В мире механической и металлообрабатывающей промышленности выбор правильного инструментального материала может иметь решающее значение для производительности, точности и рентабельности. Два наиболее распространенных материала, используемых в режущих инструментах, - это твердый сплав и быстрорежущая сталь (HSS). Каждый из них обладает своим набором преимуществ и недостатков, что делает их подходящими для разных областей применения. В этом подробном руководстве мы рассмотрим различия между инструментами из твердого сплава и быстрорежущей стали в различных областях применения, что поможет вам принять обоснованное решение для ваших конкретных нужд.
Понятие твердосплавной стали и твердого сплава
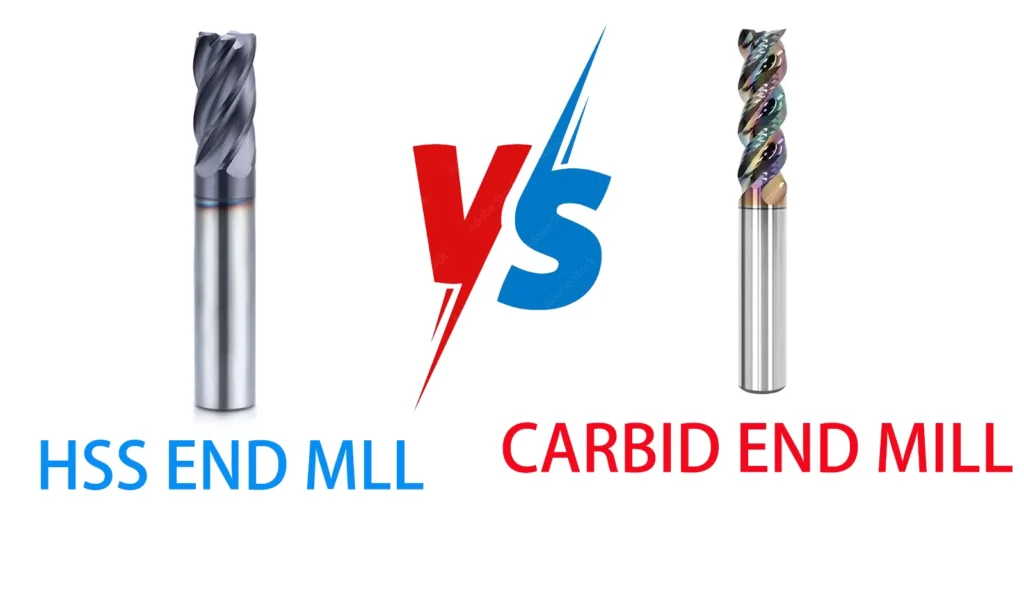
Прежде чем перейти к рассмотрению конкретных типов инструментов, необходимо понять основные свойства твердого сплава и быстрорежущей стали.
Карбид, также известный как цементированный карбид или карбид вольфрама, представляет собой композитный материал, состоящий из частиц карбида вольфрама, соединенных металлическим связующим, обычно кобальтом. Он известен своей исключительной твердостью, износостойкостью и способностью сохранять остроту режущей кромки при высоких температурах.
Быстрорежущая сталь (HSS) - это легированная сталь, содержащая значительное количество вольфрама, молибдена, ванадия и хрома. Она обладает хорошей твердостью и вязкостью и может выдерживать более высокие температуры резания, чем обычная углеродистая сталь.
В целом, твердый сплав более твердый и износостойкий, чем быстрорежущая сталь, что позволяет увеличить скорость резания и срок службы инструмента. Однако быстрорежущая сталь более твердая и менее хрупкая, что делает ее более устойчивой к ударам и вибрации. Кроме того, инструменты из быстрорежущей стали обычно дешевле своих твердосплавных аналогов.
Твердосплавные метчики в сравнении с метчиками из быстрорежущей стали
Когда речь идет о нарезании резьбы, и твердосплавные, и быстрорежущие пластины имеют свое место.
Преимущества твердосплавных метчиков
- Более высокая скорость резки, что приводит к увеличению производительности
- Отличная износостойкость, что увеличивает срок службы инструмента
- Превосходная производительность при работе с более твердыми материалами
- Лучшее качество резьбы в некоторых областях применения
Недостатки твердосплавных метчиков
- Дороже, чем метчики из быстрорежущей стали
- Более хрупкие и подвержены поломкам при неправильном использовании
- Требуется более жесткая настройка станков для предотвращения сколов
Преимущества метчиков из быстрорежущей стали
- Более щадящий режим при менее жестких настройках
- Низкая стоимость, что делает их экономичными для небольших серий.
- Легче затачивать, что продлевает срок службы.
- Лучшая производительность при работе с мягкими, липкими материалами
Недостатки метчиков из быстрорежущей стали
- Более низкие скорости резания по сравнению с твердым сплавом
- Сокращение срока службы инструмента при работе с абразивными материалами
- Может испытывать трудности при работе с очень твердыми материалами
Лучшие приложения
- Используйте твердосплавные метчики для крупносерийного производства, работы с более твердыми материалами (>35 HRC), а также в тех случаях, когда очень важно высокое качество резьбы.
- Выбирайте метчики из быстрорежущей стали для нарезания резьбы общего назначения, работы с более мягкими материалами, а также в тех случаях, когда жесткость станка может быть проблемой.
Сверла из твердого сплава и быстрорежущей стали
Сверла необходимы для многих операций обработки, и выбор между твердосплавными и быстрорежущими сверлами может существенно повлиять на производительность.
Твердосплавные сверла
- Обеспечивают более высокие скорости резки и подачи
- Обеспечивают более длительный срок службы инструмента, особенно при работе с абразивными материалами
- Обеспечивают более высокую точность отверстий и чистоту поверхности
- Превосходное сверление твердых материалов
Сверла из быстрорежущей стали
- Экономичнее для малосерийного производства
- Менее хрупкий, что снижает риск поломки в нестабильных условиях
- Легче затачивать, часто по нескольку раз
- Хорошо работают с широким спектром распространенных материалов
Соображения по поводу стоимости
Сверла из твердого сплава обычно дороже, но могут быть более рентабельными при крупносерийном производстве благодаря более длительному сроку службы и высокой производительности. Сверла из быстрорежущей стали более бюджетны для периодического использования или небольших мастерских.
Подходящие материалы и применение
- Используйте твердосплавные сверла для обработки твердых металлов, композитов и абразивных материалов, особенно в крупносерийном производстве.
- Выбирайте сверла из быстрорежущей стали для сверления более мягких металлов, дерева и пластмасс общего назначения, особенно при небольших объемах работ или разнообразном применении.
Концевые фрезы из твердого сплава и быстрорежущей стали
Концевые фрезы - это универсальные режущие инструменты, используемые при фрезеровании, и выбор между твердосплавными и быстрорежущими фрезами может значительно повлиять на эффективность обработки.
Скорость резки и подача
Твердосплавные концевые фрезы могут работать на значительно более высоких скоростях резания и подачах по сравнению с быстрорежущей сталью. Это позволяет быстрее снимать материал и повышать производительность.
Срок службы инструмента и износостойкость
Твердосплавные концевые фрезы обычно обладают более высокой износостойкостью, сохраняя свою режущую кромку дольше, чем фрезы из быстрорежущей стали, особенно при обработке более твердых материалов. Однако концевые фрезы из быстрорежущей стали более устойчивы к ударам и могут быть более щадящими в менее стабильных условиях обработки.
Точность обработки и чистота поверхности
Твердосплавные концевые фрезы, как правило, обеспечивают лучшее качество обработки поверхности и более жесткие допуски благодаря своей жесткости и устойчивости к отклонениям. Концевые фрезы из быстрорежущей стали могут требовать более низких скоростей для достижения сравнимого качества обработки.
Токарные инструменты из твердого сплава и быстрорежущей стали
Токарные инструменты имеют решающее значение для токарных работ, и выбор между твердосплавными и быстрорежущими инструментами зависит от различных факторов.
Эффективность резки различных материалов
Токарные инструменты из твердого сплава превосходно справляются с обработкой более твердых материалов и сохраняют стабильную производительность на высоких скоростях. Инструменты из быстрорежущей стали более универсальны и хорошо работают с широким спектром материалов мягкой и средней твердости.
Теплостойкость и требования к охлаждению
Твердосплавные инструменты выдерживают более высокие температуры резания, что часто позволяет вести сухую обработку или сократить использование СОЖ. Инструменты из быстрорежущей стали обычно требуют большего охлаждения для поддержания режущей кромки.
Геометрия и универсальность инструмента
Токарные инструменты из быстрорежущей стали легко обтачиваются до сложной геометрии, что делает их универсальными для индивидуального профилирования. Твердосплавные инструменты часто поставляются в виде пластин с заранее заданной геометрией, которую можно быстро изменить, но при этом они могут предложить меньше возможностей для индивидуальной обработки.
Твердосплавные и твердосплавные лезвия рубанка
В деревообработке выбор между твердосплавными и быстрорежущими лезвиями рубанка может повлиять на качество и эффективность вашей работы.
Сохранение кромки и острота
Ножи для рубанков из твердого сплава сохраняют остроту кромки гораздо дольше, чем из быстрорежущей стали, особенно при работе с твердыми породами дерева или композитными материалами. Лезвия из быстрорежущей стали могут требовать более частой заточки, но позволяют добиться очень острой кромки.
Устойчивость к ударам и долговечность
Ножи для рубанков из быстрорежущей стали обычно более устойчивы к ударам о сучки или посторонние предметы в древесине. Твердосплавные лезвия более твердые, но более хрупкие и могут расколоться при столкновении с металлом или камнями.
Экономичность при различных видах деревообработки
Для любителей или случайных пользователей лезвия из быстрорежущей стали представляют собой хороший баланс между производительностью и доступностью. Для профессиональных деревообработчиков или тех, кто работает с экзотическими твердыми породами дерева, более длительный срок службы и стабильная работа твердосплавных лезвий могут оправдать более высокую первоначальную стоимость.
Токарные инструменты по дереву из твердого сплава и быстрорежущей стали
Для токарных работ по дереву требуются инструменты, способные справиться с уникальными задачами по обработке древесины.
Производительность токарной обработки различных пород древесины
Токарные резцы по дереву из твердого сплава отлично справляются с обработкой твердых пород древесины и сохраняют стойкость кромки. Инструменты из быстрорежущей стали более универсальны и легко затачиваются для работы с различными породами древесины и техниками точения.
Простота заточки и обслуживания
Токарные инструменты по дереву из быстрорежущей стали можно быстро подправить с помощью настольного шлифовального станка или точильного камня, что позволяет часто перетачивать их в процессе работы. В инструментах из твердого сплава часто используются сменные вставки, что исключает необходимость заточки, но требует замены при затуплении.
Долгосрочная стоимость и инвестиции
Токарные инструменты из твердого сплава имеют более высокую начальную стоимость, но их долговечность и стабильная работа делают их выгодным вложением для серьезных токарей по дереву. Инструменты из быстрорежущей стали отличаются более низкой первоначальной стоимостью и больше подходят для новичков или тех, кому нравится процесс обслуживания инструмента.
HSS vs Кобальт vs Твердый сплав
Рассматривая материалы для режущих инструментов, стоит упомянуть кобальтовую сталь как альтернативу стандартной быстрорежущей стали и твердому сплаву.
Сравнение твердости и износостойкости
Твердый сплав - самый твердый и износостойкий, за ним следует кобальтовая сталь, а HSS - самая мягкая из трех. Это означает, что инструменты из твердого сплава дольше сохраняют кромку, особенно в сложных условиях эксплуатации.
Теплостойкость и скорость резки
Твердосплавные инструменты выдерживают самые высокие температуры резания, обеспечивая самые высокие скорости резания. Кобальтовая сталь обладает повышенной жаростойкостью по сравнению со стандартной быстрорежущей сталью, что позволяет использовать ее для средних скоростей резания.
Компромиссы между стоимостью и производительностью
Инструменты из быстрорежущей стали наиболее экономичны, но могут требовать более частой замены. Инструменты из кобальтовой стали занимают промежуточное положение, обладая улучшенными характеристиками по сравнению с инструментами из быстрорежущей стали при более низкой стоимости по сравнению с твердосплавными. Инструменты из твердого сплава являются самыми дорогими, но часто обеспечивают наилучшую долгосрочную стоимость при больших объемах работ или в сложных условиях применения.
Заключение
Выбор между инструментами из твердого сплава и быстрорежущей стали требует тщательного рассмотрения ваших конкретных потребностей в обработке, бюджета и долгосрочных целей. В то время как инструменты из твердого сплава обычно обладают более высокой твердостью, износостойкостью и скоростью резания, инструменты из быстрорежущей стали обеспечивают универсальность, ударопрочность и экономическую эффективность для многих областей применения.
Ключевые факторы, которые следует учитывать при выборе, включают:
- Обрабатываемый материал
- Объем производства
- Возможности и жесткость оборудования Первоначальный бюджет против долгосрочных затрат
- Требуемая шероховатость поверхности и допуски
- Уровень квалификации и предпочтения оператора
По мере развития технологий обработки можно ожидать дальнейших улучшений в формулах инструментов из твердого сплава и быстрорежущей стали. Кроме того, разработка новых технологий нанесения покрытий и гибридных материалов может еще больше размыть границы между этими двумя непоколебимыми вариантами оснастки.
В конечном счете, лучший выбор часто зависит от нахождения правильного баланса между производительностью и стоимостью для вашей конкретной задачи. Понимая сильные и слабые стороны инструментов из твердого сплава и быстрорежущей стали, вы сможете принимать обоснованные решения, которые позволят оптимизировать процессы обработки и повысить общую производительность.
Чем отличаются быстрорежущая сталь и карбид вольфрама?
Быстрорежущая сталь в основном состоит из железа с добавлением карбидообразующих легирующих элементов, а карбид вольфрама в основном состоит из частиц карбида вольфрама, соединенных кобальтом. Быстрорежущая сталь обладает превосходной горячей твердостью, а карбид вольфрама - повышенной твердостью и износостойкостью.
Каковы различные области применения быстрорежущей стали и карбида вольфрама?
Быстрорежущая сталь часто используется для изготовления режущих инструментов, таких как сверла, концевые фрезы и т.д. Карбид вольфрама часто используется для изготовления инструментов для непрерывного и прерывистого резания, таких как точение, фрезерование, развертывание и т.д.
Каковы преимущества и недостатки твердосплавных и вольфрамовых резцов?
Плюсы быстрорежущей стали - низкая стоимость и хорошая обрабатываемость; минусы - меньшая твердость и износостойкость. Плюсы карбида вольфрама - высокая твердость и износостойкость; минусы - высокая стоимость и хрупкость.
Как сравниваются скорости резания при обработке быстрорежущей стали и карбида вольфрама?
При одинаковых условиях резания скорость резания карбида вольфрама в 3-5 раз выше, чем у быстрорежущей стали.
В чем разница в сроке службы инструментов из быстрорежущей стали и карбида вольфрама?
При одинаковых условиях резания срок службы инструмента из карбида вольфрама может быть в несколько раз, а то и в десятки раз больше, чем у инструмента из быстрорежущей стали.