U-образное сверло, один из наиболее часто используемых инструментов для обработки отверстий, обычно называется по-разному: неглубокое сверло, водоструйное сверло, агрессивное сверло, быстрое сверло, T-сверло, вставное сверло и т.д. Стандартное название - сверло со сменными вставками или сверло с машинным патроном. Термин "U-сверло" берет свое начало от U-сверла Sandvik Coromant T-MAX, которое затем получило широкое распространение в промышленности и постепенно превратилось в общепринятое название.
Какие типы вставок используются в U-образных сверлах?
Существует несколько распространенных типов SPMG, SOMT, WCMTWCMX, конкретные данные можно найти в следующей таблице.

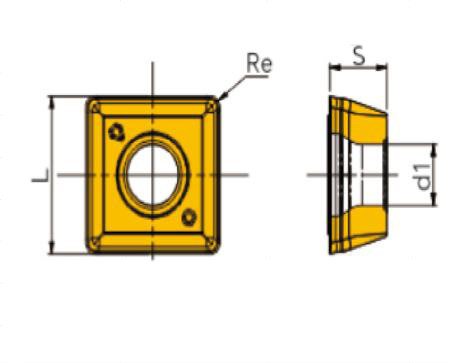
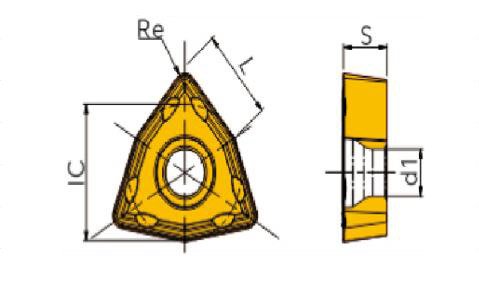
Модель | L | S | RE |
---|---|---|---|
SOMT050204-PC FPA010 | 4.9 | 2.38 | 0.4 |
SOMT060204-PC FPA010 | 5.7 | 2.38 | 0.4 |
SOMT070306-PC FPA010 | 6.8 | 2.8 | 0.6 |
SOMT08T306-PC FPA010 | 7.9 | 3.97 | 0.6 |
SOMT09T308-PC FPA010 | 9.2 | 3.97 | 0.8 |
SOMT11T308-PC FPA010 | 11 | 3.97 | 0.8 |
SOMT130408-PC FPA010 | 12.8 | 4.4 | 0.8 |
SOMT150510-PC FPA010 | 15 | 4.8 | 1 |
Модель | L | S | RE |
---|---|---|---|
SPMG050204-EC FPA010 | 5 | 2.38 | 0.4 |
SPMG060204-EC FPA010 | 6 | 2.38 | 0.4 |
SPMG07T308-EC FPA010 | 7.94 | 3.97 | 0.8 |
SPMG090408-EC FPA010 | 9.8 | 4.3 | 0.8 |
SPMG110408-EC FPA010 | 11.5 | 4.8 | 0.8 |
SPMG140512-EC FPA010 | 14.3 | 5.2 | 1.2 |
Модель | L | IC | S | RE |
---|---|---|---|---|
WCMT030208-TM FPA005 | 3.8 | 5.56 | 2.38 | 0.8 |
WCMT040208-TM FPA005 | 4.3 | 6.35 | 2.38 | 0.8 |
WCMT050308-TM FPA010 | 5.4 | 7.94 | 3.18 | 0.8 |
WCMT06T308-TM FPA010 | 6.5 | 9.525 | 3.97 | 0.8 |
WCMT080412-TM FPA010 | 8.7 | 12.7 | 4.76 | 1.2 |
Чаще всего используются типы WC, SP и SO. Учения пластины в металлообработке. Для операций сверления хорошо подходят сверла со сменными пластинами, поскольку они сокращают время смены инструмента. Очень успешной является техника использования сверл u в качестве черновой обработки. Глубокие полости или отверстия можно создать путем выполнения нескольких осевых резов сверлом или фрезой. Этот метод особенно подходит для черновой обработки. Поскольку основные силы резания сосредоточены в осевом направлении вдоль шпинделя, он является энергосберегающим, эффективным и снижает требования к шпинделю станка. Сверление отверстий под пластинчатый сверлильный инструмент является первым этапом процесса внутреннего фрезерования пластин. Уникальный стружколоматель имеет единственную в своем роде конструкцию с гофрированными кромками. Это обеспечивает высокую прочность кромок и эффективное стружкодробление.
Советы по обработке с помощью U-образных сверлильных вставок
Сверление неровной поверхности
Нерегулярные
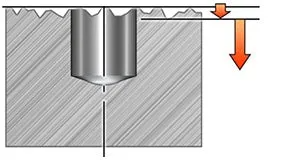
Выпуклый
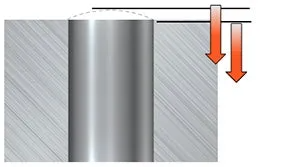
Вогнутый
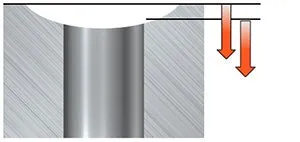
- Используйте максимально короткие сверла, чтобы свести к минимуму вибрацию и уменьшить влияние прогиба.
- Рекомендуемые начальные значения скорости резания и минимальная рекомендуемая подача
- Не рекомендуется использовать 6-7×DC, если радиус вогнутости равен или меньше радиуса сверла
Предварительно просверленные отверстия
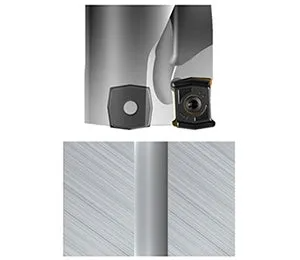
Для поддержания баланса силы резания между центральной и периферийной пластиной на приемлемом уровне, предварительно просверленное отверстие не должно быть больше DC/4
Сверление поперечных отверстий
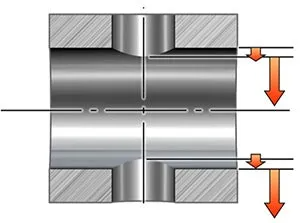
Задачи:
- Эвакуация чипов затронута, может стать более проблематичной
- Снимать заусенцы в переходе очень сложно. Образование заусенцев должно быть как можно меньше
- Вызывает больший износ инструмента, чем обычное сверление
Рекомендации:
- Для отверстий разного диаметра: сначала просверлите большее отверстие, чтобы уменьшить образование заусенцев
- Начните с минимальной рекомендованной подачи при пересечении отверстий
- Не рекомендуется использовать материалы с длинным сколом из-за необходимости удаления стружки при прохождении отверстий
Бурение наклонных входов/выходов
Создает неравномерные и чрезмерные усилия, действующие на режущие кромки
- Прерывистая резка при входе/выходе сверла из заготовки
- Повышает вероятность вибрации
- Может исказить профиль сверления
- Вызывает больший износ инструмента, чем обычное сверление
Общие рекомендации:
- Стабильность имеет решающее значение. Небольшое отношение длины к диаметру поможет сохранить допуски
- Фрезерование небольшой плоской поверхности рекомендуется при обработке заготовок с большим наклоном
Угловые или наклонные поверхности, вход
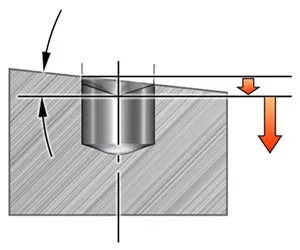
- Используйте максимально короткие сверла, чтобы свести к минимуму вибрацию и уменьшить влияние прогиба.
- Начните с минимальной рекомендованной скорости резки и 1/3 минимальной рекомендованной подачи (или ниже) до полного включения, а затем вернитесь к нормальной подаче.
- 4-5×DC наклонный вход может быть наклонен под углом до 15º
- 6-7×DC наклонный вход может быть наклонен до 10º
Угловые или наклонные поверхности, выход
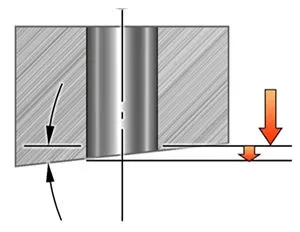
- Используйте максимально короткие сверла, чтобы свести к минимуму вибрацию и уменьшить влияние прогиба.
- Рекомендуемые начальные значения скорости резания и минимальная рекомендуемая подача (или ниже)
- 4-5×DC наклонный выход может быть наклонен под углом до 15º
- 6-7×DC наклонный выход может быть наклонен до 5º
Сверление асимметрично изогнутых поверхностей
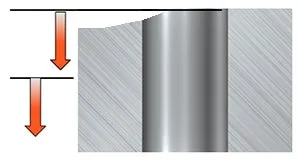
- Используйте как можно более короткое сверло, чтобы минимизировать изгиб сверла от центра, подобно наклонной поверхности
- Уменьшите подачу до 1/3 от начальной скорости проникновения для вогнутых поверхностей
- Радиус изогнутой поверхности должен быть больше радиуса сверла
- Не рекомендуется использовать дрели с 6-7×DC
Как работают сверлильные вставки U и каковы области их применения
U-образное сверло, также известное как сверло со сменными пластинами, - это инструмент, используемый в основном для высокопроизводительного сверления отверстий в различных материалах. Ниже приводится подробное описание работы U-образного сверла:
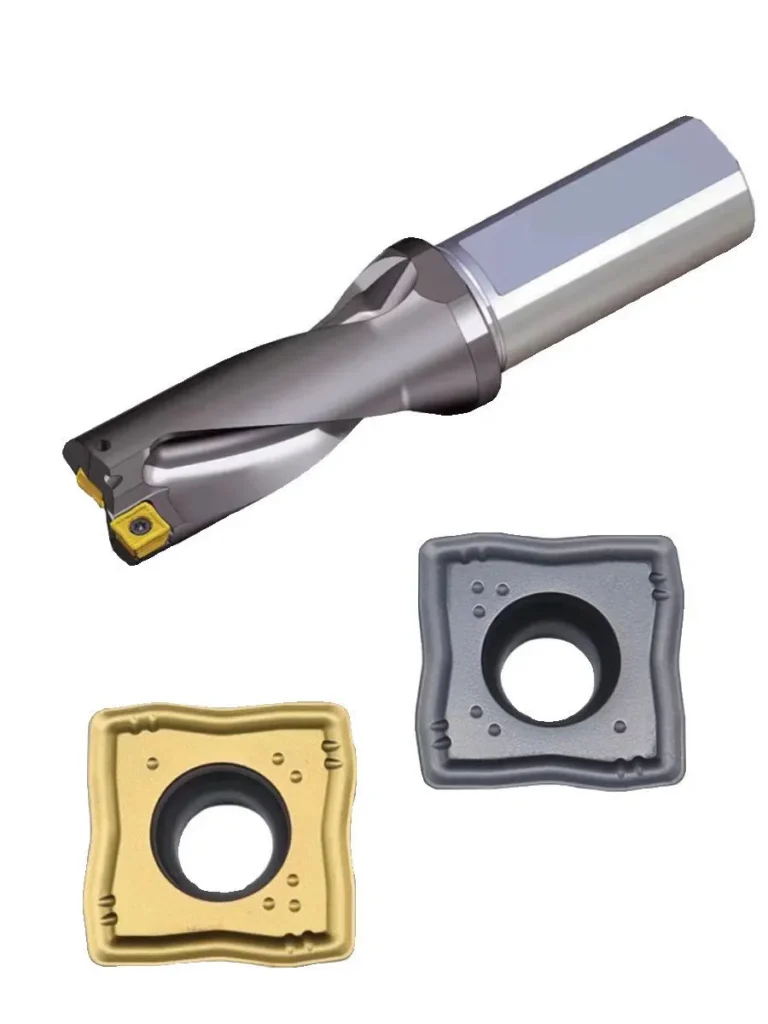
1. Компоненты и структура
- U-образный корпус бура: Это основная часть U-образного сверла, обычно изготовленная из прочного материала. Она имеет два посадочных места для пластин: одно в центре и одно на периферии. В этих гнездах размещаются сменные пластины (режущие кромки).
- Вставки: В сверлах U используются две сменные вставки:. центральная вставка и периферийная вставка. Центральная пластина режет материал в сердцевине отверстия, а периферийная - по внешним краям. Внешняя пластина обычно выполняет больший объем работы, так как имеет большую поверхность резания.
2. Процесс резки
- Двойное режущее действие: При вращении U-образного сверла на высокой скорости обе пластины одновременно входят в заготовку. Центральная пластина режет внутреннюю часть отверстия, а внешняя - наружный диаметр. Такая комбинация делает U-образное сверло высокоэффективным, поскольку нагрузка при резании распределяется между двумя пластинами.
- Система охлаждения: U-образные сверла обычно имеют внутренние каналы для охлаждающей жидкости. СОЖ течет по этим каналам и непосредственно охлаждает зону резания, уменьшая нагрев и трение. Это также помогает вымыть стружку из просверленного отверстия.
3. Буровые работы
- Выравнивание и позиционирование: Перед сверлением заготовка прочно закрепляется на столе станка или в приспособлении. Центр U-образного сверла выравнивается по месту предполагаемого отверстия с помощью программирования ЧПУ или ручного позиционирования.
- Инициирование разреза: Шпиндель станка вращается, и U-образное сверло начинает двигаться в заготовке. Центральная пластина начинает резать, высверливая сердцевину, за ней следует периферийная пластина. По мере проникновения инструмента вглубь обе пластины продолжают эффективно удалять материал.
- Эвакуация чипов: При отрезании материала образуется стружка. Эта стружка выводится из отверстия под действием вращающихся пластин и внутренней охлаждающей жидкости, которая помогает удалить стружку и предотвратить засорение.
- Завершение бурения: Как только U-образное сверло достигает запрограммированной глубины, инструмент втягивается, оставляя после себя готовое отверстие. Благодаря высокой точности пластин и конструкции корпуса инструмента отверстие обычно получается точным и не требует дополнительной обработки.
4. Преимущества U-образных дрелей
- Высокая эффективность: Поскольку U-образное сверло использует две пластины для одновременной резки, оно работает на гораздо более высоких скоростях и подачах по сравнению с традиционными сверлами, что сокращает время цикла.
- Точность: Конструкция U-образного сверла обеспечивает точный диаметр отверстий, что часто устраняет необходимость в дополнительных финишных операциях, таких как растачивание или развертывание.
- Эффективность охлаждающей жидкости: Встроенные каналы охлаждающей жидкости сохраняют пластины холодными во время высокоскоростного сверления, снижая износ и продлевая срок службы инструмента.
5. Эксплуатационные соображения
- Выбор вставки: Очень важно выбрать правильный материал и геометрию пластины в зависимости от материала заготовки (например, сталь, алюминий, чугун). Использование правильных пластин обеспечивает более гладкие резы и продлевает срок службы инструмента.
- Параметры резки: Скорость сверления и подачу следует регулировать в зависимости от материала и глубины отверстия. Если скорость подачи слишком высока, это может привести к чрезмерному износу или повреждению пластин.
- Расход охлаждающей жидкости: Убедитесь, что система охлаждения правильно настроена и функционирует. Недостаточное количество охлаждающей жидкости может привести к перегреву и преждевременному выходу инструмента из строя.
Что такое U-образные сверлильные вставки и почему они популярны?
Пластины для U-образных сверл - это режущие инструменты, используемые в сменных U-образных сверлах, специально разработанных для высокоэффективного сверления отверстий. Эти пластины обычно изготавливаются из карбида или других твердых материалов, которые способны выдерживать высокие скорости и температуры резания. Они являются сменными, то есть если пластина затупилась, ее можно заменить вместо замены всего сверла, что делает их экономически эффективными.
почему популярны U-образные сверлильные вставки:
Высокая эффективность: U-образные сверла со вставками могут сверлить отверстия гораздо быстрее, чем традиционные спиральные сверла, поскольку для резки используются одновременно две вставки - одна для центра отверстия, другая - для его периметра. Это значительно сокращает время обработки.
Экономичность: Поскольку вставки являются сменными, общая стоимость инструмента снижается. Вместо замены всего сверла необходимо заменить только изношенные вставки.
Универсальность: U-образные сверлильные вставки можно использовать в различных материалах, таких как сталь, нержавеющая сталь, чугун и цветные металлы. Для различных областей применения предлагаются различные геометрии и покрытия.
Точность: U-образные сверлильные вставки обеспечивают высокую точность при сверлении, часто создавая отверстия с минимальной потребностью во вторичной обработке, такой как растачивание или развертывание.
Подача охлаждающей жидкости: Многие U-образные сверла имеют внутренние каналы для подачи СОЖ, которые охлаждают пластины во время сверления, улучшая срок службы инструмента и отвод стружки.
Важные соображения при использовании U-образных сверлильных вставок
Для обеспечения оптимальной производительности при использовании U-образных сверлильных вставок необходимо учитывать несколько факторов:
1. Выбор материала вставки
Выберите правильный материал вставки (твердый сплав, твердый сплав с покрытием и т.д.) в зависимости от материала заготовки. Для достижения наилучших результатов в разных материалах требуются особые пластины. Например, для сверления твердых сталей могут потребоваться более жесткие пластины, а для более мягких материалов, таких как алюминий, может потребоваться более специализированная геометрия пластин.
2. Скорость резания и скорость подачи
Скорость резания и подача должны соответствовать материалу заготовки и типу пластины. Слишком высокая скорость подачи может привести к поломке пластины, а слишком низкая - к плохому образованию стружки или чрезмерному нагреву.
Обратитесь к руководству производителя для получения информации о рекомендуемых скоростях и подачах, регулируя их в зависимости от твердости материала и глубины отверстия.
3. Управление охлаждающей жидкостью
Убедитесь, что охлаждающая жидкость правильно направлена в зону резания. Охлаждающая жидкость помогает снизить нагрев, предотвратить износ инструмента и способствует отводу стружки. U-образные сверла часто поставляются с внутренними каналами охлаждающей жидкости, но вы должны убедиться, что эти каналы работают правильно.
Использование недостаточного количества СОЖ или засорение канала СОЖ может привести к перегреву, сокращению срока службы инструмента и ухудшению качества отверстий.
4. Правильная установка вставки
Убедитесь, что вставки правильно установлены и закреплены в корпусе U-образного сверла. Неправильная установка может привести к смещению вставок, ухудшению качества отверстий или даже к повреждению корпуса инструмента.
Периодически проверяйте износ пластин и заменяйте их, когда они затупятся, чтобы не повредить заготовку или инструмент.
5. Эвакуация чипов
Следите за удалением стружки в процессе сверления. Плохое удаление стружки может привести к закупорке отверстия, что приведет к поломке инструмента, перегреву или повреждению заготовки.
Отрегулируйте скорость подачи или расход охлаждающей жидкости, если стружка неэффективно удаляется из отверстия.
6. Глубина и точность отверстий
U-образные сверла идеально подходят для быстрого получения отверстий, но точность может варьироваться в зависимости от установки и материала. При выполнении глубоких отверстий необходимо обеспечить правильное выравнивание U-образного сверла, чтобы избежать отклонения, которое может привести к образованию конических или некруглых отверстий.
7. Контроль износа вставки
Следите за износом вставок во время использования. Изношенные вставки могут негативно повлиять на качество отверстий, а также привести к перегреву, увеличивая риск поломки или повреждения заготовки.
Регулярные проверки и своевременная замена пластин необходимы для поддержания качества отверстий и продления срока службы инструмента.
Следуя этим рекомендациям и используя подходящую вставку для конкретного применения, вы сможете максимально повысить эффективность, рентабельность и точность сверл U в процессе обработки
Заключение
U-сверло - это сверлильный инструмент с твердосплавными пластинами, отличающийся простотой использования и экономичностью. Чтобы облегчить обработку широкого спектра материалов, U-сверла ONMY выпускаются различных типов и размеров. U-сверла ONMY - это энергосберегающее и эффективное решение, а также высокая скорость съема металла. Для получения высококачественных U-сверлильных пластин обращайтесь в ONMY! Свяжитесь с нами, и мы с радостью ответим на любые ваши вопросы и пожелания.