機械加工の世界では、最適な結果を得るために、作業に適した工具を選択することが重要です。 エンドミル エンドミルは、フライス加工に使用される汎用性の高い切削工具であり、機械加工者が直面する最も重要な決断の1つは、異なるフルート構成を選択することです。この記事では、2枚刃エンドミルと4枚刃エンドミルの比較に焦点を当て、それぞれの特徴、用途、性能に影響を与える要因についてご紹介します。
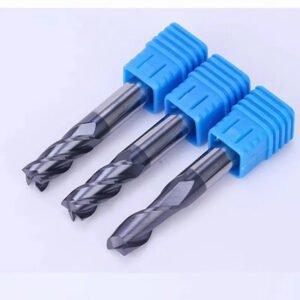
エンドミルのフルートについて
2枚刃エンドミルと4枚刃エンドミルの比較に入る前に、フルートとは何か、フルートが切削性能にどのような影響を与えるかを理解することが重要です。フルートとは、エンドミルの長さ方向に走る深いらせん状の溝のことです。この溝の主な目的は2つあり、切れ刃を作ることと、切削中に切り屑を排出する溝を作ることです。
フルートの数 エンドミル は、様々な用途での性能に大きな影響を与えます。一般的に、エンドミルには2枚刃から8枚刃まであり、2枚刃と4枚刃の構成が最も一般的です。
2枚刃エンドミル
特徴
2枚刃エンドミルは、大きなフルートスペースと鋭い切れ刃が特徴です。この設計により、効率的な切り屑排出と切削抵抗の低減が可能になります。

メリット
- 優れたチップクリアランス
- より低い切断力
- 柔らかい素材に最適
- プランジ加工に最適
デメリット
- 用途によっては安定性に欠ける
- 素材によっては粗い仕上がりになる場合がある。
2枚刃エンドミルは何に使うのですか?
2枚刃エンドミルは主に次の用途に使用される:
- アルミニウム、真鍮、プラスチックなどの柔らかい材料の切断
- 深い溝やポケットを必要とするフライス加工
- チップ避難が重要なオペレーション
- プランジ切断および穴あけ作業
4枚刃エンドミル
特徴
フルート4本 エンドミル は、2枚刃に比べ切れ刃が多く、フルートスペースが小さい。この構成により、多くの用途で安定性が向上し、仕上げ面が改善されます。

メリット
- 切断時の安定性が向上
- 表面仕上げの向上
- より高い送り速度が可能
- より硬い素材に適している
デメリット
- チップクリアランスの減少
- より高い切断力
- プランジ加工の効率が悪い
4枚刃エンドミルは何に使うのですか?
4枚刃エンドミルは、一般的に次のような用途に使用される:
- 鋼やステンレス鋼のような硬い材料の切断
- 表面品質が重要な仕上げ作業
- 側面フライス加工とプロファイル加工
- 高い送り速度を必要とする用途
2枚刃と4枚刃エンドミルの比較
2枚刃エンドミルと4枚刃エンドミルの選択は、いくつかの要因によって決まります。主な違いを見てみましょう:
- 切削効率: 一般的に2枚刃エンドミルは、切り屑の負荷が大きく、切り屑の排出性が向上するため、軟らかい被削材での切削効率が良くなります。しかし、4枚刃エンドミルは、切削力がより多くの刃に分散されるため、より硬い被削材では、より高い切削効率を発揮します。
- 材料除去率:多くの場合、2枚刃エンドミルは、特に軟らかい被削材で高い材料除去率を達成できます。これは、より深い切削が可能で、より大きな切りくずを処理できるためです。しかし、4枚刃エンドミルは、より高い送り速度を使用できるため、より硬い被削材で高い切り屑処理率を達成できる場合があります。
- 表面仕上げ: 4枚刃エンドミルは、一般的に2枚刃エンドミルに比べて表面仕上げが良好です。切れ刃が追加されることで、加工物が均等に分散され、より滑らかな仕上げ面が得られます。そのため、4枚刃エンドミルは仕上げ加工に適しています。
- 放熱性: 2枚刃エンドミルは、一般的にフルートスペースが広いため、放熱性に優れています。これは、熱に敏感な材料を扱う場合や、冷却が制限される用途で特に有益です。
- 工具寿命:エンドミルの工具寿命は、被削材や切削条件など様々な要因によって異なります。一般的に、4枚刃エンドミルは、硬い被削材を切削する場合、摩耗がより多くの切れ刃に分散されるため、工具寿命が長くなる可能性があります。しかし、2枚刃のエンドミルは、軟らかい被削材を切削する場合、発熱が少なく、切削抵抗が小さいため、工具寿命が長くなる可能性があります。

専門的な比較
より包括的に理解するために、他のフルートの構成を簡単に比較してみよう:
- 2枚刃と3枚刃エンドミルの比較3枚刃エンドミルは、2枚刃ミルの切り屑排出性と4枚刃ミルの安定性のバランスがとれています。アルミなどの被削材によく使用され、良好な切り屑処理性を維持しながら、2枚刃ミルに比べて仕上げ品質を向上させることができます。
- 2枚刃エンドミルと3枚刃エンドミルの比較アルミニウムを加工する場合、2枚刃エンドミルと3枚刃エンドミルの両方が有効です。2枚刃エンドミルは、切りくず排出性に優れ、深いポケット加工に最適です。3枚刃エンドミルは、切り屑排出性と仕上げ面のバランスが良く、幅広いアルミ加工に適しています。
- 2枚刃と3枚刃の比較木材加工では、切りくず排出性に優れる2枚刃エンドミルが一般的に好まれます。しかし、3枚刃エンドミルは、木材の種類によっては、より滑らかな仕上げが可能で、人工木材製品を加工する場合に有益です。
- 2枚刃と4枚刃のボールノーズエンドミルボールノーズエンドミルは、3次元輪郭加工や仕上げ加工に使用されます。2枚刃ボールノーズエンドミルは、柔らかい被削材や切り屑排出が重要な場合に適しています。4枚刃ボールノーズエンドミルは、仕上げ面精度が向上し、硬い被削材や仕上げ加工に適しています。
- 3枚刃と4枚刃のエンドミル3枚刃エンドミルと4枚刃エンドミルのどちらを選択するかは、多くの場合、特定の被削材と用途によって決まります。3枚刃エンドミルは、切り屑排出性と安定性のバランスが良く、様々な被削材に対応します。4枚刃エンドミルは、最大限の安定性と仕上げ面精度が得られるため、より硬い被削材や仕上げ加工に最適です。
正しいエンドミルの選択
2枚刃エンドミルと4枚刃エンドミルのどちらかを選択する場合は、以下の要素を考慮してください:
- 材質一般的に、柔らかい材料には2枚刃エンドミルが適していますが、硬い材料には4枚刃エンドミルが必要な場合があります。
- 加工タイプ荒加工には2枚刃エンドミルがよく使用され、仕上げ加工には4枚刃エンドミルがよく使用されます。
- 切りくず排出:切り屑の排出を重視する場合は、通常2枚刃エンドミルを使用します。
- 表面仕上げ:特に硬い被削材で優れた仕上げ面を得るには、4枚刃のエンドミルが好まれることが多い。
- 安定性:工具のたわみが懸念される用途では、4枚刃エンドミルの方が安定性が高い。
- 送り速度:送り速度を上げたい場合は、特に硬い被削材には4枚刃エンドミルの方が適している場合があります。
素材別推奨事項
- アルミニウム:2フルートまたは3フルート エンドミル は、切り屑の排出性から好まれることが多い。
- スチール: 4枚刃エンドミルは、その安定性と仕上げ面精度の高さから一般的に使用されています。
- 木材: 2枚刃エンドミルは、一般的に切りくず処理能力で推奨されます。
- プラスチック: 溶解を防ぎ、切りくずを適切に排出するため、通常は2枚刃のエンドミルを使用します。
結論
2枚刃エンドミルと4枚刃エンドミルの違いを理解することは、加工作業を最適化する上で非常に重要です。2枚刃エンドミルは切り屑排出と軟質材料の切削に優れていますが、4枚刃エンドミルは特に硬質材料の安定性と仕上げ面精度が向上します。
これら2つの構成のどちらを選択するかは、加工する材料、加工の種類、希望する仕上げ面、切り屑排出の要件など、様々な要因によって決まります。これらの要素を注意深く考慮し、各構成の長所と短所を理解することで、加工者は特定のアプリケーションに最適なエンドミルを選択することができ、最終的に生産性の向上、部品の品質向上、工具寿命の延長につながります。
機械加工には、万能のソリューションはありません。実験と経験によって、エンドミルの選択プロセスを微調整し、フライス加工で最高の結果を得ることができます。アルミニウム、スチール、木材、プラスチックのいずれを加工する場合でも、適切なエンドミル形状を選択することは、加工の成功に向けた重要なステップです。