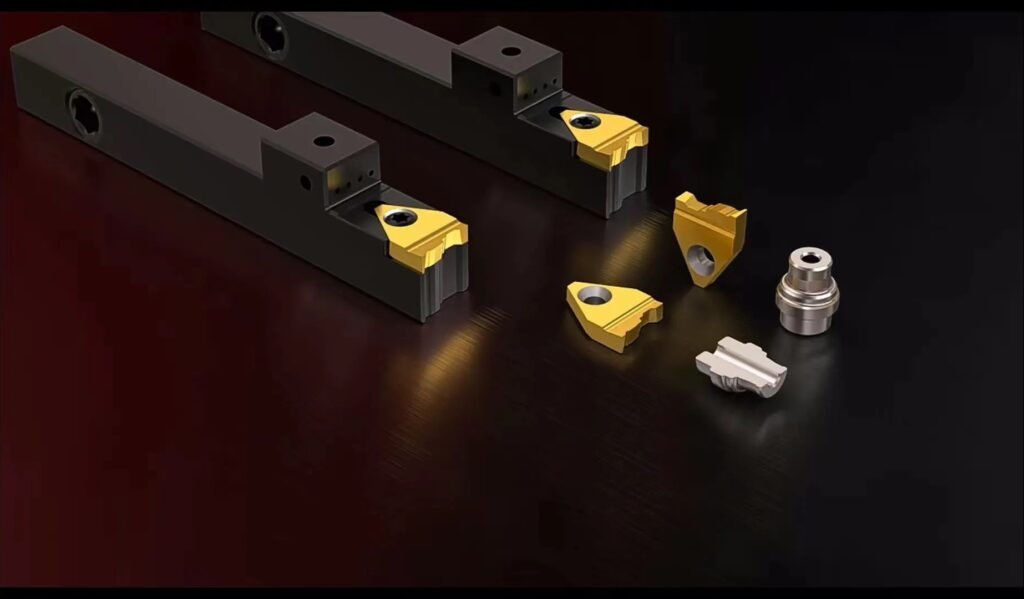
- Precision and Consistency: Lathe form tools allow for the production of highly precise and consistent shapes, which is crucial for meeting stringent industry standards and ensuring the reliability of finished products.
- Efficiency Enhancement: By reducing the need for multiple tool changes and minimizing machining time, these tools significantly boost operational efficiency. They streamline processes and enable faster production cycles.
- Versatility: These tools can be customized to handle a wide range of materials, from softer metals to harder alloys. This adaptability makes them suitable for various applications across different sectors.
Role in the Metalworking Industry:
- Automotive Manufacturing: Lathe form tools are used to produce components like engine parts, shafts, and gears with high precision, ensuring the functionality and durability of vehicles.
- 항공 우주 공학: The industry demands parts with exact specifications for safety and performance. Form tools help in crafting components like turbine blades and structural fittings with the required accuracy.
- 일반 제조업: From producing intricate parts for machinery to crafting custom components for consumer products, these tools play a vital role in a wide array of manufacturing processes.
Definition and Types of Lathe Form Tools

Lathe form tools are specialized cutting tools used on lathes for shaping and cutting materials, particularly metals, into specific geometric profiles. Unlike standard cutting tools, which typically produce round or cylindrical shapes, form tools are designed to create more complex contours in a single pass. This unique capability makes them indispensable in precision machining processes where consistency and efficiency are key.
Definition:
A lathe form tool is defined as a single-point cutting tool that comes into contact with the workpiece and removes material to form a specific shape or profile. The design of the cutting edge of the tool corresponds directly to the cross-section of the desired final product.
Types of Lathe Form Tools:
- High-Speed Steel (HSS) Form Tools:
Made from high-speed steel, these tools can withstand high temperatures, allowing for faster cutting speeds. They are widely used for their toughness and resistance to wear and tear.
- Carbide Form Tools:
Composed of tungsten carbide, these tools offer exceptional hardness and can maintain a sharp cutting edge at high temperatures, making them suitable for
- Diamond Form Tools:
These tools use a diamond, the hardest known material, as the cutting edge. They are used for ultra-precision machining tasks, particularly for non-ferrous and highly abrasive materials.
- Cobalt Form Tools:
Cobalt form tools combine the toughness of high-speed steel with the heat resistance of carbide tools. They are ideal for machining work that requires both durability and the ability to handle high temperatures.
- Ceramic Form Tools:
Made from ceramic materials, these tools are extremely hard and resistant to wear. They are preferred for high-speed machining of hard materials, though they are more brittle than other types.
Design Principles of Form Tools
The design principles of form tools are integral to their effectiveness in precision machining. These principles ensure that tools efficiently create desired shapes while maintaining durability and reducing wear. The following are key considerations in the design of form tools:
Material Compatibility: The tool material should be suitable for cutting the workpiece material. For instance, harder materials like carbides are preferred for machining tough metals, while high-speed steel (HSS) might be adequate for softer materials.
Cutting Edge Geometry: The shape of the cutting edge directly influences the form of the cut. It must be precisely designed to match the desired profile on the workpiece. This includes considerations for rake angles, clearance angles, and leading/trailing edges to optimize cutting efficiency and tool life.
Tool Strength and Rigidity: Tools must be designed to withstand the forces they encounter during machining without deforming. This requires careful consideration of tool cross-sectional areas, support angles, and overall geometry to balance strength with the need for precise cutting edges.
Heat Dissipation: Effective heat management is essential to preserve tool life and maintain cutting accuracy. This involves designing tools and selecting materials that can withstand or dissipate heat effectively. It also includes considering the use of coolants and the geometry of the tool to allow for adequate heat escape.
Wear Resistance: Tools are designed with materials and coatings that resist wear from friction and abrasion. This might involve using carbide, diamond, or applying coatings like titanium nitride (TiN) to prolong tool life.
Ergonomics and Safety: Form tool designs consider ease of use and safety, ensuring that tools can be securely mounted, easily adjusted, and safely operated.
Economic Efficiency: The tool design must also consider manufacturing cost and maintenance. Designs that offer replaceable cutting edges or regrindable profiles can offer significant savings over tools that must be discarded when dull.
Surface Finish Requirements: The desired quality of the workpiece surface influences tool design, particularly in terms of cutting edge smoothness and the precision of the tool form.
Advantages of Using Form Tools
Using form tools in machining operations comes with a range of advantages that make them an essential aspect of the manufacturing process, especially when precision and efficiency are paramount. Here are some of the key benefits:
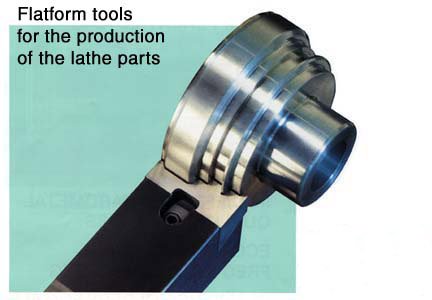
Precision and Accuracy: Form tools are designed to create specific shapes in a single pass. This ensures high precision and accuracy in the produced parts, as the shape of the tool directly correlates with the profile of the workpiece.
Increased Production Speed: Since form tools can shape a workpiece in a single pass, they significantly reduce the machining time compared to using multiple tools or passes. This efficiency is crucial for high-volume production runs where time savings directly translate to increased throughput.
Consistency and Reproducibility: The ability to produce uniform shapes with each pass makes form tools ideal for operations requiring high consistency and repeatability. This is particularly important in industries where parts must adhere to strict specifications and quality standards.
Reduced Tool Changes: By accomplishing the desired shape in one pass, form tools minimize the need for tool changes. This not only speeds up the production process but also reduces wear and tear on the machinery and decreases downtime for tool replacement.
Versatility: Form tools can be custom-made to produce a wide variety of shapes and profiles. This versatility allows them to be adapted to different machining operations and materials, making them invaluable in custom or specialized manufacturing tasks.
향상된 표면 마감: The single-pass cutting action of form tools often results in a superior surface finish, reducing or even eliminating the need for subsequent finishing processes. This can lead to further savings in time and cost.
Ease of Use: Despite their specialized nature, form tools are designed for straightforward operation. Once set up, they can produce the desired shapes without requiring constant adjustments, making them user-friendly and reducing the likelihood of operator error.
Cost-Effectiveness: Although the initial investment in custom form tools can be higher than standard tools, the increased efficiency, reduced downtime, and lower labor costs often result in long-term cost savings. This makes them a cost-effective choice for many machining operations.
Application of Lathe Form Tools
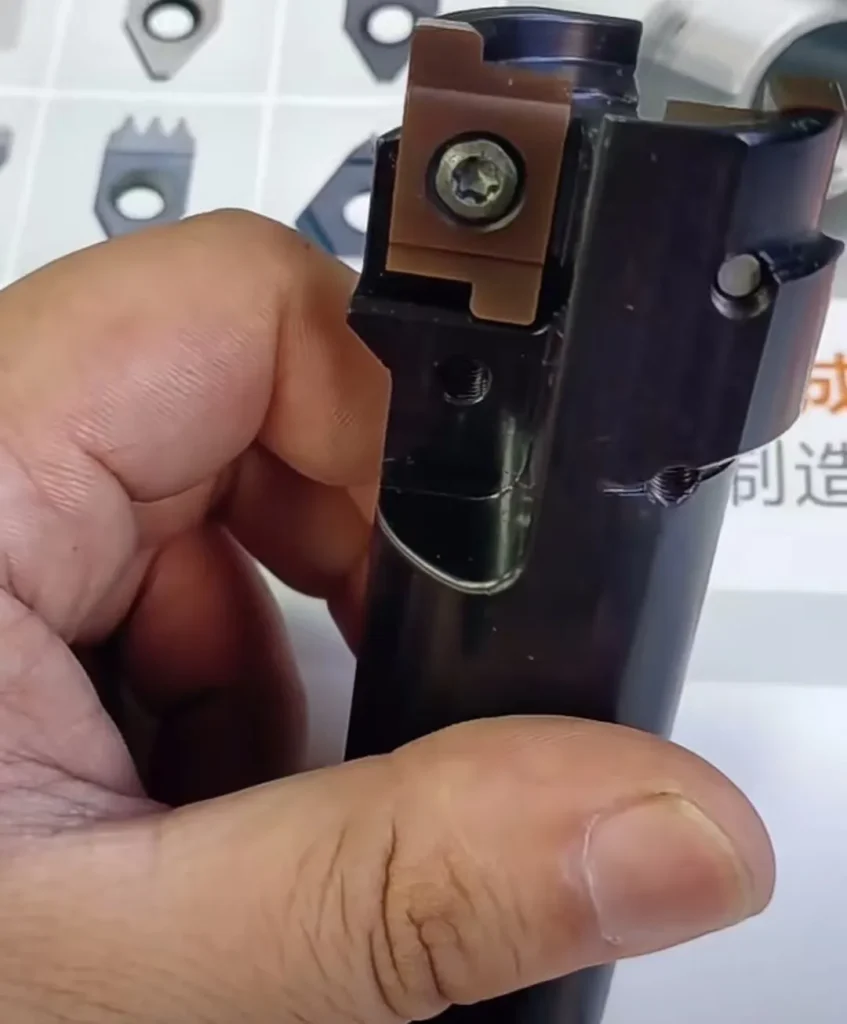
Form tools are vital in various manufacturing and machining operations due to their unique ability to create complex shapes and profiles with precision. Their applications span a wide range of industries, making them indispensable tools for both general and specialized machining tasks. Here are some of the key applications of form tools:
Automotive Industry:
Form tools are used to create precision parts such as engine components, transmission gears, and shafts. Their ability to produce complex shapes with high accuracy is crucial for the performance and reliability of automotive parts.
Aerospace Industry:
In aerospace machining, form tools are employed to manufacture components with tight tolerances, such as turbine blades, structural components, and landing gear parts. The precision and consistency of form tools ensure that these critical parts meet stringent aerospace standards.
Medical Device Manufacturing:
The medical industry relies on form tools for creating precision instruments and implants, such as orthopedic implants, surgical tools, and device enclosures. The high level of accuracy and finish achieved with form tools is essential for the functionality and safety of medical devices.
Tool and Die Making:
Form tools are extensively used in the tool and die industry to produce molds, dies, and fixtures. They facilitate the machining of intricate geometries and patterns required in the production of other tools and components.
Jewelry and Watchmaking:
The ability to produce delicate, intricate designs makes form tools ideal for the jewelry and watchmaking sectors. They are used to craft everything from watch components to intricate jewelry items with precision.
Electronics Industry:
Form tools play a crucial role in manufacturing electronic components and assemblies, such as connectors, heat sinks, and enclosures. They enable the high precision and miniaturization required in modern electronics.
General Machinery:
In the production of machinery and equipment across various industries, form tools are used to machine key components that require specific shapes and profiles, such as gears, bearings, and levers.
Woodworking and Plastics:
While mainly associated with metalworking, form tools are also used in woodworking and plastics machining to produce molds, patterns, and complex shapes in non-metal materials.
Custom Manufacturing:
For custom manufacturing operations that require unique and specialized parts, form tools are designed and utilized to meet specific machining needs that standard tools cannot achieve.
결론
Form tools significantly enhance traditional turning processes by introducing efficiency, precision, and versatility to what was once a more time-consuming operation. Their primary significance lies in their ability to produce complex shapes and profiles in a single pass, which drastically improves the production speed and accuracy of turned parts. This single-pass capability reduces the need for multiple tools or setups, streamlining the machining process and minimizing the potential for errors, leading to consistent and high-quality outcomes.