

SNGX insert
Are you in search of a reliable, high-performance solution for your precision milling needs? Introducing SNGX inserts, the cutting-edge tools designed to deliver exceptional accuracy and durability. Perfect for a variety of milling tasks, our inserts ensure you achieve superior results every time.
Why SNGX Inserts Are the Best Choice for Your Business
Exceptional Precision and Accuracy
SNGX inserts are engineered to provide outstanding precision and accuracy in milling operations. Their unique geometry and high-quality construction ensure consistent performance, making them ideal for tasks that demand meticulous detail.
Robust and Durable Design
Designed to withstand high cutting forces and temperatures, inserts are made from premium materials and feature advanced coatings. This durability allows them to perform efficiently in challenging conditions, extending tool life and reducing downtime.
Versatility Across Applications
SNGX inserts excel in a wide range of milling applications:
- Precision Milling: Achieve fine details and exact specifications.
- Finishing Operations: Ensure a smooth surface finish and high-quality results.
- Medium-Duty Milling: Perfect for a variety of materials including steel, stainless steel, and non-ferrous metals.
- Complex Contours: Handle intricate shapes and profiles with ease.
Advanced Coatings and Materials
Available in various grades and coatings, such as PVD and CVD, our SNGX inserts are designed to enhance wear resistance, reduce friction, and improve overall cutting performance. This makes them suitable for both roughing and finishing operations.
Applications
Inserts excel in various industrial milling operations:
- General face milling
- Shoulder milling
- Roughing and finishing operations
- Suitable for materials including steel, stainless steel, and cast iron
Benifit Our Inserts?
Transform Your Milling Efficiency
Imagine the productivity boost and cost savings your business will experience with inserts. Our high-performance inserts not only improve your milling operations but also extend tool life, minimizing downtime and maximizing profitability.
Proven Success
Join the ranks of satisfied customers who have elevated their milling processes with inserts. Trusted by industry leaders for their precision and reliability, our inserts deliver consistent, high-quality results.
Tailored Solutions
We understand the unique needs of your business. We offer custom solutions tailored to your specific milling requirements. Our team of experts is ready to assist you in selecting the right inserts and providing ongoing support to ensure your success.
Frequently Asked Questions
What are SNGX inserts?
Inserts are indexable cutting tools used in milling operations. They feature a square shape with a robust design, offering multiple cutting edges for enhanced performance and durability in precision milling tasks.
How many cutting edges do SNGX inserts have?
Inserts typically have four cutting edges. This design allows for multiple uses of the insert by rotating it to access different edges, maximizing tool life and reducing costs.
How do SNGX inserts improve milling performance?
Inserts enhance milling performance by:Providing precise and accurate cuts Offering durability to withstand high cutting forces Ensuring a smooth surface finish and consistent results Handling interrupted cuts and complex geometries effectively
What applications are SNGX inserts suitable for?
Precision milling and finishing operations Medium-duty milling across various materials Machining complex contours and profiles Handling interrupted cuts and high-speed milling Working with hard materials like hardened steel and high-strength alloys
What types of coatings are available for SNGX inserts?
PVD (Physical Vapor Deposition): Provides wear resistance and reduces friction. CVD (Chemical Vapor Deposition): Offers toughness and extended tool life.
How do I choose the right SNGX insert for my application?
The material to be machined The type of milling operation (e.g., precision or roughing) Desired surface finish and accuracy Cutting conditions (speed, feed, and depth of cut) Compatibility with your machine and tooling setup Consulting with a tooling expert can help ensure the best selection for your needs.
Our Production Capability

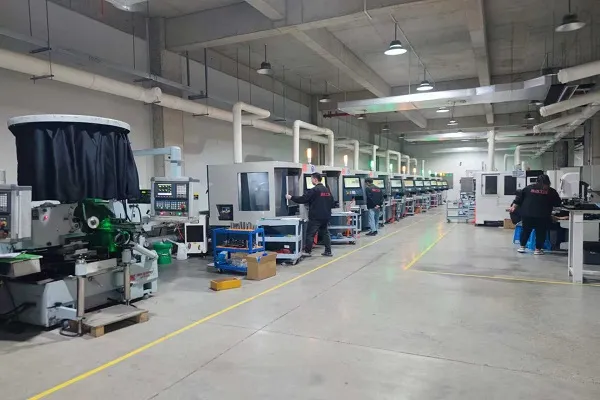



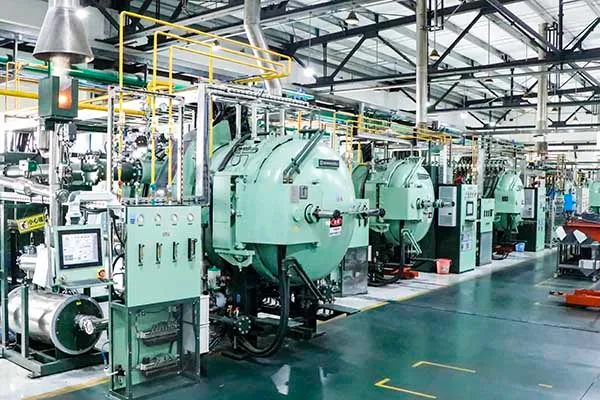

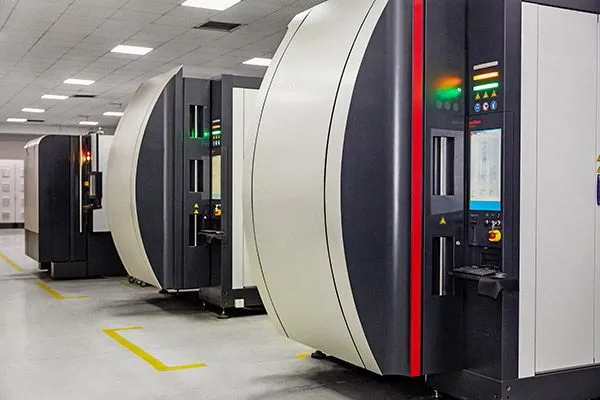

