In the world of precision manufacturing, CNC (Computer Numerical Control) machining plays a crucial role in producing high-quality parts with exceptional accuracy. At the heart of this process are CNC inserts, the cutting tools that directly impact machining efficiency and output quality. For many manufacturers and machine shops, understanding and optimizing CNC insert prices is essential for maintaining competitiveness and profitability.
The Importance of CNC Insert Selection
Before delving into the intricacies of CNC insert pricing, it’s crucial to understand why these small components are so vital to the machining process. CNC inserts are the cutting edges that perform the actual material removal in turning, milling, and other machining operations. They directly influence:
- Machining speed and efficiency
- Surface finish quality
- Tool life and replacement frequency
- Overall production costs
Given their significance, selecting the right inserts at the right price point is a critical decision for any machining operation.
Factors Influencing CNC Insert Prices
Several key factors contribute to the wide range of CNC insert prices in the market:
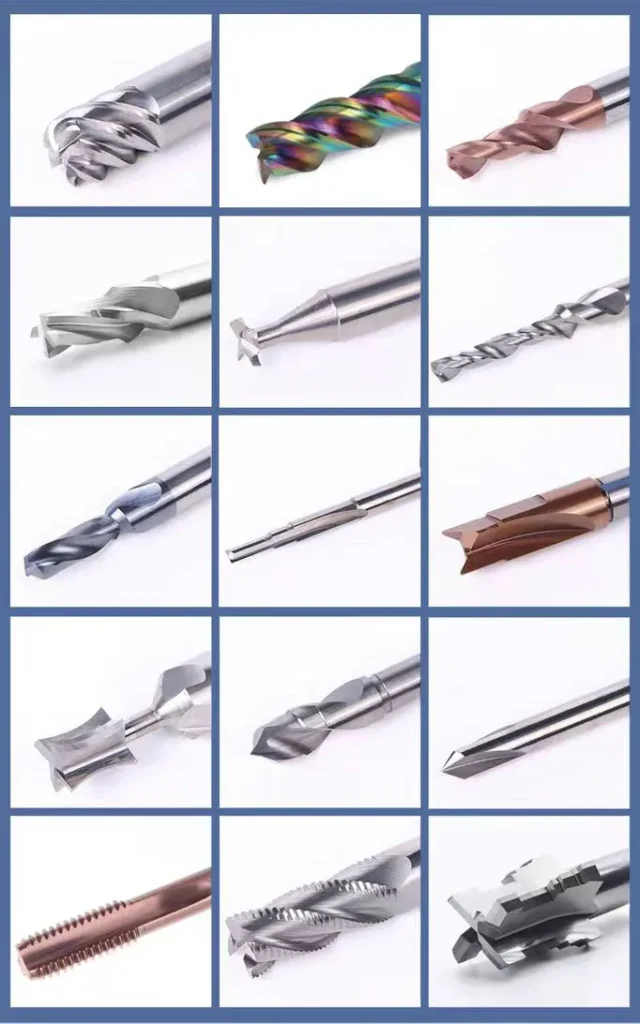
1. Material Composition
The base material of a CNC insert significantly impacts its price. Common materials include:
- Carbide: The most widely used material, offering a good balance of hardness and toughness.
- Ceramic: Harder than carbide but more brittle, suitable for high-speed machining of hard materials.
- Cubic Boron Nitride (CBN): Extremely hard, used for machining hardened steels and cast irons.
- Polycrystalline Diamond (PCD): The hardest insert material, ideal for non-ferrous metals and composites.
Generally, کاربائڈ داخل کرتا ہے are the most affordable, while PCD inserts command premium prices due to their superior hardness and wear resistance.
2. Coating Technology
Many CNC inserts feature advanced coatings to enhance performance and longevity. Common coating types include:
- Titanium Nitride (TiN)
- Titanium Carbonitride (TiCN)
- Titanium Aluminum Nitride (TiAlN)
- Diamond-Like Carbon (DLC)
Coated inserts typically cost more than uncoated ones but often provide better wear resistance and longer tool life, potentially offering better value in the long run.
3. Geometry and Design
The complexity of an insert’s geometry can significantly impact its price. Inserts with specialized chip-breaker designs or unique cutting edge preparations may cost more but can improve machining efficiency and surface finish quality.
4. Brand and Quality
As with many industrial products, brand reputation plays a role in CNC insert pricing. Well-known manufacturers may charge premium prices for their products, often justifying the cost with superior quality control, consistency, and performance guarantees.
5. Quantity and Packaging
Purchasing inserts in larger quantities typically results in lower per-unit prices. Additionally, some manufacturers offer economical packaging options for bulk buyers.
Strategies for Optimizing CNC Insert Costs
While the CNC insert price is an important consideration, it shouldn’t be the sole factor in your decision-making process. Here are some strategies to optimize your insert costs while maintaining machining quality:
1. Conduct Thorough Application Analysis
Before selecting an insert, carefully analyze your specific machining requirements. Consider factors such as:
- Workpiece material
- Cutting parameters (speed, feed, depth of cut)
- Surface finish requirements
- Production volume
This analysis will help you choose the most appropriate insert type and grade, potentially saving money by avoiding over-specification.
2. Calculate Total Cost of Ownership
Instead of focusing solely on the upfront CNC insert price, consider the total cost of ownership. This includes factors such as:
- Tool life
- Machining time
- Scrap rates
- Machine downtime for tool changes
A more expensive insert that lasts longer or allows for higher cutting speeds may prove more economical in the long run.
3. Explore Different Suppliers
Don’t limit yourself to a single supplier. Research and compare offerings from multiple manufacturers and distributors. Some lesser-known brands may offer comparable quality at lower prices.
4. Optimize Inventory Management
Implement an efficient inventory management system to avoid overstocking expensive inserts or facing production delays due to stockouts. Just-in-time ordering can help balance inventory costs with production needs.
5. Consider Regrinding Services
For certain insert types, regrinding services can extend tool life and reduce overall costs. While not all inserts are suitable for regrinding, it’s worth exploring this option for high-value or specialized inserts.
6. Invest in Training and Process Optimization
Proper insert selection, setup, and use can significantly impact tool life and performance. Invest in operator training to ensure your team is maximizing the potential of your CNC inserts, regardless of their price point.
7. Leverage Technology for Insert Management
Implement tool management software to track insert usage, performance, and costs across your operation. This data can provide valuable insights for future purchasing decisions and process improvements.
The Future of CNC Insert Pricing
As manufacturing technology continues to evolve, several trends are likely to impact CNC insert prices in the coming years:
- Advanced Materials: Development of new, high-performance insert materials may lead to higher upfront costs but potentially lower long-term expenses due to improved durability and performance.
- Additive Manufacturing: 3D printing technologies may enable the production of more complex insert geometries, potentially affecting pricing structures.
- Sustainability Concerns: Growing emphasis on sustainable manufacturing practices may influence insert designs and materials, potentially impacting prices.
- Digital Integration: Smart inserts with embedded sensors for wear monitoring and predictive maintenance may command premium prices but offer enhanced performance and cost savings over time.
Conclusion
Navigating the world of CNC insert prices requires a balanced approach that considers both immediate costs and long-term value. By understanding the factors that influence insert pricing and implementing strategic cost optimization techniques, manufacturers can make informed decisions that enhance their machining operations’ efficiency and profitability.
Remember that the lowest-priced insert isn’t always the most economical choice in the long run. Instead, focus on finding the optimal balance between CNC insert price, performance, and longevity for your specific applications. By taking a holistic view of your machining processes and continuously evaluating your insert choices, you can stay competitive in an ever-evolving manufacturing landscape.
Ultimately, the goal is to find CNC inserts that deliver the best value for your operation, enabling you to produce high-quality parts efficiently and cost-effectively. With careful consideration and strategic decision-making, you can optimize your CNC insert investments and drive success in your machining endeavors.