A 銑削刀片 is a cutting tool that is used to perform metal machining on a milling machine. It is usually made of HSS, carbide, or ceramic materials and comes in various shapes to suit different machining needs. A milling insert consists of two parts: the tool holder and the insert.
What you will know about milling inserts
- The shape of milling inserts
- Types of milling
- Material of milling inserts
- Application scenarios of milling inserts
If you want to know more about choosing milling inserts, please continue reading below.
Types of milling

boring milling

helical milling
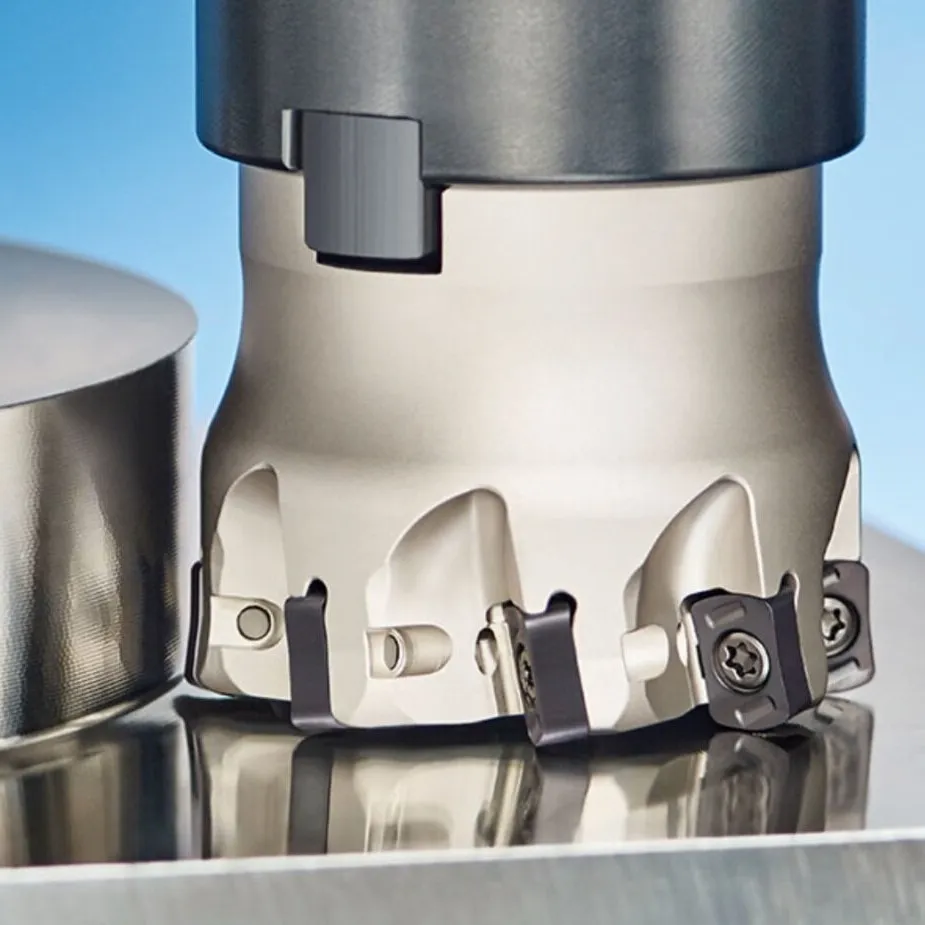
high feed milling

face milling
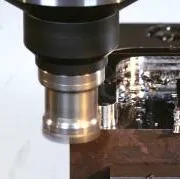
square shoulder milling
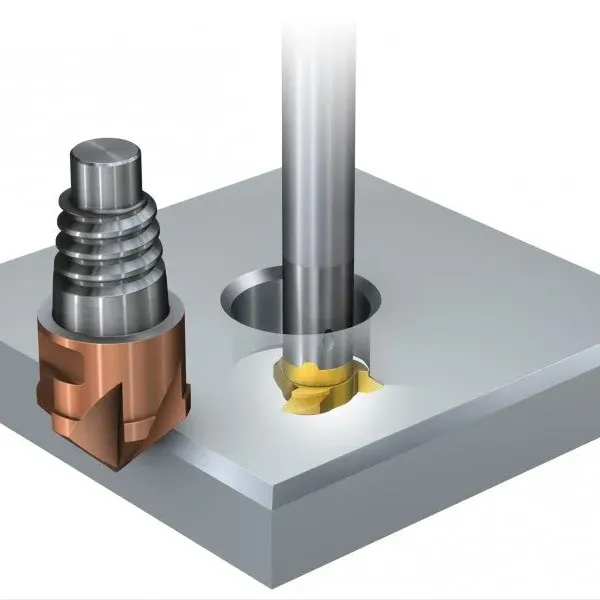
chamfer milling
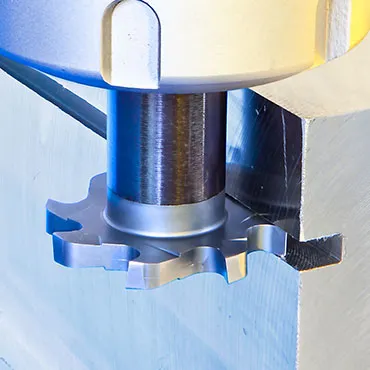
T-slot milling

side and face milling
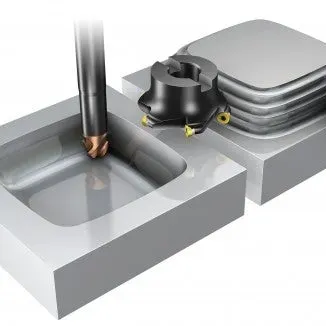
profile milling
What is a milling insert?
In this paragraph, you will first know what is milling and then what is milling insert.
Milling is the manufacturing of metal products using inserts to remove material from a workpiece. The variety of shapes and sizes determines the cutting or removal of these materials from the object. This is why the quality of inserts is as important to the machinery as well as the workpiece.
Indexable inserts offer a significant advantage compared to other cutting tools: If a cutting edge of the indexable insert is worn, it is simply turned to an unused cutting edge – no need for regrinding. This ensures that ongoing production is only interrupted briefly and there is no need for a time-consuming setup of the tool.
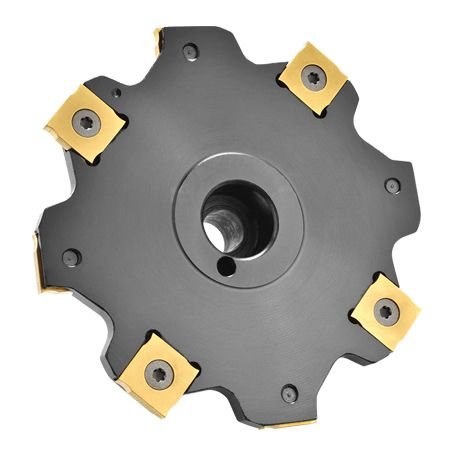
How to classify the milling insert?
There are many ways to classify milling inserts, and we will distinguish the types of milling inserts in this paragraph by their function. Of course, if you want to know other classification methods, you can also communicate with us.
銑削刀片 can also be classified according to different characteristics such as cutting method, tool shape, tool material, and coating.

Here are some types:
End milling cutter
An end milling cutter is a common rotary cutting tool that is usually used for milling work on machine tools. Its main feature is a rotatable cutting blade, with a straight shank design that is easy to replace and adjust the blade position. Generally suitable for processing flat surfaces, chamfers, and grooves.
Face milling cutter
A face milling cutter is a rotating tool suitable for processing large-area flat surfaces. Its characteristic is that the plate-shaped blade can rotate, and the machine body structure is strong, and suitable for a wide range of applications.
Gear milling cutter
The gear milling cutter is used to process straight teeth, helical teeth, or involute teeth. The blade is chain-shaped, and there are two common types: cylindrical and conical.
Spiral milling cutter
A spiral milling cutter is a special cutting tool for processing spiral lines, which can be used in milling, forming, and grinding processes. The main feature is that the blade rotates in a spiral shape to speed up cutting and improve efficiency.
Ball milling cutter
The shape of the ball milling cutter is spherical, mainly suitable for processing three-dimensional surfaces and spherical surfaces, with the advantages of high processing quality and stable cutting.
High-efficiency milling cutter
High-efficiency milling cutters have made breakthroughs in material selection, tool shape design, tool coating, etc., which can achieve high-speed and high-efficiency processing. They are widely used in fields such as automobiles, electronics, and aerospace with high-speed processing requirements.
Milling insert identification
In this paragraph, you will know exactly what types of rotary milling inserts comply with the ISO international standard. You will find data about insert size, shape, thickness, angle, etc. in the illustrations.

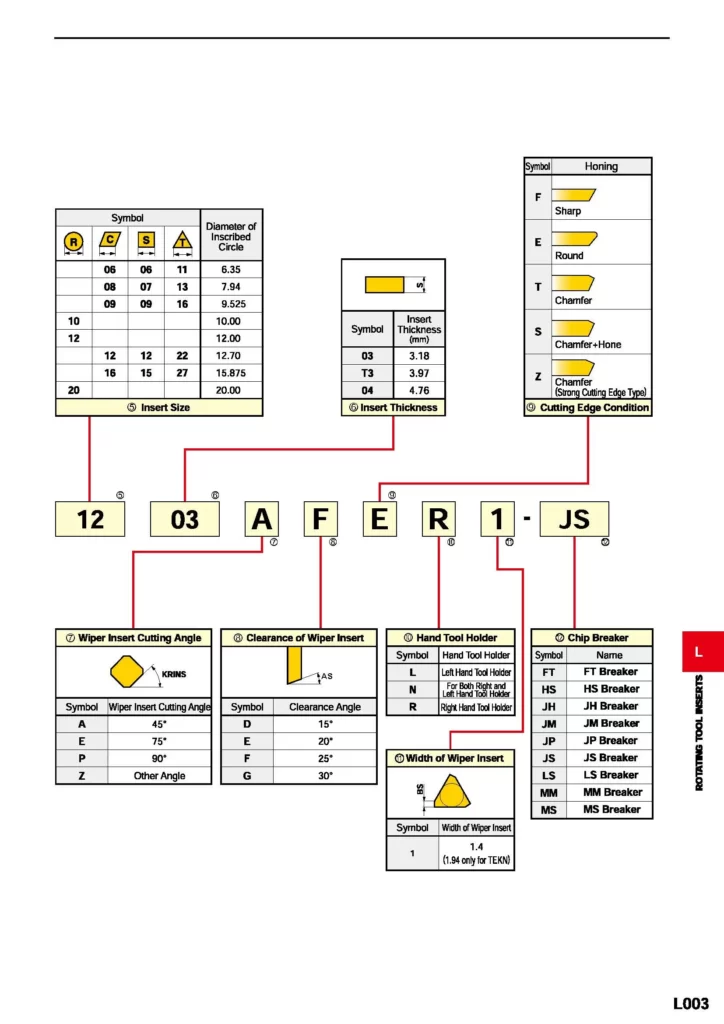
(Image quoted from Mitsubishi)
Material and performance of milling inserts
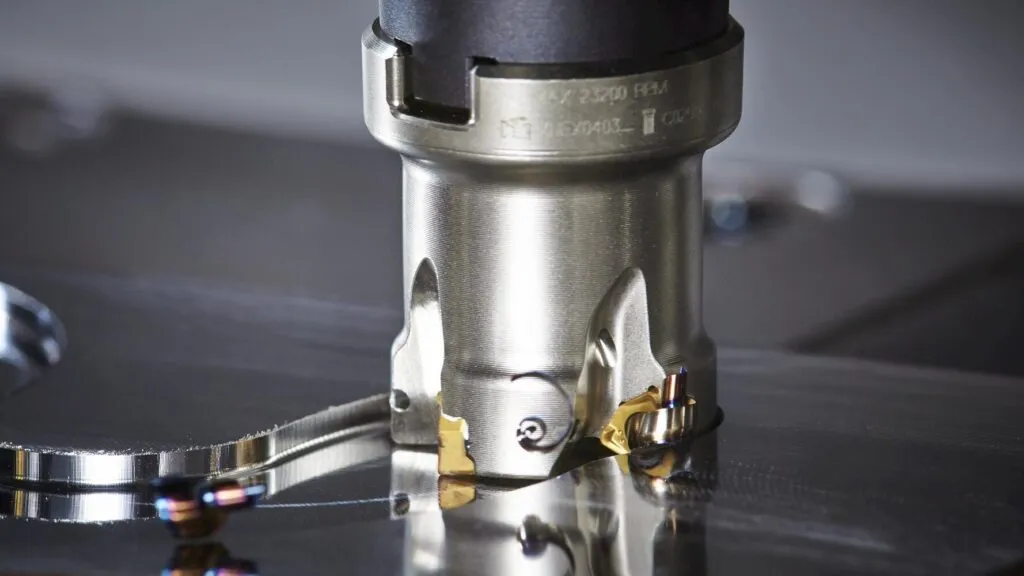
Different insert materials and coatings have different ranges of applications and cutting performances for different milling operations.
- High-Speed Steel milling inserts (HSS): An affordable milling insert material for machining softer metals such as aluminum, copper, cast iron, and mild steel.
- Carbide Milling Inserts (Carbide): Carbide milling inserts made of tungsten cobalt alloy, typically used for machining high-hardness materials such as bronze, stainless steel, and alloys.
- Ceramic milling inserts (Ceramic): This milling insert material is made of impregnated ceramic and therefore has high hardness and wear properties. Ceramic milling inserts have excellent cutting performance for high-hardness materials, high-speed machining, and vibration reduction, but they are also prone to tool breakage.
- PCD milling insert: It is made of synthetic diamond powder with high hardness and excellent wear resistance. It is used for processing soft and non-metallic materials such as aluminum and copper.
Milling inserts can also be coated to enhance their wear resistance, and corrosion resistance, reduce surface adhesion, and improve thermal stability. Common coatings include PVD coatings, CVD coatings, and edge front coatings.
The effect of cutting parameters on the life and performance of milling inserts
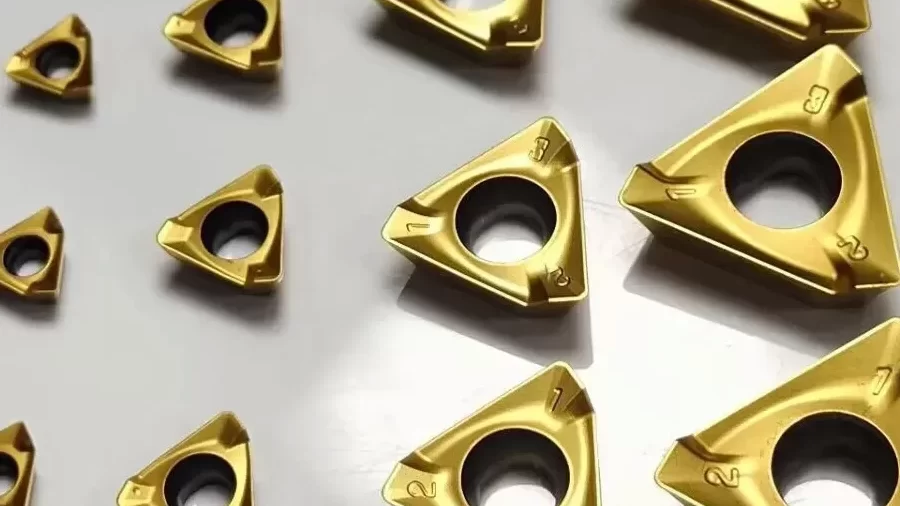
I would say that the cutting parameters are the most difficult to set. But it has a very big impact on the machining, and the good thing is that we now have milling calculation formulas to use, very easy to calculate the data you need.
- Cutting speed: too high a cutting speed will lead to excessive frictional heat of the milling cutter blade, which will intensify tool wear and may even cause the tip to scratch the surface of the workpiece, affecting the accuracy and surface quality of the workpiece; while too low a cutting speed will lead to milling difficulties, increased cutting force, difficult chip discharge and other problems.
- Feed: too much feed will lead to excessive tool load and increased wear; while too little feed may result in insufficient milling force, slow feed, low cutting efficiency, and other problems.
- Cutting depth: too much cutting depth will lead to an increase in the cutting force on the milling cutter blade, which will easily wear and even break, while too little cutting depth may lead to an increase in working time and lower productivity.
- Cutting fluid: the use of appropriate cutting fluid can effectively protect the milling cutter blade, and reduce the risk of tool wear and fracture, while the surface quality of the workpiece also has a better protection role.
In summary, the selection of cutting parameters should be considered with the workpiece material, milling cutter blade material, milling accuracy, work efficiency, and other factors, and be reasonably adjusted to achieve the best milling effect and tool life.
Tips for choosing to mill insert
Finally, finally, I’ll give you some small tips for choosing the right rotary milling cutter insert(This is the summary of our experts after many years)
Select indexable insert geometry according to the workpiece to be machined
For roughing, we recommend a combination of large depths of cut and high feed rates. Roughing applications place high demands on the reliability of the cutting edge.
For finishing applications, low cutting forces are required, as shallow depths of cut and low feeds are usually needed.
Choose the largest possible point angle
Large point angle advantage: stable, large feed rate, high efficiency.
Large point angle disadvantage: high vibration
Small point angle advantage: Reduction of surface burrs, reduced cutting force
Small point angle disadvantage: Untimely chip removal, lower cutting efficiency
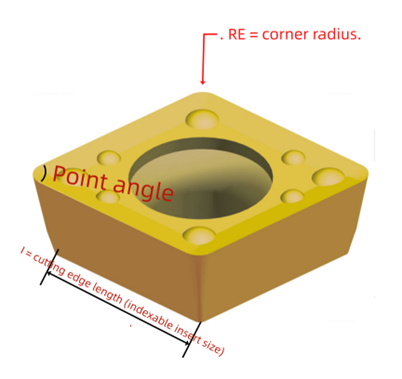
Choose an indexable insert size based on the depth of cut
Determine the maximum depth of cut, then set the desired cutting length, taking into account the mounting angle of the tool holder. You can then select the correct cutting edge length for the insert.
Choose the correct mounting angle
a. 0-degree mounting: Inserts are mounted along the milling centerline and are best suited for milling flat surfaces. If other types of milling are required, the mounting angle may need to be changed.
b. Slightly negative angle mounting: When milling thin-walled parts, the negative angle helps reduce vibration and tool runout. However, negative angles can increase cutting forces and wear and can result in a lower-quality milled surface.
c. Slightly positive angle mounting: Positive angles help improve tool rigidity and stability, reduce tool loading, and thus extend tool life. However, positive angles deteriorate surface roughness and increase cutting forces.
d. Large angle mounting: When used for milling harder materials, a large angle produces less cutting force and higher surface quality, but less efficient machining.
Choose the right cutting material and coating
Choosing the correct material and coating for the milling cutter blade is important because the choice of material and coating can have a direct impact on the milling cutting ability, cutting life, and surface quality.
a.Material selection: The commonly used materials for milling cutter blades are HSS, carbide, ceramic, etc. Generally speaking, the main disadvantages of carbide tools are fragmentation and brittleness, while the main problem of milling cutter blades made of HSS is wear and tear.
b.Coating selection: The popular milling cutter coatings on the market now are titanium nitride, tungsten carbide, aluminum nitride, etc. The role of the coating is to improve the hardness of the cutting edge, anti-wear, and reduce the friction coefficient, thus extending the cutting life. Depending on the machining conditions, different coatings can be selected. For example, for milling difficult-to-cut materials such as high-temperature alloys, choosing aluminum oxide coating can get better results; for the case of high surface finish of the workpiece, choosing titanium coating can get better surface quality and life.
Choosing the right material and coating for milling cutter blades can improve the cutting performance and machining efficiency of the tool, while also extending the service life of the cutting tool. However, different tool materials are suitable for different machining conditions and workpiece materials and need to be selected with the actual machining situation.
FAQ:
How about feeds and speeds?
A.Feeds and speeds are a whole different beast in itself. Contact your tool rep and if you have multiple tool reps… have them send you their catalogs which will give you good starting feeds and speeds. Always think about the ISO material group you are milling, and take your endmill’s coating into consideration. For example, if you are milling aluminum, don’t mill it with an endmill that uses an aluminum coating! Otherwise, it could end up welding to your cutter
Can you please elaborate on how to select a clearance angle?
The marks on the side of the blade holder are reference points for clearance angle. This is the angle between the front face of the block and the one side of the bevel triangle that is facing the block. Normally, this bevel angle should be between 3-8 degrees