In the world of precision machining, efficiency and accuracy are paramount. Enter the تبدیل کرنے والا ٹپ ڈرل, a game-changing tool that’s reshaping the landscape of drilling operations across industries. This innovative design combines the best of both worlds: the performance of a solid drill with the versatility and cost-effectiveness of indexable inserts.
It’s widely accepted that drilling is the most frequently performed process in machining, whether on machining centers, CNC lathes, or dedicated drilling machines. When selecting the right drill and process, key considerations include cost-per-hole, hole quality, and hole completion. Replaceable tip drills have emerged as an extremely productive, accurate, and economical option for drilling, offering flexibility and optimum performance across multiple materials and applications.
In this comprehensive guide, we’ll delve into the world of replaceable tip drills, exploring their features, benefits, and applications that are making them an indispensable part of modern machining processes.

Understanding Replaceable Tip Drills
Replaceable tip drills, also known as exchangeable tip drills or modular drills, are cutting tools designed with interchangeable cutting tips. Unlike traditional solid drills, these tools feature a steel body with a separate, replaceable carbide insert at the cutting end. This design allows for quick and easy replacement of worn cutting edges without the need to replace the entire drill body.
The key components of a replaceable tip drill include:
- Drill body: The main shaft of the tool, typically made of high-strength steel
- Insert seat: A precisely engineered pocket at the tool’s tip to hold the cutting insert
- Cutting insert: A removable carbide tip that performs the actual cutting
- Clamping mechanism: A system to securely hold the insert in place
The advantages of replaceable tip drills over traditional solid drills are numerous:
- Reduced tooling costs: Only the insert needs replacement, not the entire drill
- Improved productivity: Quick insert changes mean less downtime
- Consistent performance: New cutting edges with each insert change
- Flexibility: One drill body can accommodate various insert geometries for different applications
Types of Replaceable Tip Drills
Replaceable tip drills come in various configurations to suit different machining needs:
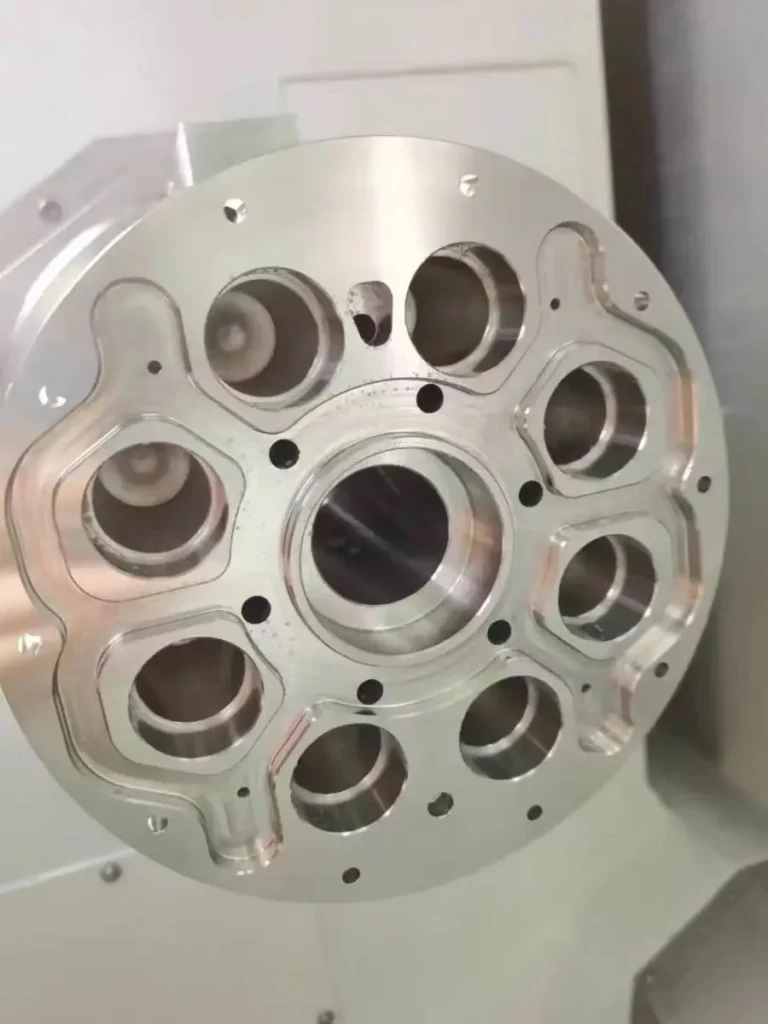
Single-flute designs:
- Ideal for deep hole drilling
- Excellent chip evacuation in challenging materials
- Often used in aerospace and automotive applications
Double-flute designs:
- Balanced cutting forces for improved hole quality
- Suitable for a wide range of materials and applications
- Common in general machining operations
Multi-flute options:
- Designed for high-speed drilling in stable conditions
- Provide superior hole finish and straightness
- Often used in mass production environments
Key Features of Replaceable Tip Drills
Cutting geometry:
Replaceable tip drills feature advanced cutting geometries optimized for specific materials and applications. These geometries are designed to:
- Enhance chip formation and evacuation
- Reduce cutting forces and heat generation
- Improve hole quality and surface finish
Insert materials:
The cutting inserts used in replaceable tip drills are typically made from advanced carbide grades, often with specialized coatings. These materials offer:
- Extended tool life
- Improved wear resistance
- Better performance at high cutting speeds
Coolant delivery systems:
Many replaceable tip drills incorporate sophisticated coolant channels that deliver cutting fluid directly to the cutting edge. This feature:
- Enhances chip evacuation
- Reduces heat buildup
- Extends insert life
Tool Holders and Drill Tips
Tool Holders:
Tool holders for replaceable tip drills are offered in numerous diameter-to-depth ratios, including:
- 1.5xD
- 3xD
- 5xD
- 7xD
- 10xD
- 12xD
Holder designs come in both straight and helical fluted options. They are typically available in:
- Imperial and metric shanks
- Cylindrical and flanged with a flat designs
Drill Tips:
Drill tips can vary based on substrate, coatings, and geometry depending on the application for which they are designed:
- Steel materials geometry: Designed to provide increased penetration and excellent chip control, ideal for low and medium carbon and alloy steels.
- Iron and cast geometry: Includes a corner radius for improved hole finish and heat dispersion, designed for cast and nodular iron applications.
- Multi-purpose geometry: Designed for softer materials, including aluminum, brass, and copper applications, yielding excellent chip control.
Applications of Replaceable Tip Drills
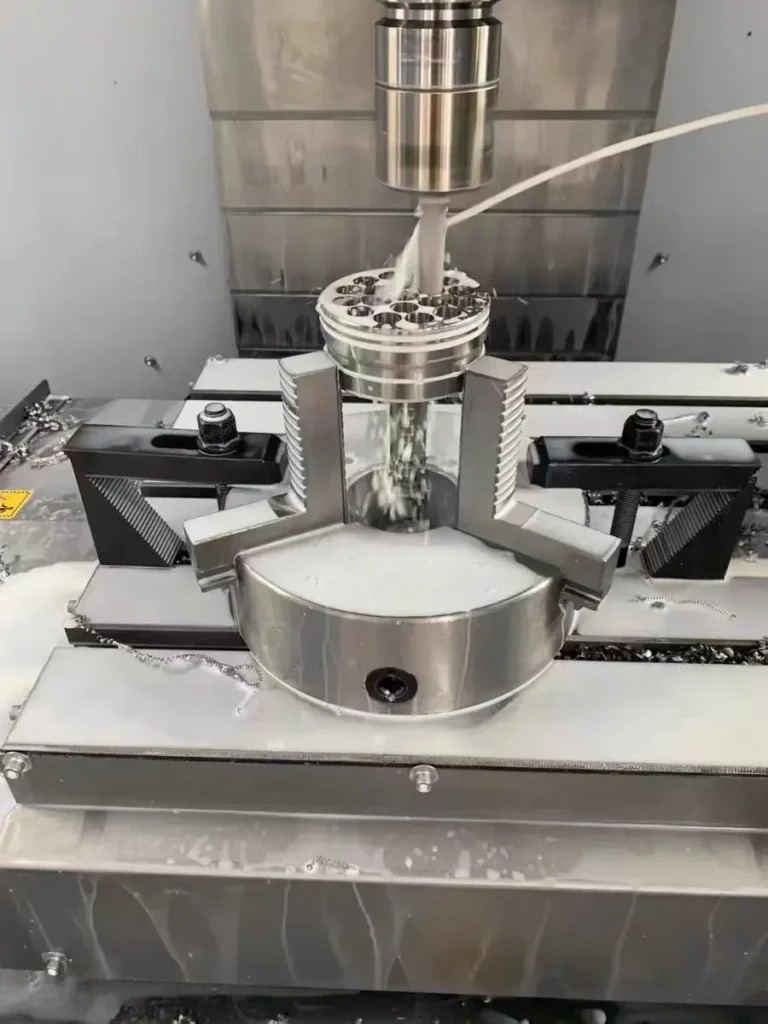
Industries that benefit from replaceable tip drills include:
- Aerospace: For drilling tough alloys in engine components and structural parts
- Automotive: High-volume production of engine blocks, transmission cases, and chassis components
- Oil and gas: Drilling of complex parts for exploration and production equipment
- General machining: Versatile use across various materials and applications
Common materials drilled with replaceable tip drills:
- Steel alloys
- Stainless steel
- Cast iron
- Aluminum alloys
- Titanium
- Exotic alloys like Inconel and Hastelloy
Expanded Applications: While replaceable-tip drills have been popular for their cost savings, they were initially limited to certain applications. However, advances in coatings and geometries, as well as improvements in machine tools, have led to increased applications for replaceable-tip drills. This expansion has made them suitable for a wider range of materials and machining conditions.
Selecting the Right Replaceable Tip Drill
Choosing the appropriate replaceable tip drill involves considering several factors:
- Hole diameter and depth
- Material to be drilled
- Required surface finish and tolerance
- Production volume
- Machine tool capabilities
Matching inserts to applications is crucial for optimal performance. Consider:
- Insert geometry: Different geometries are optimized for specific materials and cutting conditions
- Coating type: Select coatings that enhance wear resistance and reduce friction for the target material
- Grade: Choose carbide grades that balance hardness and toughness for the application
Best Practices for Using Replaceable Tip Drills
Setup and installation:
- Ensure proper alignment and minimal runout when mounting the drill
- Verify that the insert is correctly seated and securely clamped
- Check coolant flow and pressure before starting the operation
Cutting parameters:
- Follow manufacturer recommendations for cutting speed, feed rate, and depth of cut
- Adjust parameters based on material properties and desired hole quality
- Monitor chip formation and adjust as needed for optimal performance
Maintenance and care:
- Regularly inspect inserts for wear and damage
- Clean the insert seat thoroughly when changing inserts
- Store drills and inserts in a clean, dry environment to prevent corrosion
Cost-Effectiveness of Replaceable Tip Drills
While the initial investment in replaceable tip drills may be higher than traditional solid drills, the long-term savings are significant:
- Reduced tooling costs: Only inserts need replacement, not entire drills
- Decreased downtime: Quick insert changes improve productivity
- Inventory simplification: Fewer drill bodies needed, with inserts providing versatility
Productivity improvements:
- Consistent performance throughout insert life
- Higher cutting speeds and feed rates possible with advanced insert materials
- Reduced setup time for different drilling operations
To Regrind or Not? One of the key benefits of modular drills is that users can choose to eliminate the regrinding of worn tools. While some shops still choose to regrind replaceable tips to extend overall tool life, omitting that process increases the tools’ financial viability by:
- Reducing the cost-per-part
- Eliminating the need to ship worn drills to a re-sharpener
However, if regrinding is needed, some tool manufacturers offer this service to extend the life of your replaceable tips.
Preserving Body Life:
Another advantage of replaceable-tip drills is using one tool body for an extended period. While the concept of buying one drill body and an infinite number of heads is appealing, it’s important to note that wear and tear on the drill body eventually take their toll. Regular inspection and maintenance of the tool body are essential to ensure optimal performance and longevity.
Future Trends in Replaceable Tip Drill Technology
The future of replaceable tip drills looks promising, with ongoing advancements in:

Insert materials:
- Development of new carbide grades with improved wear resistance
- Advanced coatings for enhanced performance in challenging materials
- Nano-structured materials for increased toughness and heat resistance
Smart drilling systems:
- Integration of sensors for real-time monitoring of cutting conditions
- Adaptive control systems to optimize drilling parameters on-the-fly
- Predictive maintenance capabilities to schedule insert changes proactively
Conclusion
Replaceable tip drills have revolutionized the world of precision machining, offering a perfect blend of performance, versatility, and cost-effectiveness. As we’ve explored in this guide, these innovative tools provide numerous benefits, from reduced tooling costs to improved productivity and consistent hole quality.
The future of replaceable tip drills looks bright, with ongoing advancements in materials science and smart manufacturing technologies promising even greater capabilities. As industries continue to demand higher precision, faster production, and more cost-effective solutions, replaceable tip drills will undoubtedly play a crucial role in meeting these challenges.
Whether you’re a seasoned machinist or new to the world of drilling operations, embracing replaceable tip drill technology can significantly enhance your machining capabilities. By understanding the features, applications, and best practices outlined in this guide, you’ll be well-equipped to harness the full potential of these game-changing tools in your operations.