Cutting tools and metal components often utilize advanced coatings like PVD vs CVD to improve surface properties like hardness, wear resistance, corrosion protection and more. But what is the difference between these two common coating processes?
In this guide, we’ll explore the key distinctions between PVD and CVD methodology, resulting coating characteristics, ideal applications, and benefits for cutting inserts and endmills.
How PVD & CVD Coating Processes Work
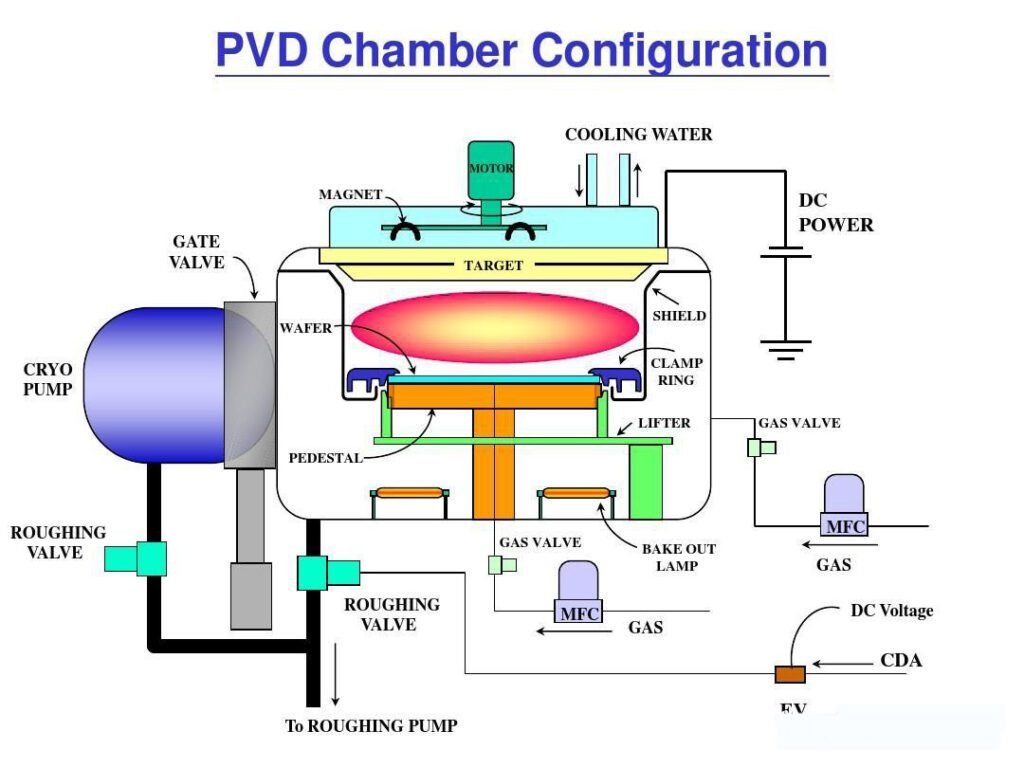
PVD (physical vapor deposition) involves placing the target substrate in a vacuum chamber, then utilizing magnetron sputtering or evaporation to vaporize the coating material. This vapor condenses and deposits uniformly onto the substrate surface as a thin film coating. Temperatures typically range from 200-500°C.
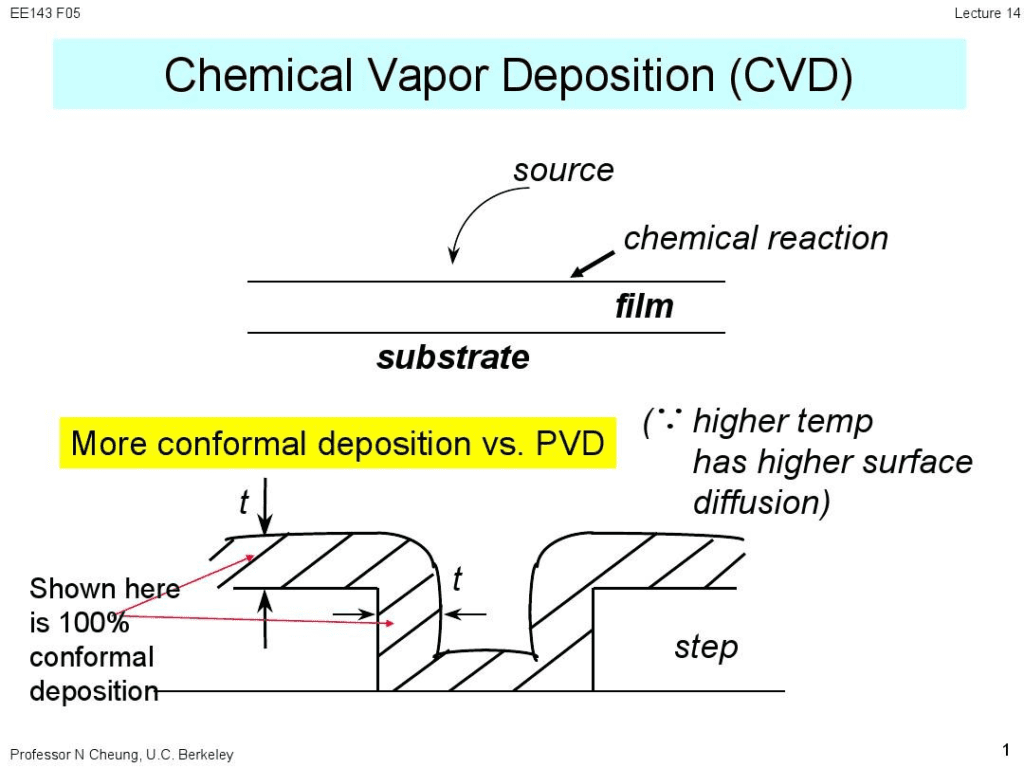
CVD (chemical vapor deposition) coats surfaces via chemical reactions between precursor gases like methane, hydrogen and ammonia. These reactants break down and react at the heated surface to deposit the desired coating uniformly. CVD reactions occur at very high temperatures of 900-1100°C.
Difference in Coating Properties & Performance
The PVD process creates thinner, more dense and uniform coatings, typically 1-5 microns thick. CVD can deposit much thicker coatings up to 30 microns with excellent adhesion, but not as uniform on complex geometries.
PVD coatings tend to be harder and more wear resistant thanks to their density. CVD coatings withstand higher temperatures, above 1000°C versus about 750°C for PVD.
Common PVD coatings are titanium nitride (TiN), titanium aluminum nitride (TiAlN), and chromium nitride (CrN). CVD options include titanium carbide (TiC), titanium nitride (TiN), and silicon carbide (SiC).
Best Applications for PVD & CVD
PVD’s ability to uniformly coat small, complex components makes it ideal for cutting tools like endmills, surgical instruments, engine components and decorative finishes.
CVD’s excellent adhesion and heat resistance suit it to alloying machine parts, diffusion barriers in semiconductors, and corrosion protection coatings.
PVD vs CVD for Milling Inserts & Cutting Tools
For milling inserts and cutting tools, PVD’s hardness improves wear resistance and tool life. However, CVD coatings allow lower cutting forces. CVD also withstands higher cutting temperatures better.
PVD coated endmills excel in high speed machining of aluminum and non-ferrous alloys. CVD inserts perform well in titanium, nickel and cobalt alloys. For optimal performance, choose PVD or CVD coatings suited to your workpiece.
Is CVD or PVD better for cutting tools? Why?
PVD often imparts better hardness while CVD offers higher temperature resistance. PVD works best for high speed non-ferrous machining while CVD suits tough materials like titanium.
What are the temperature limitations for PVD vs CVD coatings?
PVD coatings perform well up to about 750°C while CVD coatings can withstand over 1000°C in many cases.
Which coating typically has better adhesion – PVD or CVD?
CVD coatings generally have superior adhesion to the substrate thanks to the high temperature chemical bonding process.
What industries rely most on PVD and CVD coatings?
PVD is widely used in medical, aerospace, automotive, plastic injection molding. CVD is common in aerospace, power generation, semiconductors, and optics.
How thick can CVD coatings be applied compared to PVD?
CVD commonly deposits coatings up to 30 microns thick due to the chemical reactions. PVD is limited to thinner coatings, typically under 5 microns.
Conclusion
Understanding the distinct advantages of both PVD and CVD coating processes allows choosing the right technology for the application. PVD offers uniformity and hardness while CVD provides heat resistance and adhesion. For cutting tools, choose PVD for high precision non-ferrous work and CVD for tough materials like titanium and nickel alloys. With the right coating, machining and component performance can be optimized.