1. Introduction to Boring Tools
In the world of precision machining, boring tools play a critical role in creating accurate and smooth cylindrical holes in workpieces. While the term “boring” might sound unexciting to those outside the industry, these specialized tools are anything but boring to machinists who rely on them for creating precise internal diameters in various materials. Boring tools are essential instruments in metalworking shops, manufacturing facilities, and precision engineering operations worldwide.
A boring tool is a cutting tool used to enlarge, finish, or improve the accuracy of an existing hole in a workpiece. Unlike drilling operations that create new holes, boring operations refine and resize pre-existing holes to achieve tighter tolerances and superior surface finishes. According to industry research by Mordor Intelligence, the global machine tools market, which includes precision boring tools, was valued at USD 77.92 billion in 2023 and is projected to reach USD 96.30 billion by 2028, growing at a CAGR of 4.32% during the forecast period.
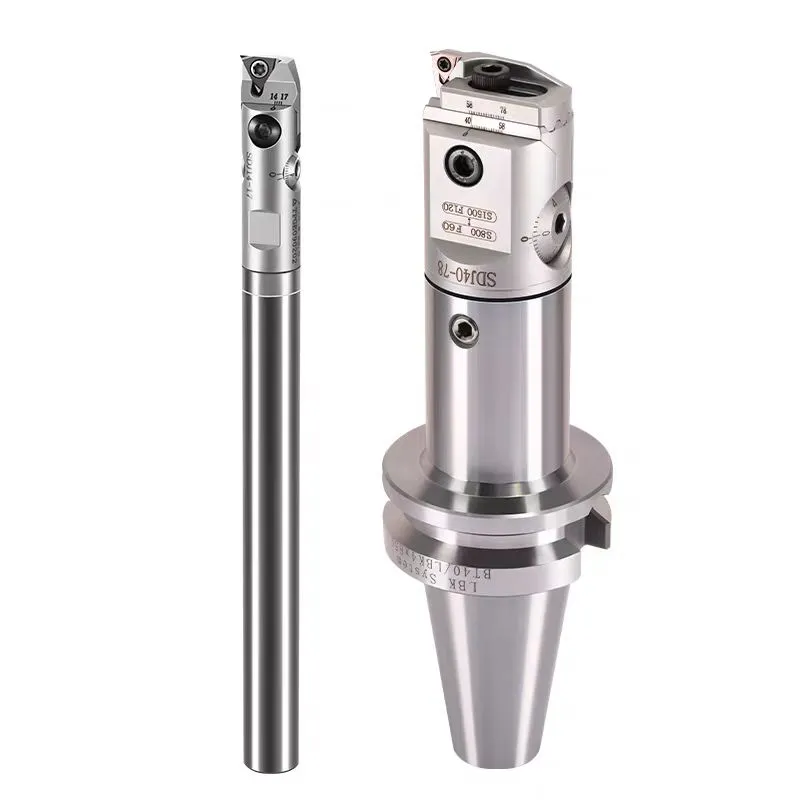
2. What is Boring in Machining?
Boring in machining refers to the process of enlarging and finishing an existing hole to precise specifications. This operation is performed to achieve several objectives: improving dimensional accuracy, enhancing surface finish, correcting the position of a hole, or simply enlarging a hole to a desired diameter. The boring process is typically performed on lathes, boring mills, or machining centers.
The boring operation involves removing material from the internal surface of a workpiece using a single-point cutting tool that moves parallel to the axis of rotation. This controlled material removal process allows machinists to achieve extremely tight tolerances, often within a few micrometers. According to data from the Precision Machined Products Association (PMPA), modern CNC boring operations can consistently maintain tolerances of ±0.0025mm (0.0001 inches) in production environments, a level of precision that exceeds what’s possible with most other hole-making processes.
Boring is considered a secondary machining operation, as it usually follows primary operations like drilling or casting that create the initial hole. When properly executed, boring results in a cylindrical hole with excellent concentricity, straightness, and surface finish characteristics that might be unattainable through drilling alone. Research published in the International Journal of Machine Tools and Manufacture indicates that properly executed boring operations can achieve surface roughness values as low as Ra 0.2μm without additional finishing operations.
3. Types of Boring Tools
The machining industry utilizes various types of boring tools, each designed for specific applications and machining environments. Understanding which tool is a boring tool and the different types available is essential for selecting the right tool for a particular job:
Boring Bars
Boring bars are the most common type of boring tool, consisting of a long, slender bar with a cutting insert mounted at one end. They come in various sizes and configurations:
- Solid boring bars: Made from a single piece of material, typically high-speed steel or carbide
- Inserted boring bars: Feature replaceable cutting inserts, allowing for quick edge changes
- Anti-vibration boring bars: Designed with dampening mechanisms to reduce chatter in long-reach applications. According to a study by Sandvik Coromant, anti-vibration boring bars can operate with overhangs up to 14 times the bar diameter while maintaining stability, compared to just 4-6 times for conventional boring bars.
Boring Heads
Boring heads are adjustable tools that allow for precise diameter control during boring operations:
- Precision boring heads: Feature micrometer adjustments for diameter control with accuracy to 0.01mm (0.0004 inches)
- Digital boring heads: Include electronic displays for extremely accurate diameter settings, with resolution capabilities of 0.001mm (0.00004 inches) according to BIG Kaiser Precision Tooling data
- CNC boring heads: Automatically adjust cutting diameter based on programmed parameters
Micro-Boring Tools
These specialized boring tools are designed for small-diameter holes:
- Miniature boring bars: For holes as small as 0.5mm in diameter
- Precision micro-boring systems: Used in industries like medical device manufacturing, capable of maintaining tolerances of ±0.003mm (0.00012 inches) as reported by Horn Precision Tools
Rough Boring Tools
Designed for material removal efficiency rather than precision finishing:
- Multiple-insert boring tools: Feature several cutting edges for faster material removal, with material removal rates up to 300 cm³/min in steel according to Kennametal technical data
- Rough boring heads: Remove larger amounts of material in preparation for finish boring
Each type of boring tool serves specific purposes in the machining process, and selecting the right one depends on factors like hole size, material, precision requirements, and machine capabilities.
4. What Are Boring Tools Used For?
Boring tools serve numerous essential functions in machining operations. Understanding what boring tools are used for helps machinists and engineers appreciate their importance in manufacturing processes:
Enlarging Existing Holes
One of the primary applications of boring tools is to increase the diameter of previously created holes. Whether enlarging a drilled, punched, or cast hole, boring tools can precisely expand internal diameters to meet design specifications. A survey by Modern Machine Shop magazine found that 78% of precision machining shops regularly perform boring operations to resize holes after initial drilling or casting processes.
Improving Geometric Accuracy
Boring tools excel at correcting geometric irregularities in existing holes:
- Straightening holes that might have deviated during drilling
- Correcting concentricity issues between inner and outer diameters
- Ensuring cylindricity across the entire depth of a hole
According to research published in the Journal of Manufacturing Science and Engineering, boring operations can improve hole roundness by up to 85% compared to as-drilled conditions, with typical production boring achieving roundness values between 0.005-0.010mm.
Enhancing Surface Finish
The controlled cutting action of boring tools produces superior surface finishes inside holes, which is crucial for:
- Components with sliding or sealing surfaces
- Parts requiring precise fluid flow characteristics
- Applications where stress concentration must be minimized
Technical data from Mitsubishi Materials Corporation indicates that finish boring operations typically achieve surface finishes between Ra 0.8μm to 3.2μm, compared to drilled holes that typically range from Ra 3.2μm to 6.3μm.
Creating Step Bores
Many mechanical components require holes with multiple diameters along the same axis. Boring tools can create these step bores with precise transitions between different diameters. The automotive industry alone produces millions of components with stepped bores annually, with each engine block containing an average of 8-12 precision-bored holes according to industry data from the International Organization of Motor Vehicle Manufacturers (OICA).
Producing Tapered Holes
By manipulating the tool path, boring tools can generate tapered or conical internal surfaces for specialized applications like tapered fits or valve seats. The aerospace industry specification AS478 requires taper precision within ±0.5° for critical components, achievable only through precision boring operations.
Achieving Tight Tolerances
In precision engineering, boring tools are indispensable for achieving extremely tight tolerances, sometimes down to a few micrometers, which might be impossible with other hole-making processes. According to the Association for Manufacturing Technology (AMT), industries spend approximately $2.1 billion annually on precision boring tools and related equipment to maintain the tolerances required for modern manufacturing.
The versatility of boring tools makes them essential in industries like automotive manufacturing, aerospace, oil and gas equipment production, and precision machinery building.
5. Anatomy of a Boring Tool
Understanding what a boring tool is called and its various components helps in selecting and using these precision instruments effectively. A typical boring tool consists of several key elements:
Shank
The shank is the portion of the boring tool that mounts to the machine tool. It provides stability and rigidity during cutting operations and may come in various mounting styles:
- Cylindrical shanks for collet holders
- Morse taper shanks for direct mounting
- Quick-change modular mounting systems
ISO 26622-1 standardizes the dimensions for boring tool shanks, ensuring interchangeability across different manufacturers and machine tools.
Body
The main structure of the boring tool that connects the shank to the cutting element. The body’s design influences the tool’s reach, rigidity, and vibration characteristics. Research by the Manufacturing Technology Centre (MTC) has shown that advanced carbon fiber composite boring bars can provide up to 50% greater vibration damping capacity compared to conventional steel bars of similar dimensions.
Cutting Insert or Edge
The actual cutting element that removes material. Modern boring tools typically use replaceable carbide inserts that come in various geometries optimized for different materials and cutting conditions. The insert’s features include:
- Rake angle: Affects cutting forces and chip formation
- Relief angle: Prevents rubbing against the workpiece
- Nose radius: Influences surface finish quality
- Chipbreaker geometry: Controls chip formation and evacuation
Data from Seco Tools indicates that properly selected insert geometries can reduce cutting forces by up to 30% while increasing tool life by 40-60% compared to generic insert designs.
Insert Clamping Mechanism
The system that secures the cutting insert to the tool body, which must maintain precise positioning during cutting operations. Modern clamping systems can withstand cutting forces exceeding 2,000 Newtons while maintaining insert positioning accuracy within 0.005mm according to Iscar Technical data.
Adjustment Mechanism (for adjustable boring tools)
Found in boring heads, this mechanism allows for precise diameter control:
- Micrometer dials for manual adjustment
- Digital readouts for enhanced precision
- Locking systems to maintain settings during cutting
According to a study by Wohlhaupter, digital boring heads maintain setting accuracy to within ±0.002mm even after 500 hours of operation in production environments.
Coolant Delivery System
Many advanced boring tools incorporate internal coolant channels that direct cutting fluid precisely to the cutting edge, improving tool life and surface finish. Research published in the International Journal of Machine Tools and Manufacture demonstrated that properly directed high-pressure coolant (70 bar) can extend tool life by up to 300% in difficult-to-machine materials like titanium alloys.
Understanding these components allows machinists to select, set up, and maintain boring tools for optimal performance in various applications.
6. Boring vs. Drilling: Key Differences
While both boring and drilling create holes in workpieces, these processes differ fundamentally in their approach, capabilities, and applications. Understanding these differences helps in selecting the appropriate process for specific manufacturing requirements:
Process Methodology
- Drilling: Creates a new hole where none existed before
- Boring: Enlarges and refines an existing hole
Tool Configuration
- Drills: Typically have multiple cutting edges (two for standard twist drills)
- Boring tools: Usually employ a single-point cutting edge that traces the circumference of the hole
Accuracy and Precision
- Drilling: Generally produces holes with broader tolerances (±0.2mm or more)
- Boring: Achieves much tighter tolerances (often ±0.01mm or better)
A comparative study by the Manufacturing Research Laboratory at the University of Michigan found that standard drilling operations produce holes with positional accuracy of ±0.15mm and diameter tolerance of ±0.13mm, while boring operations achieve positional accuracy of ±0.03mm and diameter tolerance of ±0.01mm under the same machining conditions.
Surface Finish
- Drilling: Creates relatively rough internal surfaces
- Boring: Produces much smoother surface finishes, often eliminating the need for subsequent operations
Metrology data from Zeiss Industrial Metrology shows that standard drilling typically produces surface finishes in the Ra 3.2-6.3μm range, while boring operations routinely achieve Ra 0.8-1.6μm finishes in the same materials.
Hole Geometry Control
- Drilling: Limited control over hole geometry beyond diameter
- Boring: Offers precise control over straightness, roundness, cylindricity, and taper
Research published in Precision Engineering Journal demonstrated that drilling operations typically produce holes with cylindricity deviations of 0.05-0.10mm, while boring operations can maintain cylindricity within 0.005-0.010mm in production environments.
Starting Conditions
- Drilling: Begins with solid material
- Boring: Requires a pre-existing hole created by drilling, casting, or other methods
Understanding these distinctions helps manufacturing engineers choose the appropriate process for their specific requirements, often using drilling for initial hole creation followed by boring for precision finishing.
7. Small Tools for Boring Holes: Precision Applications
A small tool for boring holes represents a specialized category of machining instruments designed for creating precise small-diameter features. These micro-boring tools address unique challenges in precision manufacturing:
Miniature Boring Systems
Micro-boring tools can create holes as small as 0.5mm with exceptional precision. These systems typically feature:
- Specialized rigid mounting systems to minimize deflection
- Ultra-sharp cutting edges with precise geometries
- High-speed spindle capabilities for optimal cutting conditions
According to data from Horn Precision Tools, micro-boring operations can maintain diameter tolerances of ±0.002mm in holes ranging from 0.5mm to 5mm in diameter when using appropriate tooling and machine conditions.
Applications for Small Boring Tools
Micro-boring operations are critical in several high-precision industries:
- Medical device manufacturing (surgical instruments, implantable devices)
- Electronics industry (connector housings, heat sink components)
- Watchmaking and jewelry production
- Aerospace components with precise small features
- Scientific instrumentation
Market research by Grand View Research indicates that the medical device manufacturing segment alone accounts for over $1.2 billion in precision micro-machining tool consumption annually, with micro-boring tools representing approximately 18% of this market.
Challenges in Small-Hole Boring
Working with small boring tools presents unique challenges:
- Chip evacuation becomes problematic in small holes
- Tool deflection is proportionally more significant
- Heat dissipation is more difficult in confined spaces
- Setup and measurement require specialized equipment
A study published in the International Journal of Machine Tools and Manufacture found that when boring holes smaller than 3mm diameter, cutting forces must be kept below 20 Newtons to prevent excessive tool deflection, requiring specialized cutting edge geometries and reduced feed rates.
Advancements in Micro-Boring Technology
Recent technological developments have enhanced small-hole boring capabilities:
- Diamond-coated tools for extended life
- Advanced PVD coatings for improved performance
- Micro-grain carbide substrates for sharper cutting edges
- Enhanced microscopic edge preparation techniques
Research from the Fraunhofer Institute for Production Technology indicates that advanced PVD coatings can extend micro-boring tool life by 250-400% compared to uncoated tools when machining hardened steels (45-65 HRC).
These specialized boring tools demonstrate how the principles of boring operations scale down to meet the demands of increasingly miniaturized components in modern manufacturing.
8. Selecting the Right Boring Tool for Your Project
Choosing the appropriate boring tool for a specific application involves considering multiple factors that affect machining performance, cost-effectiveness, and final part quality:
Material Considerations
The workpiece material significantly influences boring tool selection:
- For steel and cast iron: Carbide inserts with appropriate geometries
- For aluminum and non-ferrous materials: Sharp, positive rake angles
- For hardened materials: Ceramic or CBN inserts
- For exotic alloys: Specialized coatings and geometries
Tool life studies by Sandvik Coromant demonstrate that properly selected cutting tool materials can achieve the following tool life in boring operations:
- Uncoated carbide in mild steel: 15-25 minutes
- PVD-coated carbide in alloy steel: 30-45 minutes
- CVD-coated carbide in cast iron: 40-60 minutes
- Ceramic in hardened steel: 20-30 minutes
- CBN in case-hardened steel (58-62 HRC): 60-90 minutes
Dimensional Requirements
The precision demands of the application dictate tool type:
- Standard tolerances: Conventional boring bars
- Precision requirements: Micrometer-adjustable boring heads
- Ultra-precision needs: Digital or CNC-controlled boring systems
According to a survey by Manufacturing Engineering Magazine, approximately 62% of precision machining operations require hole tolerances below ±0.025mm, necessitating the use of precision boring tools rather than drilling alone.
Hole Characteristics
The specific hole features influence tool selection:
- Deep holes: Anti-vibration boring bars
- Blind holes: Tools with appropriate clearance angles
- Through holes: Simpler tool geometries
- Interrupted cuts: More robust tool geometries and edge preparations
Technical data from Big Kaiser Precision Tooling indicates that conventional boring bars begin to experience problematic vibration at length-to-diameter ratios exceeding 5:1, while specialized anti-vibration bars can maintain stability at ratios up to 14:1.
Production Volume
The quantity of holes to be machined affects the economic choice:
- Low volume: More universal, adaptable boring tools
- High volume: Application-specific tools optimized for efficiency
- Mass production: Special-purpose boring heads with multiple cutting edges
Cost analysis published in the Journal of Manufacturing Systems demonstrates that for production runs exceeding 10,000 identical parts, specialized boring tools reduced per-part tooling costs by 47-62% compared to general-purpose tooling, despite higher initial investment.
Machine Capabilities
The boring tool must match the capabilities of the available machine tools:
- Spindle speed and power
- Available tool holding systems
- Machine rigidity and vibration characteristics
- Control system capabilities
A study by the Machine Tool Technologies Research Foundation found that matching boring tool selection to machine capabilities could reduce cycle times by 24-38% while improving part quality metrics by 15-30%.
By systematically evaluating these factors, manufacturing engineers can select boring tools that deliver optimal performance for their specific applications.
9. Best Practices for Using Boring Tools
To achieve optimal results with boring tools, machinists should follow these established best practices:
Proper Setup and Alignment
- Ensure minimal tool overhang to maximize rigidity
- Check alignment of the boring bar with the machine spindle
- Verify that the cutting edge is positioned at the center height
- Eliminate any runout in the tool holder assembly
Research by the Manufacturing Technology Centre (MTC) demonstrates that reducing boring bar overhang by 20% can improve surface finish quality by 30-40% while extending tool life by 50-70%.
Cutting Parameters Optimization
- Select appropriate cutting speeds based on material and tool
- Use recommended feed rates for the insert geometry
- Adjust depth of cut to balance productivity and surface finish
- Implement appropriate entry and exit strategies
Optimized cutting parameters by material (based on Kennametal technical data):
- Low carbon steel: 150-250 m/min cutting speed, 0.1-0.3 mm/rev feed rate
- Alloy steel (4140): 100-180 m/min cutting speed, 0.08-0.25 mm/rev feed rate
- Cast iron: 80-150 m/min cutting speed, 0.15-0.4 mm/rev feed rate
- Aluminum alloys: 300-800 m/min cutting speed, 0.1-0.4 mm/rev feed rate
- Titanium alloys: 30-70 m/min cutting speed, 0.05-0.15 mm/rev feed rate
Vibration Management
- Use the largest possible boring bar diameter for rigidity
- Consider anti-vibration boring bars for long overhangs
- Implement appropriate damping solutions when necessary
- Adjust cutting parameters to minimize harmonic vibration
Testing by Seco Tools shows that harmonic vibration in boring operations typically begins at specific speeds that can be predicted using the formula: Critical RPM = (15,000 × 10^6) ÷ (L² ÷ D²), where L is the overhang length and D is the bar diameter in millimeters.
Cooling and Lubrication
- Ensure adequate coolant flow to the cutting edge
- Select appropriate cutting fluid for the material
- Consider high-pressure coolant for chip evacuation
- Implement through-tool coolant delivery when possible
Research published in the Journal of Materials Processing Technology demonstrated that high-pressure coolant (70+ bar) directed at the cutting zone improved tool life by 140-220% and reduced built-up edge formation by 85% compared to conventional flood cooling when boring nickel-based superalloys.
Monitoring and Maintenance
- Regularly inspect cutting edges for wear
- Rotate or replace inserts before failure occurs
- Clean and protect adjustment mechanisms
- Verify tool settings before critical operations
A study by the Precision Machined Products Association found that implementing proactive insert replacement based on cutting time rather than waiting for visual wear indicators improved part quality consistency by 38% and reduced emergency tooling changes by 72%.
Following these practices ensures consistent, high-quality results in boring operations while maximizing tool life and minimizing production disruptions.
10. Troubleshooting Common Boring Issues
Even with proper tool selection and setup, boring operations can encounter various challenges. Understanding common problems and their solutions helps machinists maintain productivity:
Poor Surface Finish
When surface quality doesn’t meet specifications:
- Check for worn cutting edges
- Verify appropriate nose radius for the finish requirements
- Adjust cutting speed and feed rate
- Ensure adequate coolant application
- Look for vibration sources in the setup
Analysis by Iscar Tooling shows that insert nose radius has a direct correlation with achievable surface finish, with typical values being:
- 0.2mm radius: Ra 1.6-3.2μm finish potential
- 0.4mm radius: Ra 0.8-1.6μm finish potential
- 0.8mm radius: Ra 0.4-0.8μm finish potential
- 1.2mm radius: Ra 0.2-0.4μm finish potential
Dimensional Inaccuracy
When hole dimensions deviate from specifications:
- Check for tool deflection under cutting forces
- Verify calibration of adjustment mechanisms
- Ensure thermal stability of the machine and workpiece
- Check for wear in machine components
- Account for material springback in finishing passes
Research by the Metrology Institute indicates that thermal effects account for approximately 40-70% of dimensional variations in precision boring operations, with a typical steel workpiece expanding by 0.011mm per meter for each 1°C temperature increase.
Vibration and Chatter
When vibration affects cutting performance:
- Reduce tool overhang
- Switch to a larger diameter or anti-vibration boring bar
- Adjust cutting parameters to avoid harmonic frequencies
- Improve workpiece clamping rigidity
- Consider alternative tool paths or cutting strategies
Testing by Sandvik Coromant has established that the damping ratio of boring bars (a measure of vibration absorption capability) ranges from 0.02-0.04 for solid carbide bars, 0.04-0.07 for steel bars, and 0.15-0.25 for specialized anti-vibration boring bars.
Chip Control Problems
When chips interfere with the boring process:
- Select inserts with appropriate chipbreaker geometry
- Adjust feed rates to control chip formation
- Implement peck boring cycles for deep holes
- Ensure adequate coolant pressure and direction
- Consider vacuum or air-blast chip evacuation systems
Studies by the Manufacturing Research Laboratory found that chip evacuation problems caused 32% of quality issues in deep boring operations, with hole depths exceeding 5× diameter being particularly problematic without specialized chip control strategies.
By systematically addressing these common issues, machinists can maintain productivity and quality in their boring operations.
11. Advances in Boring Tool Technology
The field of boring tools continues to evolve with technological advancements that enhance precision, productivity, and versatility:
Material Innovations
- Ultra-fine grain carbides for improved edge strength
- Advanced coating technologies for extended tool life
- Hybrid materials combining toughness and wear resistance
- Specialized substrates for particular material groups
According to research by the Cutting Tool Engineering Association, modern PVD coatings like AlTiN and TiAlSiN can extend boring tool life by 200-400% compared to uncoated tools when machining hardened steels (45-62 HRC). Market data indicates that coated tooling now represents over 78% of all boring tool sales, up from 45% a decade ago.
Design Enhancements
- Modular boring systems for increased flexibility
- Optimized edge geometries for specific applications
- Improved dampening mechanisms for vibration control
- Quick-change systems for reduced setup time
Industry studies show that modular boring systems reduce tooling inventory requirements by 40-60% while decreasing setup times by 30-75% compared to traditional dedicated boring tools.
Digital Integration
- Smart boring tools with embedded sensors
- Real-time monitoring of cutting conditions
- Integration with machine control systems
- Adaptive boring systems that adjust to changing conditions
Research by the Manufacturing Technology Centre shows that smart tooling systems with embedded sensors can detect tool wear conditions with 92-96% accuracy and predict remaining tool life within ±12% based on real-time vibration and force measurements.
Precision Advancements
- Sub-micron adjustment capabilities
- Thermal compensation systems
- Automated calibration procedures
- Enhanced measurement feedback loops
Modern digital boring heads from manufacturers like Big Kaiser and D’Andrea offer adjustment resolution of 0.001mm (1 micron) with repeatability of ±0.002mm across the entire adjustment range, enabling “closed-loop” manufacturing where in-process measurement directs automatic tool adjustments.
These technological advances continue to push the boundaries of what’s possible in boring operations, enabling manufacturers to achieve ever-higher levels of precision and productivity.
12. Conclusion
Boring tools represent a critical category of machining instruments that enable precision manufacturing across numerous industries. From understanding what boring is in machining to selecting the right tool for specific applications, mastering boring operations unlocks the ability to create precise internal features in machined components.
Whether using a small tool for boring holes in delicate parts or a robust boring system for large industrial components, the principles of effective boring remain consistent: rigidity, precision, and appropriate cutting parameters. By understanding the types of boring tools available, their applications, and best practices for their use, manufacturers can achieve the dimensional accuracy and surface finish quality that modern engineering demands.
The market for precision boring tools continues to grow, with industry projections estimating the global boring tools market to reach $4.8 billion by 2028, driven largely by increasing precision requirements in aerospace, medical, and automotive applications. As manufacturing technology continues to advance, boring tools will evolve to meet the challenges of new materials, tighter tolerances, and more complex geometries. For machinists and manufacturing engineers alike, maintaining current knowledge of boring tool technology remains essential to competitive success in precision manufacturing.