3 刃立铣刀
三刃立铣刀是一種多功能切削刀具,具有三個螺旋槽,專為高效排屑、冷卻液流動和結構完整性而設計。它在材料去除率和表面光潔度之間取得平衡,因此適用於各種材料,包括鋁和銅合金等軟性材料,以及硬度較高的鋼和其他金屬。常見的應用包括輪廓加工、開槽和開孔。

3 刃立铣刀應用
- 非鐵金屬材料: 鋁、銅和黃銅通常使用三刃立铣刀進行加工,因為它們能夠處理較高的進給率,並產生良好的表面光潔度。
- 一般銑削: 輪廓加工、開槽和切槽是使用三刃立铣刀進行的常見加工。
- 中等材料去除率: 雖然沒有 2 刃立铣刀的攻擊性,但卻能在排屑與表面光潔度之間取得平衡。
- 開槽: 三個溝槽可有效處理切槽作業中的切屑負荷。
- 倒角和去毛刺: 有些三刃立铣刀是專為這些應用而設計的。
3 刃立铣刀 特徵
- 三個螺旋楞: 這些均勻排列的刃口可有效地去除切屑、改善冷卻液流量,並提高刀具強度。
- 平衡晶片負載: 三個刃口均勻分散切削力,減少振動,提高刀具壽命。
- 良好的表面光潔度: 溝槽的幾何形狀通常會在工件上產生平滑的光潔度。
- 多功能性: 適用於各種材料和加工作業。
- 適中的材料去除率: 在強力切削與刀具壽命之間取得平衡。
- 可用的幾何形狀: 多種楞長度、螺旋角及直徑,以符合特定應用。
- 塗層選項: 通常鍍有TiN或TiAlN等材料,以提高耐磨性和性能。
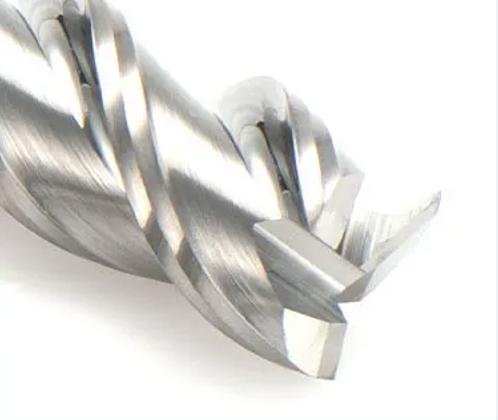
邊緣鈍化
三刃立铣刀具有三個間距均勻的螺旋刃,可有效排屑,提高刀具壽命和表面光潔度。藉由均勻分散切削力,可降低震動並改善整體性能。3 刃立铣刀的刃口幾何形狀設計可使切削刃平滑,提高加工工件的表面品質,同時延長刀具壽命。
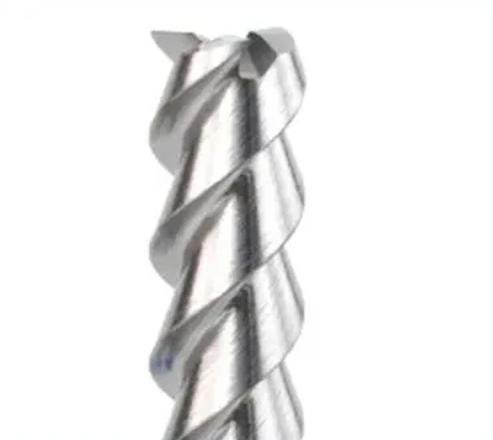
螺旋設計
3 刃立铣刀具有鋒利的切削刃,可有效地去除材料。其大型排屑槽可有效排出切屑,防止堵塞和刀具損壞。不沾鍍層可減少摩擦與發熱,提高刀具壽命與表面光潔度。這些特性使其成為各種加工應用的多用途選擇。
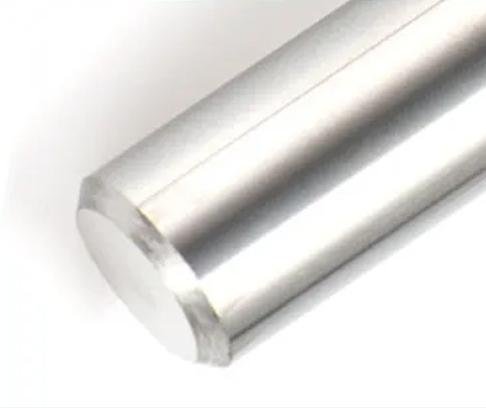
圓形把手倒角
3 刃立铣刀的刀柄上通常有一個萬向倒角,方便快速安全地安裝刀具。這種設計可防止夾持時滑動,確保最佳的性能和操作者的安全。倒角刀柄也有助於排屑,降低刀具破損的風險。
3 刃立铣刀目錄
3 刃立铣刀目錄是為廣泛使用者提供 3 刃立铣刀產品資訊的專業工具。
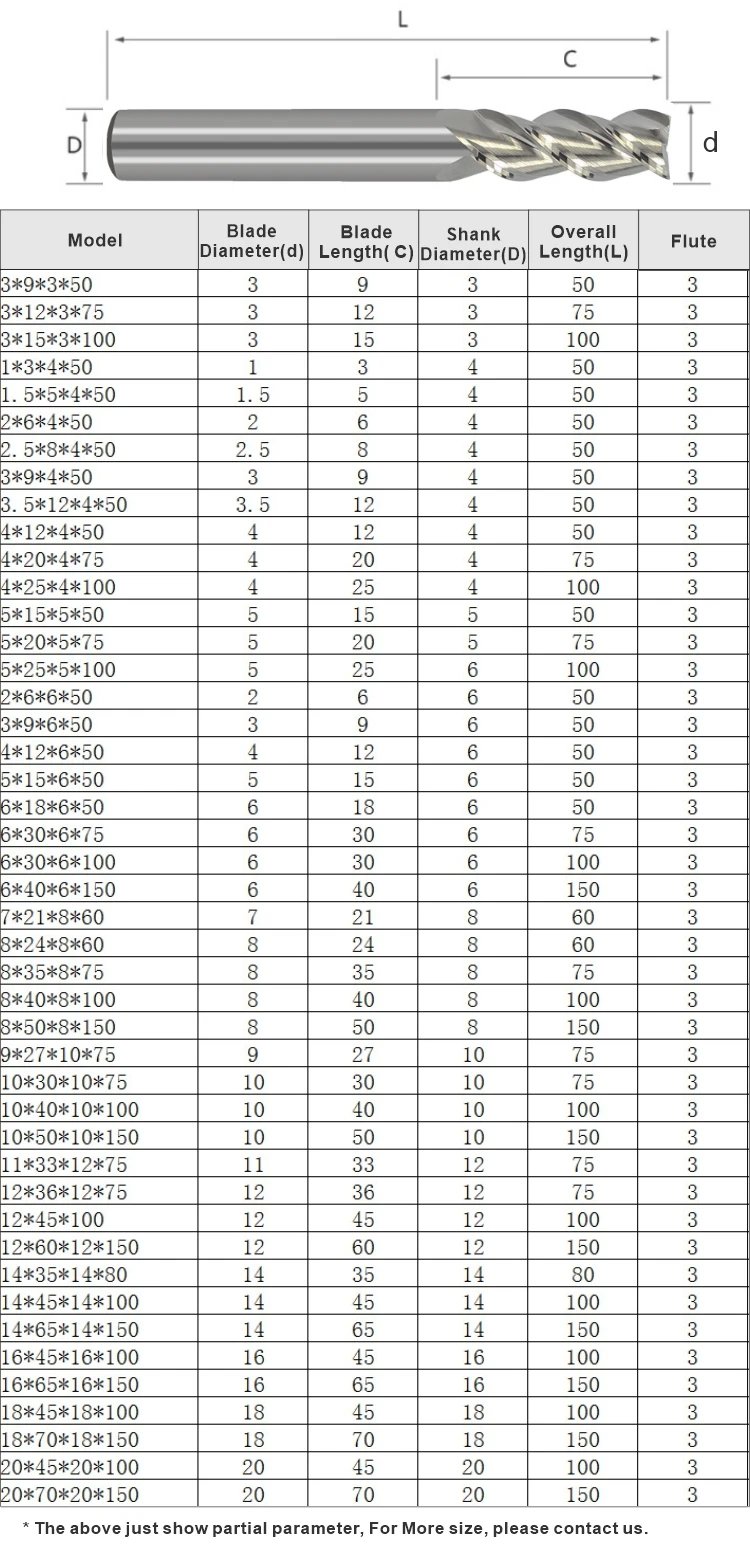
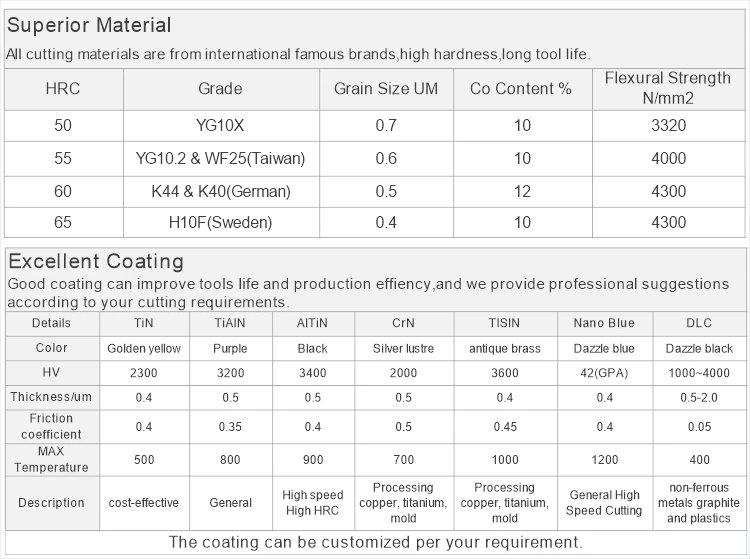
ONMY TOOLINGS 的與眾不同之處
是什麼讓我們的單刃立铣刀與眾不同?是我們獨特的組合:
先進的硬質合金配方
我們使用專有的微粒硬質合金混合物,優化了強度和耐磨性。
創新的幾何圖形
我們已取得專利的刃口設計,可最大限度地排出切屑,並將切削力降至最低。
尖端塗層
我們使用奈米層狀的 PVD 塗層,可增強耐熱性並減少摩擦。
精密研磨
我們的多軸 CNC 研磨機可達到 ±0.0005 英寸的公差。
不要只相信我們的話。以下是我們滿意的客戶所說的話:
我的快樂客戶
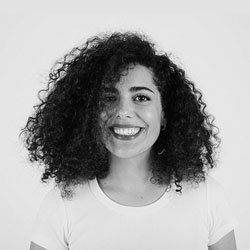
立即取得自訂報價!
P.S. 我們有提供大量訂購折扣嗎?訂購越多,節省越多!
- 無與倫比的原廠直銷價格:省去中間人,與零售價相比,最高可節省 40%。我們高效率的製造過程讓我們能以具競爭力的價格提供優質產品。
- 快速交貨:憑藉精簡的生產流程,我們提供領先業界的交貨時間。您可以在短短 7 天內收到訂製的立銑刀!我們有大量標準尺寸的庫存,可立即出貨。
- 個人化服務:我們的專業工程師團隊隨時準備幫助您找到完美的解決方案,以應對您獨特的加工挑戰。我們提供免費諮詢,分析您的特定需求,並建議理想的刀具規格。
常見問題
- 適用於較軟材料的粗加工: 三刃立铣刀可能是個不錯的選擇。
- 適用於精加工作業或較硬的材料: 通常建議使用 4 刃立铣刀
三刃立铣刀 具有與雙刃刀具相同的刃距,但強度更高。它們用途廣泛,適用於黑色和有色金屬材料。 四刃立铣刀 提供優異的強度,與三刃具相比,可達到更高的進給率。但是,它們的刃距較窄,因此切屑較小。
一般而言,在加工鋁材時,最好使用 2 刃立铣刀。
- 更大的芯片負載: 雙刃設計可產生更大的排屑空間,使排屑效果更佳,對於鋁材等軟性材料尤其重要,因為此類材料的切屑負荷可能很高。
- 更高的材料去除率: 更大的切屑載量可實現更快的切削速度和更高的進給率。
- 降低切削力: 較少的溝槽可降低切削力,這對鋁材加工非常有利。
雖然 3 刃立铣刀可用於鋁材,但往往更適合較硬的材料或需要較細緻的表面處理。
雖然 2 刃立铣刀因其優異的排屑能力,通常是鋁材加工的首選,但 3 刃立铣刀具有更多的通用性,在各種應用上都是不錯的選擇。最終,最佳的選擇取決於特定的加工條件和想要的結果。
三刃球頭立铣刀主要用於曲面的輪廓加工、仿形加工和精加工。 它的圓形尖端可在不同半徑之間平滑轉換,是製作複雜形狀的理想選擇。
三刃銑刀有助於平衡切屑負荷、良好的表面光潔度及整體刀具性能。透過選擇適當的硬質合金等級與幾何形狀,三刃硬質合金立铣刀可針對特定加工條件進行最佳化。
3 刃粗加工立铣刀主要用於快速有效地去除大量材料。 雖然不如 2 刃粗加工立铣刀那樣強力,但它在材料去除率和刀具壽命之間取得了平衡。
主要應用包括
- 快速材料移除: 在完成作業前清除多餘的材料。
- 半精加工: 達到比粗加工更平滑的表面,但在最終精加工之前。
- 一般銑削: 適用於各種材料的各種粗加工任務。