خودکار بیک اسپاٹ کا سامنا کرنے والے ٹولز
Automatic back spot facing tools is a specialized machine tool accessory designed for creating precise counterbores or spot faces on the back side of holes, particularly useful in situations where the opposite side of the workpiece cannot be accessed for conventional machining due to space constraints or the geometry of the part.
These tools operate by deploying cutting edges outward after being inserted into a pre-drilled hole, performing the machining task, and then retracting the edges to withdraw through the original hole.
Essential for manufacturing sectors requiring high precision in hard-to-reach areas, such as aerospace, automotive, and heavy machinery, autofacers significantly reduce manual labor, increase accuracy, and cut down production times by eliminating the need to reposition or manually access the workpiece’s back side.
- Reduce chip cutting time by at least 80% compared to conventional manual tools
- Eliminates costly secondary operations and saves time through clever automated process improvements
- Carbide indexable inserts for a wide range of materials to be machined
- Scientific internal mechanism ensures that the insert opens and closes accurately and reliably every time
- Tools can perform heavy interrupted cuts without excessive chatter
- Minimum guide hole diameter Ø6.5mm (Ø0.2559″)
- Unlimited depth-to-diameter ratio due to support guides
- Quick and easy tool change
- Maximum counterbore diameter up to 2.3 times the overbore diameter
- Can be equipped with a back spot facer with chamfering
ایپلی کیشنز
- Bolt head seating faces
- Differential cases – spherical and flat
- Valve seat pocketing
- Gate valves
- Planetary gear carriers
- Gearbox casings
- Landing gear
- Special inserts with chamfer and other forms on request

- Ø6.5mm minimum pilot hole
- Robust and versatile
- Back spotface, counterbore chamfer
- Back chamfer tool for vmc
- Works on interupted surfaces
- With safety pin


Performance and Benefits
- The back spot face tool is designed to automate the machining of counterbore countersinks and works without stops, reversing and any other machine aids.
- The oscillating insert retraction mechanism, combined with the principle of in-machine cooling pressure (min. 20 bar, max. 50 bar), ensures that inserts are not retracted due to swarf and dust.
- Available for both vertical and horizontal machines.
- Diameter 6.5mm-21mm is the standard product, with 0.5mm as a grade.
- Inserts cover a wide range of sizes and are made of tungsten carbide.
- The unique internal cooling chip removal design of the tool allows iron chips and dust to be removed from the insert window in a timely manner, which ensures the reliability of insert retraction.
Advanced of Safety Pin
- In case of excessive wear of the insert, it protects the workpiece, the toolholder and the machine by automatically separating the toolholder from the shank.
- It also protects the workpiece in case of program error and improper clamping of the workpiece.
Tool Description
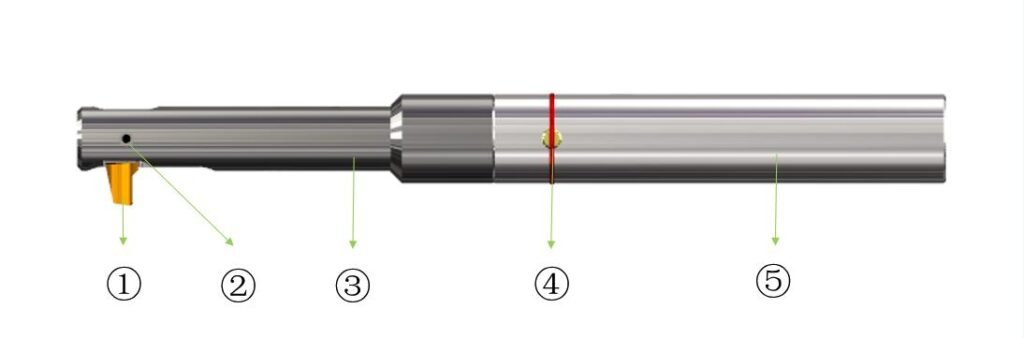
- Carbide insert
2. Locating pin
3. Tool holder
4. Safety pin
5. Tool shank
Tool Working Principle
①

②

③
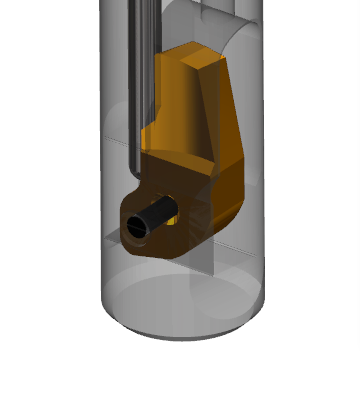
④
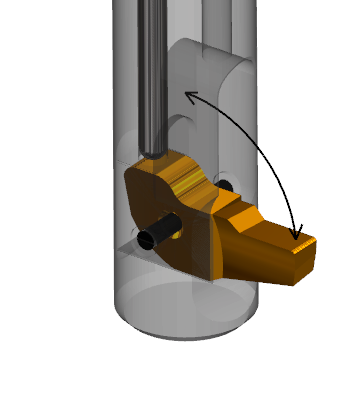
- Under coolant pressure, the piston pushes the control pin, which pushes the insert to begin retracting the insert.
- As the insert retracts into the cutter body, the pressure surface flips, and the control pin (which is still under constant pressure) continues to push the insert along the curved surface at the end of the insert until the insert is fully pushed into the cutter body.
- After the insert has been fully incorporated into the tool body by the control pin, the tool can be moved axially (Z-direction) through the workpiece overbore.
- The machine’s internal cooling is switched off, the spindle starts to rotate (at the recommended speed) and the inserts are unfolded to the working position. The internal cooling can reach the cutting edge of the insert through the cooling holes. When the counterbore countersinking is completed, the tool is returned to the machining start position. At this point, the machine’s internal cooling is turned on and the drive insert is again
retracts into the tool body again.
Processing cases
Workpiece

- Industry: Automotive
- Workpiece: Turbine housing
- Material:GGG40
- Technology: D14.0 counterbore D26.0 flat surface
- Machine: Horizontal machining center
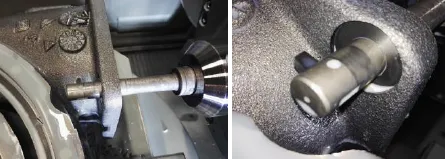
- Spindle speed:400r/min
- Feed:0.05mm/rev
Workpiece

- Industry: Automotive
- Workpiece : Steering Knuckle
- Material : Aluminum Alloy
- Process : Over ɸ13.0 and counter ɸ30.0 plane
- Machine: Vertical Machining Center
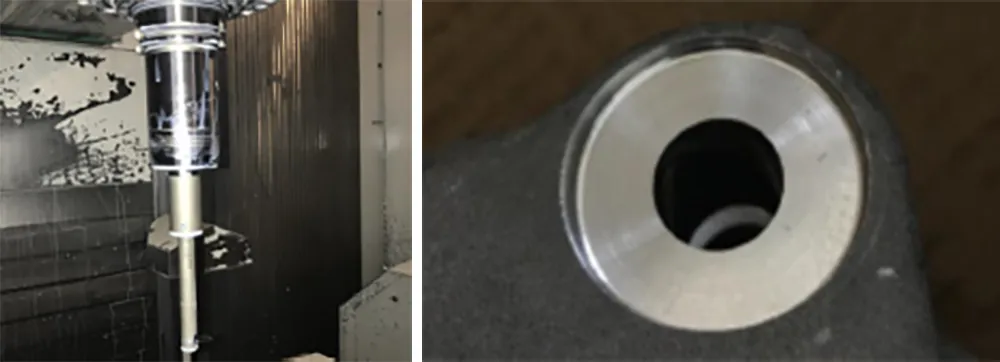
- Spindle speed:500r/min
- Feed:0.05mm/rev
Workpiece

- Industry : Marine
- Workpiece : Bearing Block
- Material : S355J2G3
- Process : Over ɸ12.8 Counter ɸ33.0 Plane
- Machine : Horizontal Machining Center

- Spindle speed:400r/min
- Feed:0.005mm/rev
The customer previously used manual tooling to machine countersunk holes. With the our autofacer back spot facing tooling there is no longer a need to install manual tooling, ensuring operator safety. The quality of the surface machining has been improved and the machining time has been greatly reduced.
Interested To Our automatic back spot facing tools?
ONMY Toolings is growing rapidly these years, and we are always welcome partners to work together to achieve manual benifits and grow together!