在精密加工的世界裡,鑽石鍍層立铣刀已經成為改變遊戲規則的工具,徹底改變了我們進行切削和銑削作業的方式。這些高性能的工具在各種材料和應用上提供了無與倫比的耐用性、精密度和多功能性。在這份全面的指南中,我們將探索金剛石塗層立铣刀的迷人領域,深入瞭解它們的類型、應用,以及它們對現代製程所產生的轉變性影響。
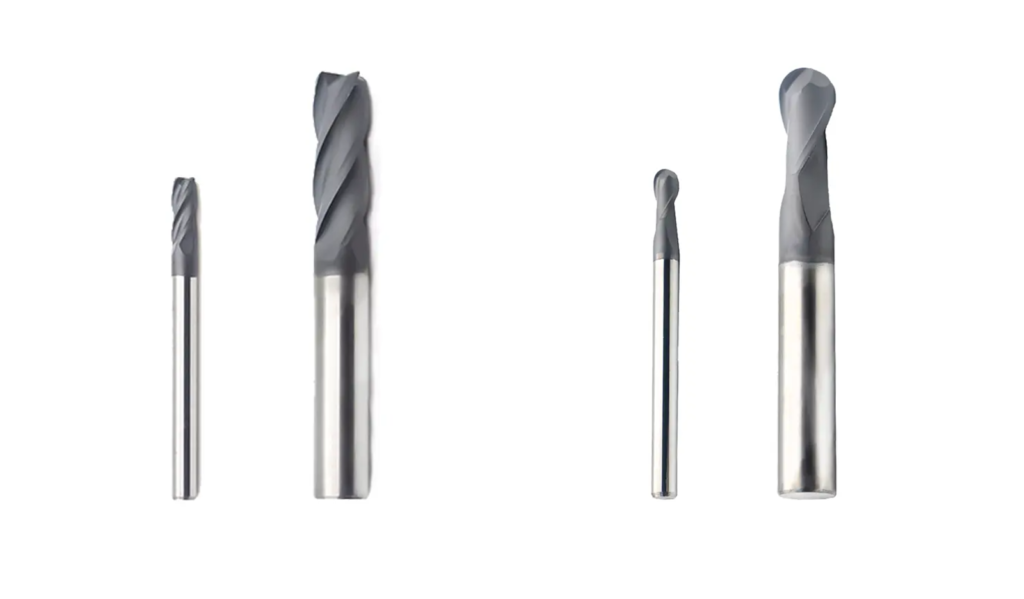
1.鑽石銑刀簡介
鑽石鍍層 立铣刀 代表了切削工具技術的頂峰,結合了鑽石的強度與傳統立铣刀設計的多功能性。這些刀具的特點是在硬質合金基材上塗上一層薄薄的金剛石材料,使切削刃具有極佳的硬度、耐磨性和熱傳導性。金剛石塗層立铣刀在從航空航天到電子等精度和效率要求極高的行業中的使用越來越普遍。
2.鑽石銑刀的種類
2.1 CVD 鍍鑽立铣刀
化學氣相沉積 (CVD) 是製造金剛石鍍層立銑刀的常用方法。CVD 金剛石塗層立铣刀以其超高的硬度和耐磨性著稱,是加工研磨材料的理想選擇。CVD 製程可產生均勻的金剛石鍍層,確保刀具切削刃的性能一致。
2.2 PVD 鍍鑽立铣刀
物理氣相沉積 (PVD) 是製造金剛石鍍層立铣刀的另一種技術。PVD 金剛石塗層立铣刀的塗層通常比 CVD 立铣刀的塗層更薄,這在某些需要保持鋒利切削刃的應用中非常有利。這些工具通常具有極佳的韌性,適用於間歇性切削作業。
2.3 非晶鑽石銑刀
無定型鑽石鍍層立铣刀是鑽石鍍層領域中的一個獨特類型。這些刀具具有非結晶金剛石結構,可在硬度和韌性之間取得平衡。無定型金剛石塗層立铣刀在需要耐磨性和耐衝擊性的應用中特別有效。
材料與應用
3.1 鍍鑽石硬質合金立铣刀
金剛石塗層硬質合金立铣刀結合了硬質合金的韌性與金剛石的優異耐磨性。這些多用途刀具適用於各種材料,包括有色金屬、複合材料及研磨材料。硬質合金基材可提供強度與剛性,而鑽石鍍層則可確保長時間的刀具壽命與優異的表面光潔度。
3.2 石墨用鑽石銑刀
在加工石墨時,金剛石塗層立铣刀是最佳選擇。石墨的磨蝕性會快速磨損傳統的切削工具,但鑽石鍍層立铣刀即使在長時間使用後仍能保持鋒利的刃口。這使得金剛石塗層立铣刀成為航空航天和能源等產業不可或缺的工具,因為這些產業的石墨零件非常普遍。
3.3 用於鋁材的鑽石銑刀
鋁加工因其容易在切削刃上形成積屑而帶來獨特的挑戰。金剛石塗層立铣刀可提供優異的排屑效果,並降低刃口積屑的風險,為鋁材加工提供解決方案。鑽石鍍層的低摩擦係數也有助於改善鋁製工件的表面光潔度。
3.4 塑膠用鑽石銑刀
在塑膠加工領域中,鑽石鍍層立铣刀的優點在於切削乾淨且刀具壽命更長。鑽石鍍層優異的散熱特性可防止塑膠材料在切削過程中熔化或變形。這使得金剛石塗層立铣刀在醫療設備製造和消費性電子產品等行業中尤為重要。
4.鑽石銑刀的優勢
使用金剛石塗層立铣刀有許多顯著的好處:
- 延長刀具壽命,減少停機時間和刀具成本
- 改善工件表面光潔度
- 提高切削速度和進給率
- 強化熱傳導性,減少加工過程中的熱量堆積
- 極佳的尺寸穩定性,確保穩定的零件品質
- 在許多應用中減少對冷卻劑的需求
5.選擇正確的鑽石銑刀
選擇合適的金剛石塗層立铣刀取決於多種因素,包括:
- 工件材料
- 所需的表面處理
- 切削參數(速度、進給、切削深度)
- 刀具幾何要求
- 塗層厚度與類型
諮詢經驗豐富的刀具專家,可協助您針對特定應用選擇最佳的金剛石塗層立铣刀。
6.鑽石銑刀的維護與保養
鑽石銑刀的正確保養對於最大化其性能和使用壽命至關重要。主要考慮因素包括
- 適當儲存以防止切削刃損壞
- 定期清潔以清除碎屑和堆積物
- 小心處理,避免鑽石鍍層崩裂或剝落
- 遵守建議的切削參數,防止過早磨損
7.中國在鑽石銑刀生產中的角色
中國已經成為金剛石塗層立铣刀生產的重要參與者。中國製造商在先進的鍍層技術和品質控制措施上投入了大量資金,使他們能夠以具有競爭力的價格生產高品質的刀具。中國金剛石塗層立铣刀的出現,使這種先進的刀具技術更容易被更廣泛的行業和應用所接受。
8.鑽石銑刀技術的未來趨勢
金剛石塗層立铣刀的未來前景看好,目前的研發重點在於:
- 改善塗層附著力和均勻性
- 開發可增強效能的新型基板材料
- 擴大鑽石鍍膜工具的應用範圍
- 整合智慧型技術以進行工具磨損即時監控
9.總結
金剛石塗層立铣刀為精密加工領域帶來了革命性的變化,在廣泛的材料和應用領域中提供了無與倫比的性能。從 CVD 和 PVD 鍍層到石墨、鋁和塑膠專用刀具,這些尖端工具不斷突破現代製造的極限。隨著技術的進步和新應用的出現,金剛石塗層立铣刀毫無疑問將在塑造精密切削和銑削操作的未來中發揮關鍵作用。
無論您是要加工具有挑戰性的材料,或是要尋求最佳化的加工製程,探索金剛石塗層立铣刀的世界,都能為您製造業的效率、精確度和品質開啟新的可能性。透過瞭解這些先進工具的類型、應用和優點,您將能夠做出明智的決策,並在您的作業中充分發揮金剛石塗層立铣刀的潛力。